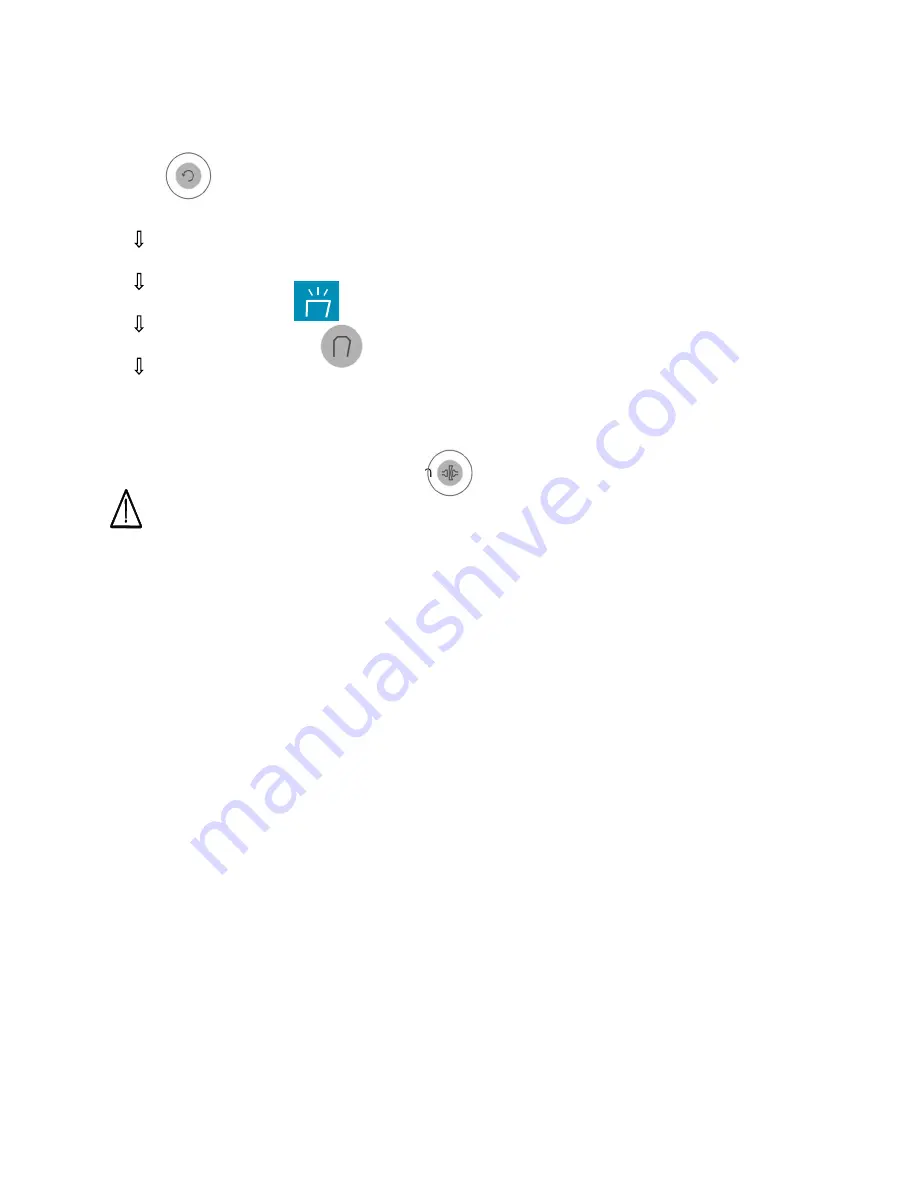
6) Push again and start edging.
Rough edging
Delicate edging
Polishing (When choose )
Chamfering (When choose )
Edging is done( switched to home)
7) Pull complete lens out
Open sliding cover and take the lens , push
key and pull lens out.
Warning
Pull lens out after opening sliding cover and the wheel is stopped throughly.
The operator may be able to be injured by the breakage or broken frictions
when lens is fallen to wheel if take the chuck off on condition that wheel
is not stopped throughly.