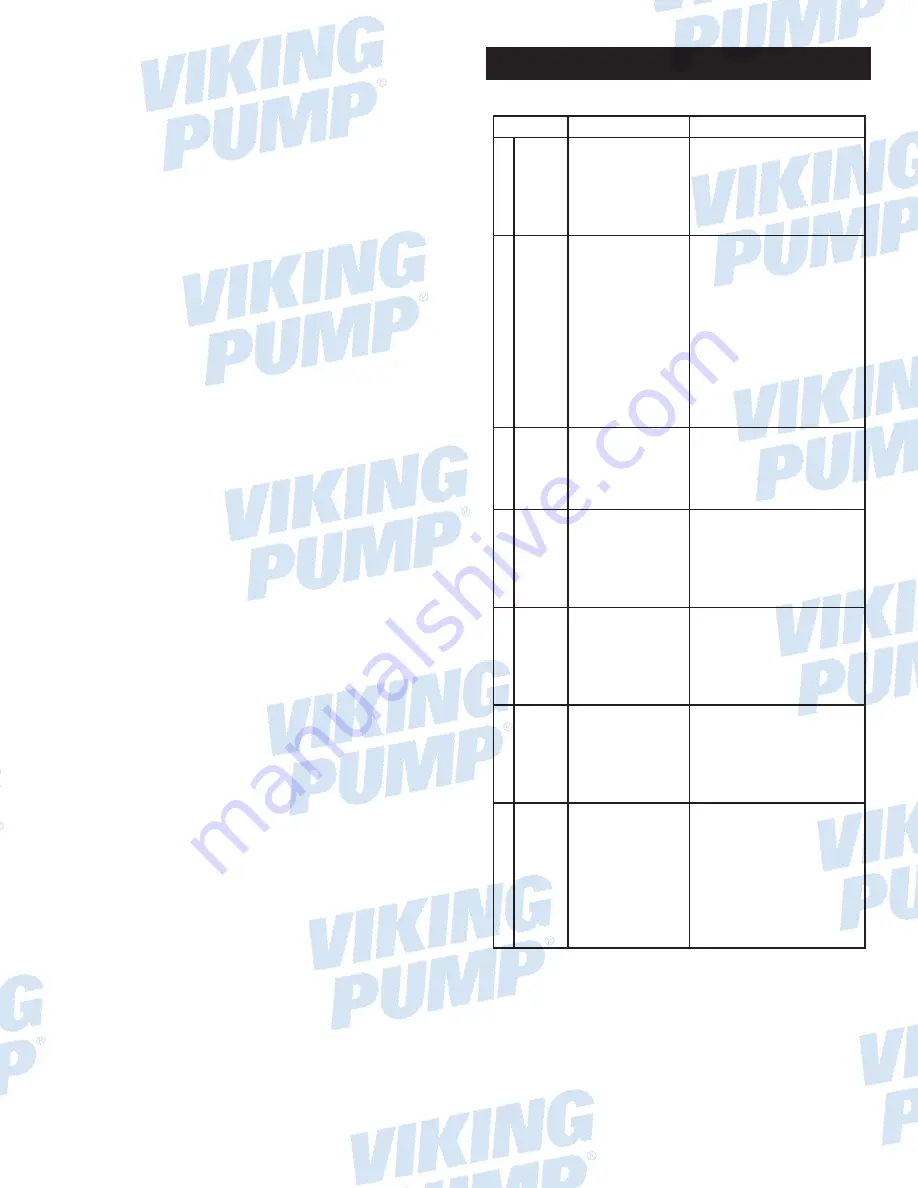
C. Pump is noisy.
1.
Pump is being starved (heavy liquid cannot get to
pump fast enough). Increase suction pipe size or
reduce length.
2.
Pump is cavitating (liquid vaporizing in the suction
line). Increase suction pipe size or reduce length. If
pump is above the liquid, raise the liquid level closer to
the pump. If the liquid is above the pump, increase the
head of liquid.
3.
Check alignment.
4.
May have a bent shaft or rotor tooth. Straighten or replace.
5.
Relief valve chatter. Increase pressure setting.
6.
May have to anchor base or piping to eliminate or
reduce vibration.
7.
May be a foreign object trying to get into the pump
through the suction port.
8. Mag Drive pumps ONLY:
The magnetic coupling has
decoupled. Shut off and let cool, then restart.
D. Pump not up to capacity.
1.
Starving or cavitating. Increase suction pipe size or
reduce length.
2.
Strainer partially clogged.
3.
Air leak in suction piping or along pump shaft.
4.
Running too slowly. Check the motor is running at the
correct speed and that it is wired correctly.
5.
Bypass line around pump partially open.
6.
