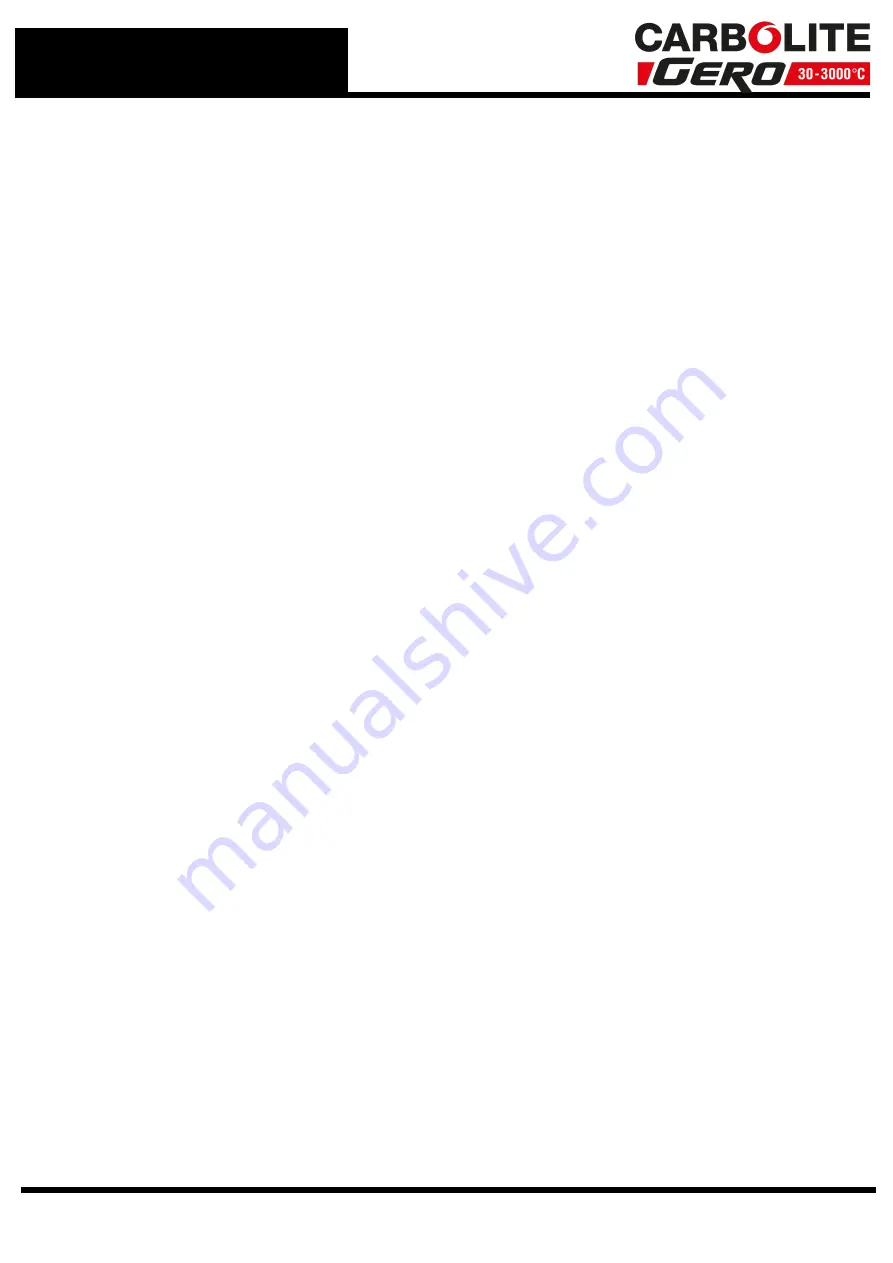
5.5.2
Cleaning the Window
When cleaning the window, use a suitable cleaning agent. Alternatively an optician
equipped with re-polishing machines can restore the clarity of the windows.
5.5.3
When Replacing the Window
Ensure that the glass is clean and free from dust, grit, chips, scratches and cracks. If the
glass is damaged replace it, a faulty window glass can cause leakage of carbon
monoxide during testing. See section 1.2.
