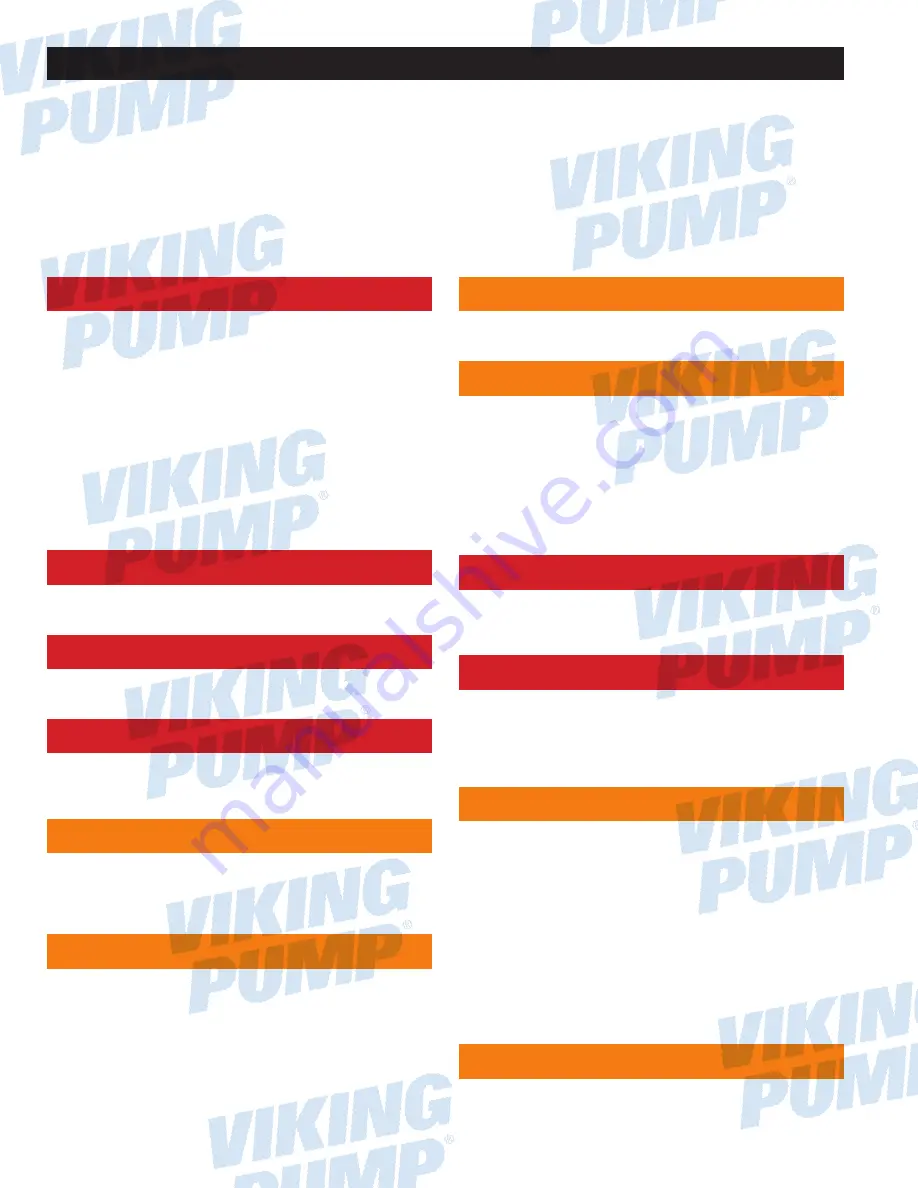
SAFETY INFORMATION & INSTRUCTIONS
IMPROPER INSTALLATION, OPERATION OR MAINTENANCE
OF PUMP MAY CAUSE SERIOUS INJURY OR DEATH, AND/OR
RESULT IN DAMAGE TO PUMP AND/OR OTHER EQUIPMENT.
VIKING’S WARRANTY DOES NOT COVER FAILURE DUE TO
IMPROPER INSTALLATION, OPERATION OR MAINTENANCE.
THIS INFORMATION MUST BE FULLY READ BEFORE
BEGINNING INSTALLATION, OPERATION OR MAINTENANCE
OF PUMP, AND MUST BE KEPT WITH PUMP. PUMP MUST BE
INSTALLED, OPERATED AND MAINTAINED ONLY BY SUITABLY
TRAINED AND QUALIFIED PERSONS.
THE FOLLOWING SAFETY INSTRUCTIONS MUST BE FOLLOWED AND ADHERED TO AT ALL TIMES.
