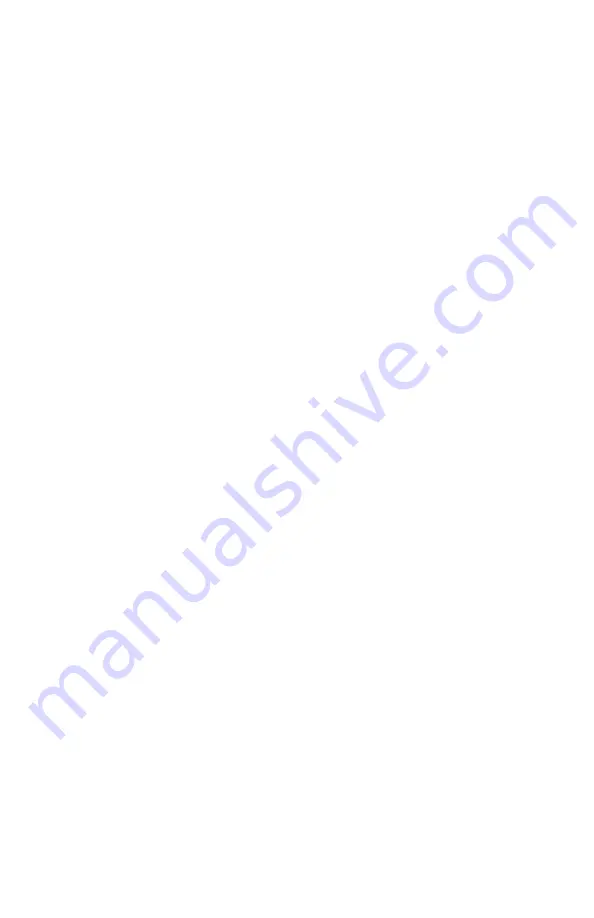
VMAC
– Vehicle Mounted Air Compressors
Toll Free:
1-800-738-8622 Local: 1-250-740-3200
Fax: 1-250-740-3201
36
FACTORY RESET
All adjustable parameters will reset to factory settings.
Pressing ENTER on this screen will display CANCEL
Pressing NEXT will show CONFIRM RESET? Pressing BACK will
display CANCEL again
Select the desired option and press the ENTER button
Summary of Contents for RAPTAIR-MF D600007
Page 2: ......
Page 62: ...This page intentionally left blank...
Page 64: ...This page intentionally left blank...
Page 65: ...This page intentionally left blank...
Page 66: ...This page intentionally left blank...
Page 67: ......
Page 68: ......