Inspect the condition of the window 'O' ring seal, it must be uniform in shape and
section, and free from cuts, cracks, dust and grit. If the seal is damaged replace it, a
faulty seal can cause leakage of carbon monoxide during testing.
Clean the inside of the viewing window retaining ring and door plug ring. Pay particular
attention to the 'O' ring seal faces, these must also be free from dust, grit, chips and
scratches. A vacuum cleaner is the best method of removing the dust and grit. Take
care not to damage the back face of the door plug during cleaning.
Fit a new window glass gasket, if this gasket is not fitted the window glass will break
when the window retaining ring is tightened.
Fit the window 'O' ring seal onto the window retaining ring. Place the window glass in
position in the door plug ring and re-fit the window retaining ring and tighten the window
retaining ring to finger tight.
Using the tool provided tighten the window retaining ring to seal the viewing window.
Whilst tightening the window retaining ring hold the door plug in position to prevent it
from rotating, the gas inlet hole in the door plug must line up with the gas inlet in the
work tube front seal assembly. See fig 17.
Prior to using the furnace conduct a pressure test of the work tube assembly to ensure
integrity of the work tube and 'O' ring seals, see section 3.3.5.
5.6
Furnace Calibration
This procedure describes the process required to achieve correct calibration and
performance from your CAF G5 furnace. The furnace is calibrated prior to leaving the
factory, but all test standards call for regular checks on calibration. Carbolite Gero
recommend that calibration checks are conducted in accordance with these standards, if
the furnace is found to be out of calibration then the control instrument must be
adjusted (see section 5.7).
5.6.1
Sample Carrier Tiles
To obtain an accurate calibration result the correct sample carrier and tiles supplied with
the furnace must be used.
5.6.2
Sample Preparation
Two types of wire are used to check the furnace calibration:
Gold Wire
Melting Point 1063 °C
Palladium Wire
Melting Point 1554 °C
50
Summary of Contents for CARBOLITE GERO CAF G5
Page 63: ...Fig 3 Front Tube Seal Assembly Fig 4 Door Arm Assembly 63 ...
Page 64: ...Fig 5a Camera Mounting Bracket Fig 5b Lens and Camera Assembly 64 ...
Page 65: ...Fig 5c Sliding the Camera Mounting Bracket Assembly onto the Door Arm 65 ...
Page 66: ...Fig 5d Securing the Camera Mounting Bracket Assembly to the Door Arm 66 ...
Page 67: ...Fig 5e Mounting the Lens and Camera Assembly 67 ...
Page 68: ...Fig 5f Lens and Camera Assembly in Position 68 ...
Page 69: ...Fig 6a Rear View of the Standard CAF G5 Furnace Showing Brick Box Assembly 69 ...
Page 71: ...Fig 7 Front Tube Seal Position 71 ...
Page 72: ...Fig 8 Tube End Seal Assembly Tightening Sequence Fig 9 Work Tube Front Support 72 ...
Page 73: ...Fig 10 Fitting the Door Arm Assembly Fig 10a Adjusting the Door Arm Assembly 73 ...
Page 74: ...Fig 11a Furnace Case and Controls 74 ...
Page 75: ...Fig 11b Gas Inlet Pipe Fig 12 Positioning the Furnace 75 ...
Page 77: ...Fig 13c Loading Samples into the Work Tube 77 ...
Page 78: ...Fig 16 File Folder 78 ...
Page 79: ...Fig 17 Door Arm Assembly Exploded View 79 ...
Page 82: ...SST DT HT FT Fig 18 Report Sheet Page 2 Side View Plan View Fig 19 Formed Wire Sample 82 ...
Page 83: ...Fig 20 Sample Carrier Sample Tiles and Sample Positions 83 ...
Page 84: ...Fig 21a Coal and Coke Test Piece Mould Fig 21b Biomass Test Piece Mould and Hand Press 84 ...
Page 85: ...Fig 22 Sample Loading Tool Fig 23 Camera Ethernet Connection 85 ...
Page 86: ...Fig 24 LED Driver Connection 86 ...
Page 87: ...Notes Service Record Engineer Name Date Record of Work ...