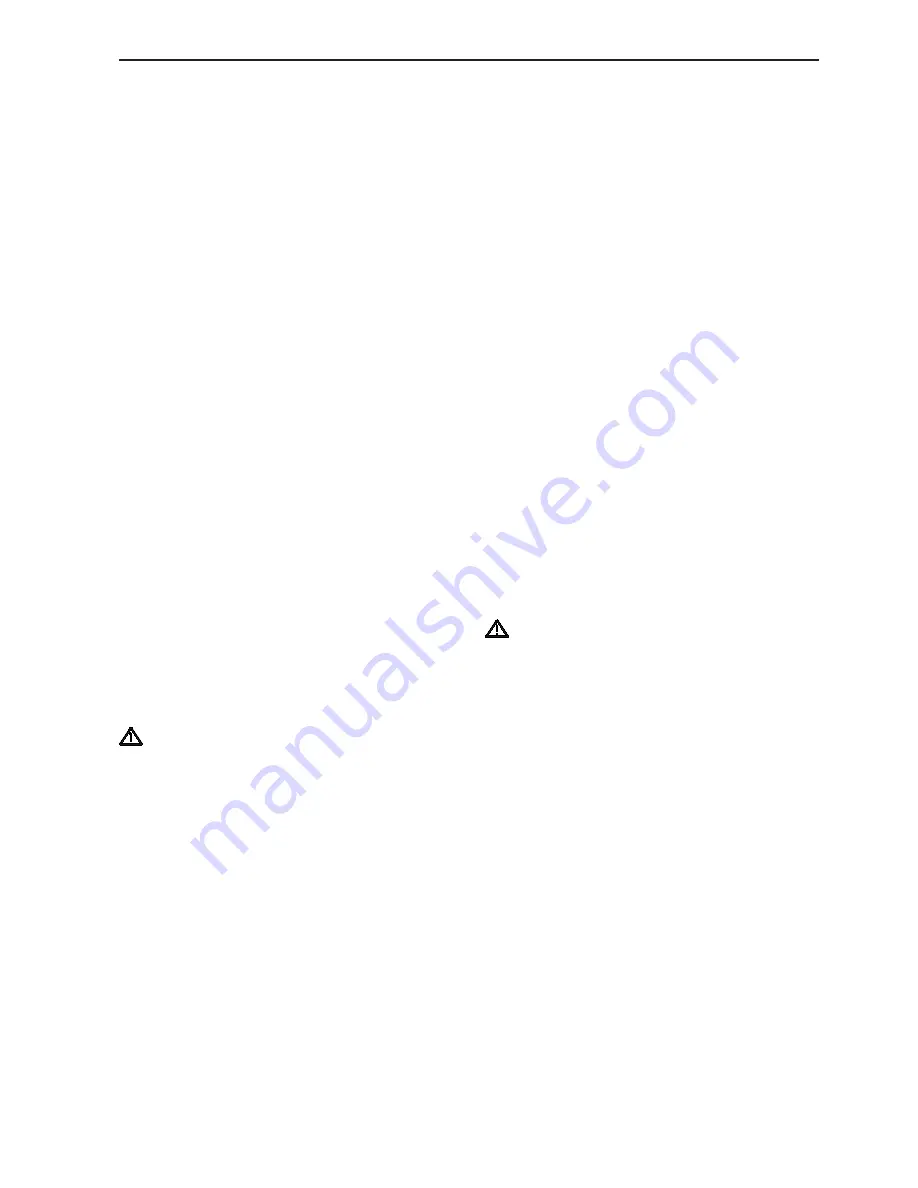
23
General
A condition test should be done before each major
service activity, if possible, to determine the general
condition of the engine and discovery any concurrent
fault causes. A condition test requires the engine to
be run, so this should be done before the engine or
any engine components are disassembled.
Please refer to “Condition test, engine”.
Repair instructions
Measures before overhaul in boat
1 Remove battery power.
2 Clean the outside of the engine.
NOTE!
Make sure that wash residue is collected
for destruction and does not inadvertently end up
in the water. Also refer to the warning text under
“Actions after lifting the engine”.
3 Work involving the cooling system: Close the sea
cocks and drain the coolant from the sea water
and fresh water systems.
WARNING!
Make sure that all sea water inlets
are securely closed, so that water cannot find
its way in during disassembly of cooling system
sub-components.
Actions before lifting the engine
from the boat
1 Lift the boat ashore.
2 Disconnect battery power, remove battery con-
nection on the starter motor.
3 Disconnect the engine-
instrument cable harness connector.
4 Disconnect the sea water connection/keel-cooling
connection.
5 Remove the exhaust system.
6 Close the fuel stopcocks. Remove the fuel con-
nections.
7 Disconnect the throttle and gearshift wires.
8 Disconnect the propshaft from the reverser. Undo
the engine mounting pads from the bed and lift the
engine out.
Actions after lifting the engine
1 Clean the engine.
IMPORTANT!
Remember the following when
washing with a power washer: Be extremely
careful when cleaning, to avoid getting water in-
side engine components. When a power washer
is used, the water jet must never be aimed at
seals, such as shaft seals, joints with gaskets,
rubber hoses or electrical components.
2 Drain the engine oil.
3 Remove the reverser (if required).
Summary of Contents for D2-55
Page 1: ...Workshop manual Group 20 23 26 30 A 2 0 D2 55 D2 75 ...
Page 2: ......
Page 103: ... References to Service Bulletins Group No Date Refers to ...
Page 104: ... Notes ...
Page 105: ... Notes ...
Page 106: ... Notes ...
Page 108: ...7742969 English 08 2006 ...