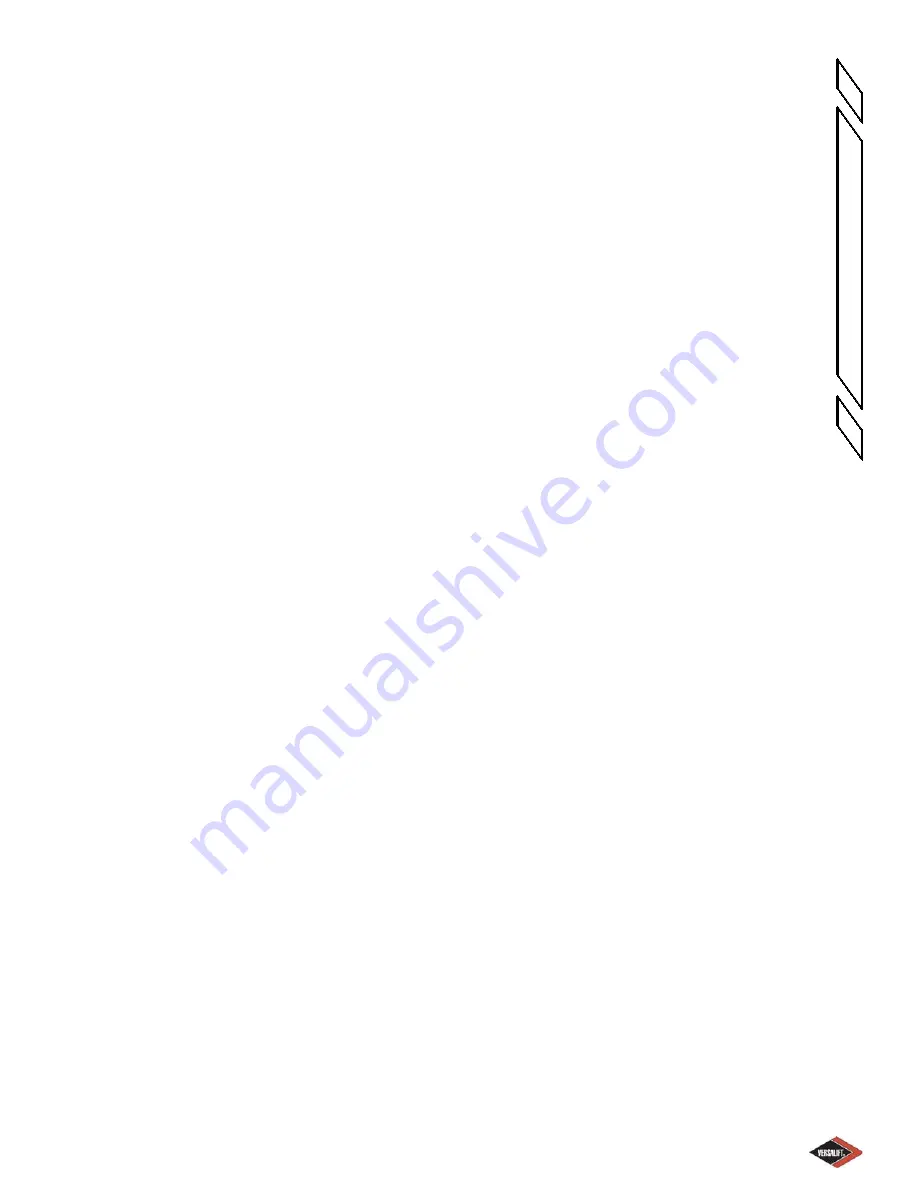
i
39026-03 02/17
VERSALIFT VST-8000/8500/9000/9500-I
TABLE OF CONTENTS
TABLE OF CONTENTS
Introduction
Section 1
Manual Structure ........................................................................................................................ 1-1
Additional Manual Features ........................................................................................................ 1-1
Nomenclature ............................................................................................................................. 1-2
Responsibilities / Safety
Section 2
Responsibilities of Dealers, Owners, Users, Operators, Lessors, and Lessees ........................ 2-1
Decals ......................................................................................................................................... 2-2
Think Safety ................................................................................................................................ 2-6
What is Insulated and What is not Insulated .............................................................................. 2-9
Additional Safety Considerations .............................................................................................. 2-10
Specifi cations
Section 3
General Specifi cations ................................................................................................................ 3-1
Option Specifi cations .................................................................................................................. 3-2
Dimensional Specifi cations ......................................................................................................... 3-5
Vehicle Specifi cations ............................................................................................................... 3-17
Operation
Section 4
Positioning the Versalift for Operation ....................................................................................... 4-1
Aerial Lift Operations .................................................................................................................. 4-2
Cab Control Operation ............................................................................................................... 4-4
Ground Control Operation ......................................................................................................... 4-4
Lower Control Operation ........................................................................................................... 4-6