⚠
DANGER = FAILURE TO FOLLOW THE INDICATED
INSTRUCTION MAY RESULT IN SERIOUS INJURY
OR DEATH.
⚠
WARNING = IN ADDITION TO SERIOUS INJURY OR DEATH,
FAILURE TO FOLLOW THE INDICATED INSTRUCTION MAY
CAUSE DAMAGE TO PUMP AND/OR OTHER EQUIPMENT
⚠
WARNING
INSTALL
pressure gauges/sensors next to the pump suction
and discharge connections to monitor pressures.
⚠
WARNING
USE
extreme caution when lifting the pump. Suitable lifting
devices should be used when appropriate. Lifting eyes
installed on the pump must be used only to lift the pump, not
the pump with drive and/or base plate. If the pump is mounted
on a base plate, the base plate must be used for all lifting
purposes. If slings are used for lifting, they must be safely and
securely attached. For weight of the pump alone (which does
not include the drive and/or base plate) refer to the Viking
Pump
®
product catalog.
⚠
DANGER
DO NOT
attempt to dismantle a pressure relief valve that has
not had the spring pressure relieved or is mounted on a pump
that is operating.
⚠
DANGER
AVOID
contact with hot areas of the pump and/or drive.
Certain operating conditions, temperature control devices
(jackets, heat-tracing, etc.), improper installation, improper
operation, and improper maintenance can all cause high
temperatures on the pump and/or drive.
⚠
WARNING
THE PUMP
must be provided with pressure protection. This
may be provided through a relief valve mounted directly on
the pump, an in-line pressure relief valve, a torque limiting
device, or a rupture disk. If pump rotation may be reversed
during operation, pressure protection must be provided on
both sides of pump. Relief valve adjusting screw caps must
always point towards suction side of the pump. If pump
rotation is reversed, position of the relief valve must be
changed. Pressure relief valves cannot be used to control
pump flow or regulate discharge pressure. For additional
information, refer to
Appendix
,
General Installation Notes
,
item 5 on Pressure Protection or contact your Viking Pump
®
representative for Engineering Service Bulletin ESB-31.
⚠
WARNING
THE PUMP
must be installed in a manner that allows safe
access for routine maintenance and for inspection during
operation to check for leakage and monitor pump operation.
⚠
DANGER
BEFORE
opening any liquid chamber (pumping chamber,
reservoir, relief valve adjusting cap fitting, etc.) be sure that:
• Any pressure in the chamber has been completely vented
through the suction or discharge lines or other appropriate
openings or connections.
• The pump drive system (motor, turbine, engine, etc.) has
been “locked out” or otherwise been made non-operational,
so that it cannot be started while work is being done on
the pump.
• You know what material the pump has been handling,
have obtained a material safety data sheet (MSDS) for
the material, and understand and follow all precautions
appropriate for the safe handling of the material.
⚠
DANGER
BEFORE
operating the pump, be sure all drive guards are in
place.
⚠
DANGER
DO NOT
operate pump if the suction or discharge piping is
not connected.
⚠
DANGER
DO NOT
place fingers into the pumping chamber, or its
connection ports, or into any part of the drive train if there is
any possibility of the pump shaft being rotated.
⚠
WARNING
DO NOT
exceed the pumps rated pressure, speed, and
temperature, or change the system/duty parameters from
those the pump was originally supplied, without confirming its
suitability for the new service.
⚠
WARNING
BEFORE
operating the pump, be sure that:
• It is clean and free from debris.
• All valves in the suction and discharge pipelines are fully
opened.
• All piping connected to the pump is fully supported and
correctly aligned with the pump.
•
Pump rotation is correct for the desired direction of flow.
TSM 1741 | Issue B | Page 2 of 20
© 2019 Viking Pump, Inc. • Cedar Falls, IA
© Viking Pump, Inc.
© Viking Pump, Inc.
© Viking Pump, Inc.
© Viking Pump, Inc.
© Viking Pump, Inc.
© Viking Pump, Inc.
© Viking Pump, Inc.
© Viking Pump, Inc.
© Viking Pump, Inc.
© Viking Pump, Inc.
© Viking Pump, Inc.
© Viking Pump, Inc.
© Viking Pump, Inc.
© Viking Pump, Inc.
© Viking Pump, Inc.
© Viking Pump, Inc.
© Viking Pump, Inc.
© Viking Pump, Inc.
© Viking Pump, Inc.
© Viking Pump, Inc.
© Viking Pump, Inc.
© Viking Pump, Inc.
© Viking Pump, Inc.
© Viking Pump, Inc.