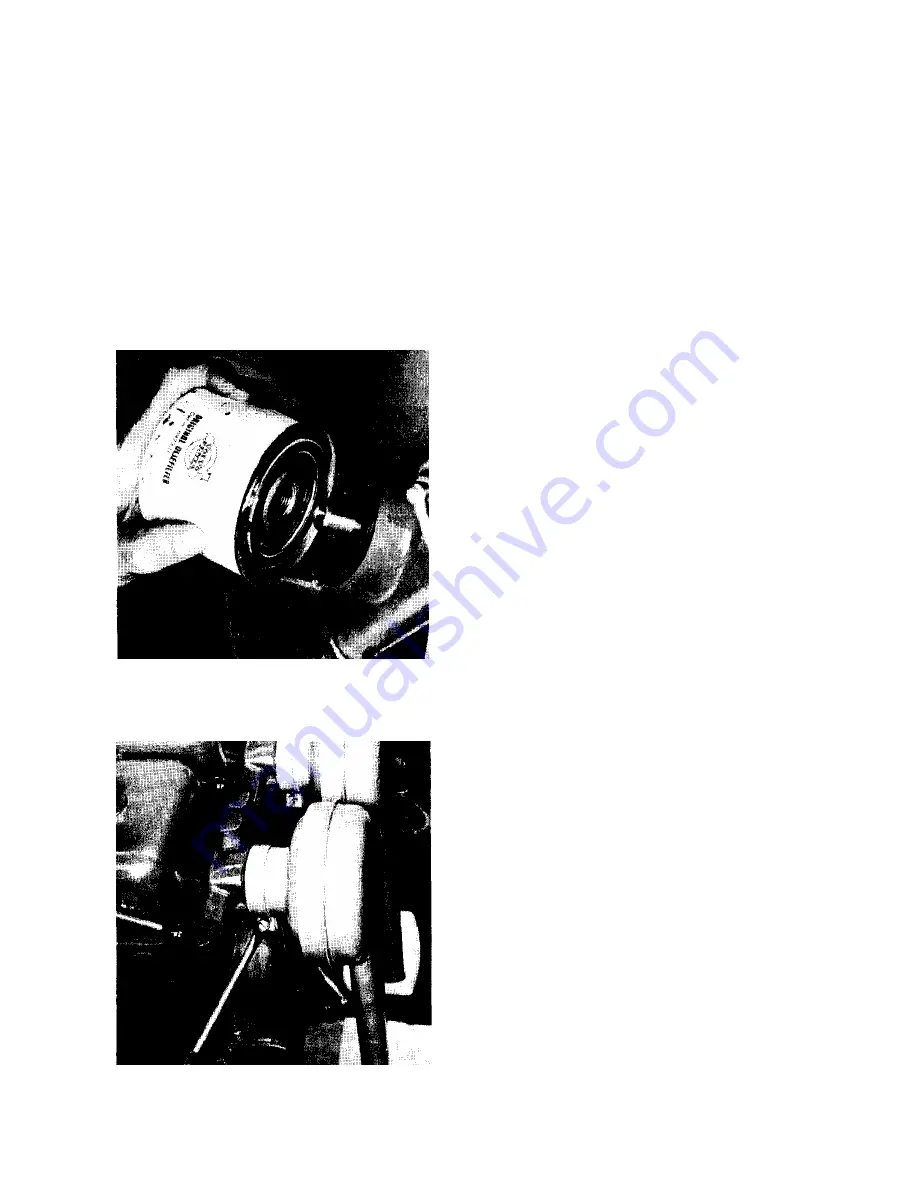
- 15 -
CHECKS AND SERVICE
SERVICE EVERY 100 HOURS OF OPERATION
OR AT LEAST ONCE EACH SEASON
OIL FILTER
The oil filter should be replaced for the first time after 20 hours of operation during the
running-in period and subsequently at every other oil change. Unscrew and discard
the oil filter.
Coat the new oil filter's rubber seal with oil.
Check the contact surface on the engine
and screw in the
filter by hand
until it
touches the contact surface. Turn the filter a
further
half turn, not more.
NOTE. Use only genuine oil filters.
Start the engine, run at idling and check that
the oil pressure lamp goes out.
Check oil level and that there are no leaks
from the oil filters contact surface.
CLEANING OF AIR FILTER
The air filter should be removed and
cleaned after every 100 hour operation
period or once per season. Loosen the
clamps with a screwdriver and remove the
filter.
Clean the filter with diesel fuel and blow it
clean with a compressed air gun. Soak
them in thin engine oil.
Let the engine oil drain and refit the filter.
Summary of Contents for MD 11C/110S
Page 1: ......
Page 34: ... 32 ENGINE COMPONENT GUIDE MD17C Reverse gear MSB For position explanation refer to page 31 ...
Page 36: ... 34 ENGINE COMPONENT GUIDE MD17C 110S For position explanation refer to page 33 ...
Page 42: ... 40 NOTES ...
Page 44: ... 42 Publ No 3167 July 1976 AB VOLVO PENTA S 405 08 GOTHENBURG SWEDEN ...