Upper Control Operation ............................................................................................................ 4-6
Storing the Aerial Lift ................................................................................................................. 4-8
Lifting Eye ................................................................................................................................... 4-9
Manual Jib Operation ............................................................................................................... 4-10
Hydraulic Jib Operation ............................................................................................................ 4-12
Jib Capacity Determination ....................................................................................................... 4-12
Emergency Operation
Section 5
Daily Visual Inspection
Section 6
Summary of Contents for VST-8000-I
Page 2: ......
Page 4: ......
Page 6: ......
Page 11: ...2 3 39026 03 02 17 VERSALIFT VST 8000 8500 9000 9500 I RESPONSIBILITIES SAFETY ...
Page 12: ...2 4 39026 03 02 17 VERSALIFT VST 8000 8500 9000 9500 I RESPONSIBILITIES SAFETY ...
Page 13: ...2 5 39026 03 02 17 VERSALIFT VST 8000 8500 9000 9500 I RESPONSIBILITIES SAFETY ...
Page 24: ...3 6 39026 03 02 17 VERSALIFT VST 8000 8500 9000 9500 I SPECIFICATIONS ...
Page 26: ...3 8 39026 03 02 17 VERSALIFT VST 8000 8500 9000 9500 I SPECIFICATIONS ...
Page 28: ...3 10 39026 03 02 17 VERSALIFT VST 8000 8500 9000 9500 I SPECIFICATIONS ...
Page 30: ...3 12 39026 03 02 17 VERSALIFT VST 8000 8500 9000 9500 I SPECIFICATIONS ...
Page 31: ...3 13 39026 03 02 17 VERSALIFT VST 8000 8500 9000 9500 I SPECIFICATIONS ...
Page 32: ...3 14 39026 03 02 17 VERSALIFT VST 8000 8500 9000 9500 I SPECIFICATIONS ...
Page 33: ...3 15 39026 03 02 17 VERSALIFT VST 8000 8500 9000 9500 I SPECIFICATIONS ...
Page 34: ...3 16 39026 03 02 17 VERSALIFT VST 8000 8500 9000 9500 I SPECIFICATIONS ...
Page 36: ...3 18 39026 03 02 17 VERSALIFT VST 8000 8500 9000 9500 I SPECIFICATIONS ...
Page 37: ...3 19 39026 03 02 17 VERSALIFT VST 8000 8500 9000 9500 I SPECIFICATIONS ...
Page 38: ...3 20 39026 03 02 17 VERSALIFT VST 8000 8500 9000 9500 I SPECIFICATIONS ...
Page 39: ...3 21 39026 03 02 17 VERSALIFT VST 8000 8500 9000 9500 I SPECIFICATIONS ...
Page 40: ......
Page 54: ......
Page 62: ...6 4 39026 03 02 17 VERSALIFT VST 8000 8500 9000 9500 I DAILY VISUAL INSPECTION ...
Page 63: ...6 5 39026 03 02 17 VERSALIFT VST 8000 8500 9000 9500 I DAILY VISUAL INSPECTION ...
Page 64: ...6 6 39026 03 02 17 VERSALIFT VST 8000 8500 9000 9500 I DAILY VISUAL INSPECTION ...