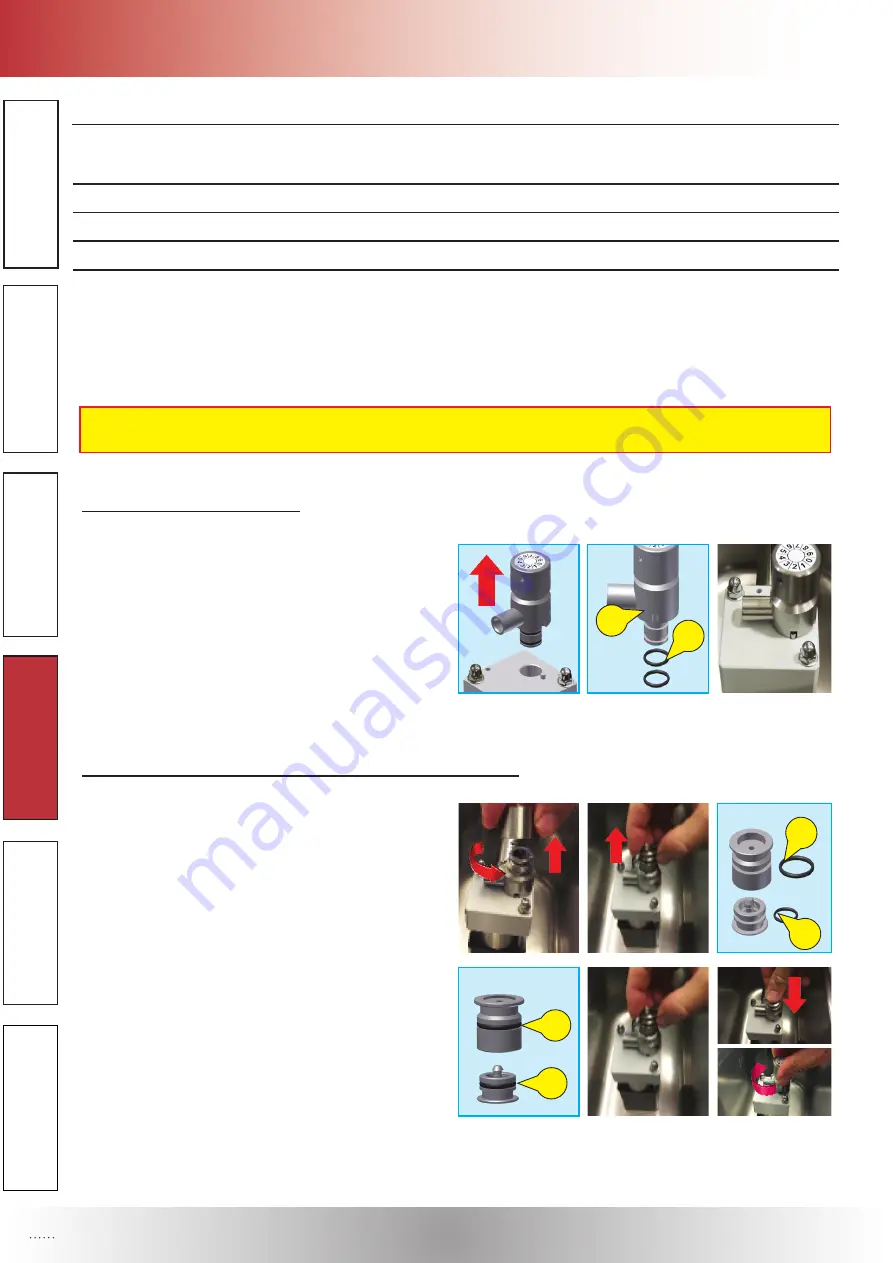
Section 4 :
Maintenance
OPERATOR’S MANUAL
18
MAINTENANCE
P
Replacing the gaskets
CHECKING INTERVAL: 500 hours or quarterly
AUTHORISED OPERATOR: 1 Operator
TIME NEEDED: 5 minutes
TOOL: Non-metallic pointy tool
- Regularly check the integrity of the gaskets and substitute them if they are broken, worn or swollen.
- Only use original gaskets, made of food-safe rubber.
- The machine is supplied with a full set of spare gaskets and food grease tube.
DO NOT PUT GASKETS IN THE INDUSTRIAL DISHWASHER, AS THE HIGH TEMPERATURES
COULD DEFORM THEM, MAKING THEM UNUSABLE.
a) Gaskets of the air-regulator:
• Remove the air-regulator from the pump cover. Re-
move the worn gaskets OR (1) from the air-regulator
(2), using a non-metallic pointy tool, taking care not
to scratch the gaskets’ seats.
•
Remove all product residues from the seats and fit
the new gaskets lubricating it with the food grease
supplied.
• Reassemble the air-regulator on the pump cover.
b) Gaskets of the valve socket and of the air regulating valve:
• Screw the air-regulator knob counterclockwise and
remove the valve socket vertically and air valve from
the air regulator body.
• Remove the worn gaskets OR (3) from valve socket
and air valve (4) using a non-metallic pointy tool, tak-
ing care not to scratch the gaskets’ seats.
•
Remove all product residues from the seat and fit
the new gaskets (5-6), lubricating them with the food
grease supplied. Place the valve socket and reas-
semble air valve inside the air regulator body, turn
clockwise the air regulator knob on air regulator body.
1
2
3
4
5
6