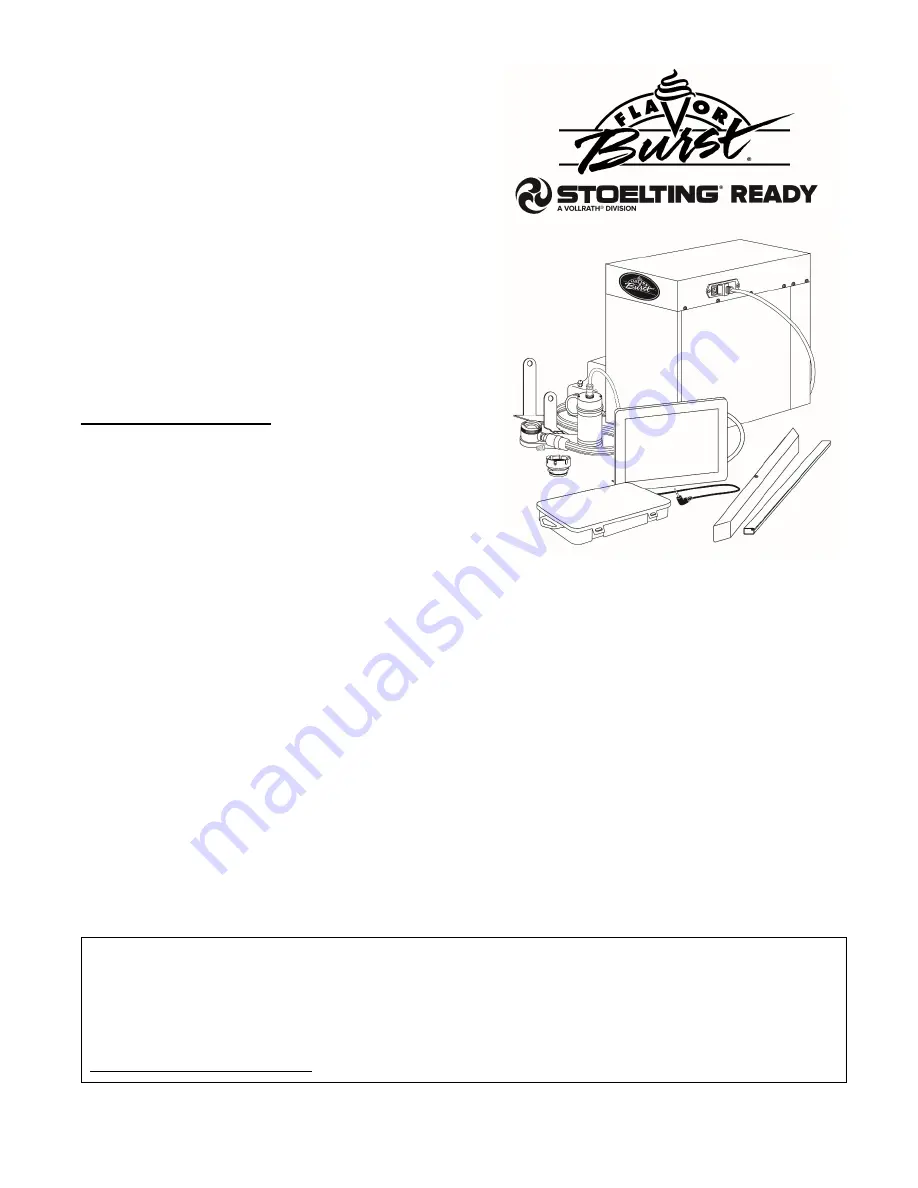
©2020 Flavor Burst Company Printed in September
Printed in
All Rights Reserved
The United States of America
Flavor Burst
®
Stoelting
®
Ready
4-Flavor Junior Soft Serve
“Blend” System
Model STL-40BLD-JR
Equipment, Maintenance and
Operations Manual
For questions, support, and ordering
parts, contact Stoelting Company’s
White Glove Service.
Phone: 1-800-319-9549
Warranty & Installation Form
An installation form is provided with every STL-40BLD-JR system, located inside the unit with this
manual. It is important that the operator / installer completely fill out the installation documents
accompanying the unit before using this system. Any questions or concerns regarding the warranty
should be clarified upon delivery or installation. For warranty details please refer to Stoelting’s website
www.stoeltingfoodservice.com.
Summary of Contents for Stoelting Flavor Burst STL-40BLD-JR
Page 2: ......
Page 9: ...6 PAGE INTENTIONALLY LEFT BLANK ...
Page 11: ...8 General System Overview Figure 1 ...
Page 17: ...14 Syrup Pump and Related Parts Figure 4 ...
Page 23: ...20 Spare Parts Kit Figure 7 ...
Page 24: ...21 PAGE INTENTIONALLY LEFT BLANK ...
Page 36: ...33 PAGE INTENTIONALLY LEFT BLANK ...
Page 50: ...47 PAGE INTENTIONALLY LEFT BLANK ...
Page 73: ......
Page 74: ......