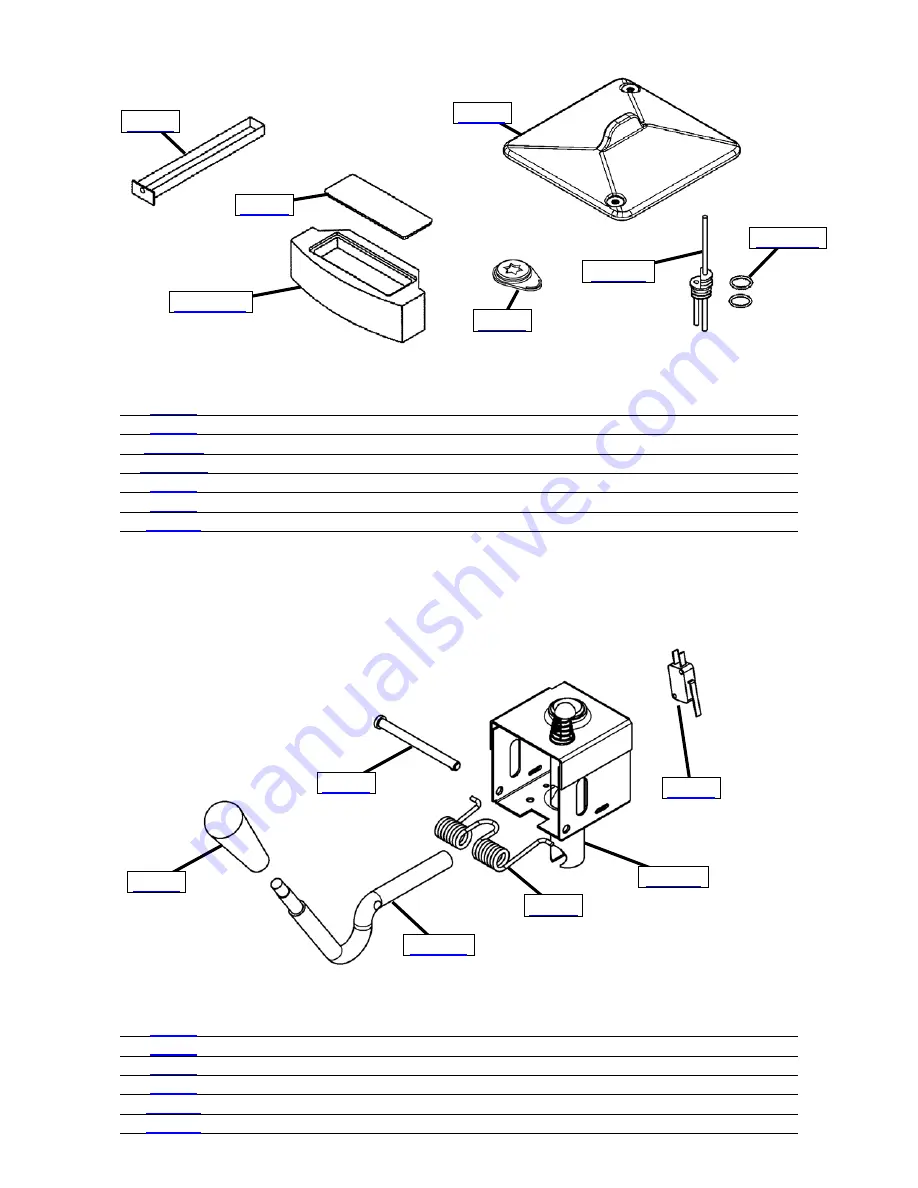
46
8.2
HOPPER COVER & TRAYS
8.3
SPIGOT CAM ASSEMBLY
Quantity
Part
Description
E111
F111
Cap - Rosette
1
1
Cover - Hopper
1
1
O-Ring - Mix Inlet - Black (5 Pack)
2
2
Tray - Drip
1
1
Insert - Drip Tray
1
1
Tray - Drain (Black Plastic)
1
1
Mix Inlet Assembly - 3/16" Hole - Standard Length (3A)
1
1
Quantity
Part
Description
E111
F111
Knob - Spigot Handle (Black)
1
1
Pin - Cotterless Clevis (Spigot Handle)
1
1
Spring - Torsion (Spigot Handle)
1
1
Switch - Spigot
1
1
Glide - Spigot Socket
1
1
Handle - Spigot (Metal Only)
1
1
Summary of Contents for Stoelting E111I
Page 1: ...Model E111I F111I SERVICE MANUAL Manual No 513663 Nov 2010...
Page 2: ......
Page 24: ...18...
Page 26: ...20 Figure 4 2 IntelliTec Control Menu Settings...
Page 46: ...40...
Page 57: ...51 8 9 WIRING DIAGRAMS...
Page 58: ...52...
Page 59: ...53...
Page 60: ......