Relief valve set too low or stuck open.
7.
Pump is worn out.
8.
Too much end clearance.
9.
Head position incorrect. See
Figure A3
.
E. Pump takes too much power.
1.
Running too fast. Verify the motor speed, reducer ratio,
sheave size, and other drive components are correct
for the application?
2.
The liquid is too viscous for the size of the unit. Heat
the liquid to reduce viscosity, increase the pipe size,
slow down the pump, or use a larger motor.
3.
Discharge pressure higher than calculated. Verify with
a pressure gauge. Increase size or reduce length of
pipe, reduce speed (capacity), or get bigger motor.
4.
Packing gland drawn down too tight.
5.
Pump misaligned.
6.
Extra clearance on pumping elements may not be
sufficient for operating conditions. Check parts for
evidence of drag or contact in pump and increase
clearance where necessary.
7.
System pressure relief valve is set too high.
8.
Bushings have locked to shaft or pin, or the liquid has
set up in the pump.
F. Rapid Wear.
On most applications the pump will operate for many
months or years before it gradually loses its ability to
deliver capacity or pressure. Examination of such a pump
would show a smooth wear pattern on all parts. Rapid
wear, occurring in a few minutes, hours or days, shows
up as heavy grooving, galling, twisting, breaking or similar
severe signs of trouble. See
Rapid Wear Table
.
RAPID WEAR
RAPID WEAR TABLE
CAUSE
EVIDENCE
POSSIBLE SOLUTION
1
ABRASIVES
Gouges or marks made
by large, hard particles;
a rapid wearing away
of bushings from very
small abrasives; or
anything in between.
Flush the system with the pump
removed. Install strainer in suction
line. Most abrasive objects and
particulate is removed after a few
cycles (or days) of flushing.
2
CORROSION
Rust, pitting or metal
appears to be “eaten”
away.
Check the Viking General
Catalog Liquid List for materials
of construction recommendation.
Consider whether all of the
materials used in pump
construction were attacked;
consider other materials used in
the system to determine how they
resisted the liquid. Check to see
whether or not the liquid has been
contaminated to make it more
corrosive than anticipated.
3
EXCEEDING
OPERA
TING
LIMITS
Noisy operation,
broken bushings,
twisted shaft, parts
show evidence of high
heat (discoloration).
Review General Catalog for
operating limits on particular model
involved.
4
INSUFFICIENT
EXTRA
CLEARANCE
Pump may stall.
Evidence of heavy
contact between end of
rotor teeth and head or
other parts.
Increase end clearance and/
or contact your Viking Pump
®
representative with details of the
application, so that information
regarding proper extra clearance
may be provided.
5
LACK OF
LUBRICA
TION
Noisy bearings,
localized heating at
bearings or lip seal,
smoke, rapid bushing
wear.
Be sure all grease fittings are
greased before starting, and
instructions for lubrication of
drive equipment are followed;
consider use of auxiliary lubricating
equipment.
6
MISALIGNMENT
Wear on only one part
of a surface, e.g., one
side of the casing, one
side of the packing
gland, only a portion of
the face of the head.
Double check alignment of drive
equipment and piping. Check the
alignment under conditions as
close to operating conditions as
possible.
7
RUN DR
Y
Pump stalls because
parts have uneven
expansion caused by
frictional heat; galling
between surfaces
having relative motion;
seal seats and idler
pins changing color
because of high heat.
Be sure there is liquid in the
system at the time of start up.
Provide some kind of automatic
alarm or shut-off if supply tank
runs dry.
TSM 1741 | Issue B | Page 17 of 20
© 2019 Viking Pump, Inc. • Cedar Falls, IA
© Viking Pump, Inc.
© Viking Pump, Inc.
© Viking Pump, Inc.
© Viking Pump, Inc.
© Viking Pump, Inc.
© Viking Pump, Inc.
© Viking Pump, Inc.
© Viking Pump, Inc.
© Viking Pump, Inc.
© Viking Pump, Inc.
© Viking Pump, Inc.
© Viking Pump, Inc.
© Viking Pump, Inc.
© Viking Pump, Inc.
© Viking Pump, Inc.
© Viking Pump, Inc.
© Viking Pump, Inc.
© Viking Pump, Inc.
© Viking Pump, Inc.
© Viking Pump, Inc.
© Viking Pump, Inc.
© Viking Pump, Inc.
© Viking Pump, Inc.
© Viking Pump, Inc.
© Viking Pump, Inc.
© Viking Pump, Inc.
© Viking Pump, Inc.
© Viking Pump, Inc.
© Viking Pump, Inc.
© Viking Pump, Inc.
© Viking Pump, Inc.
© Viking Pump, Inc.