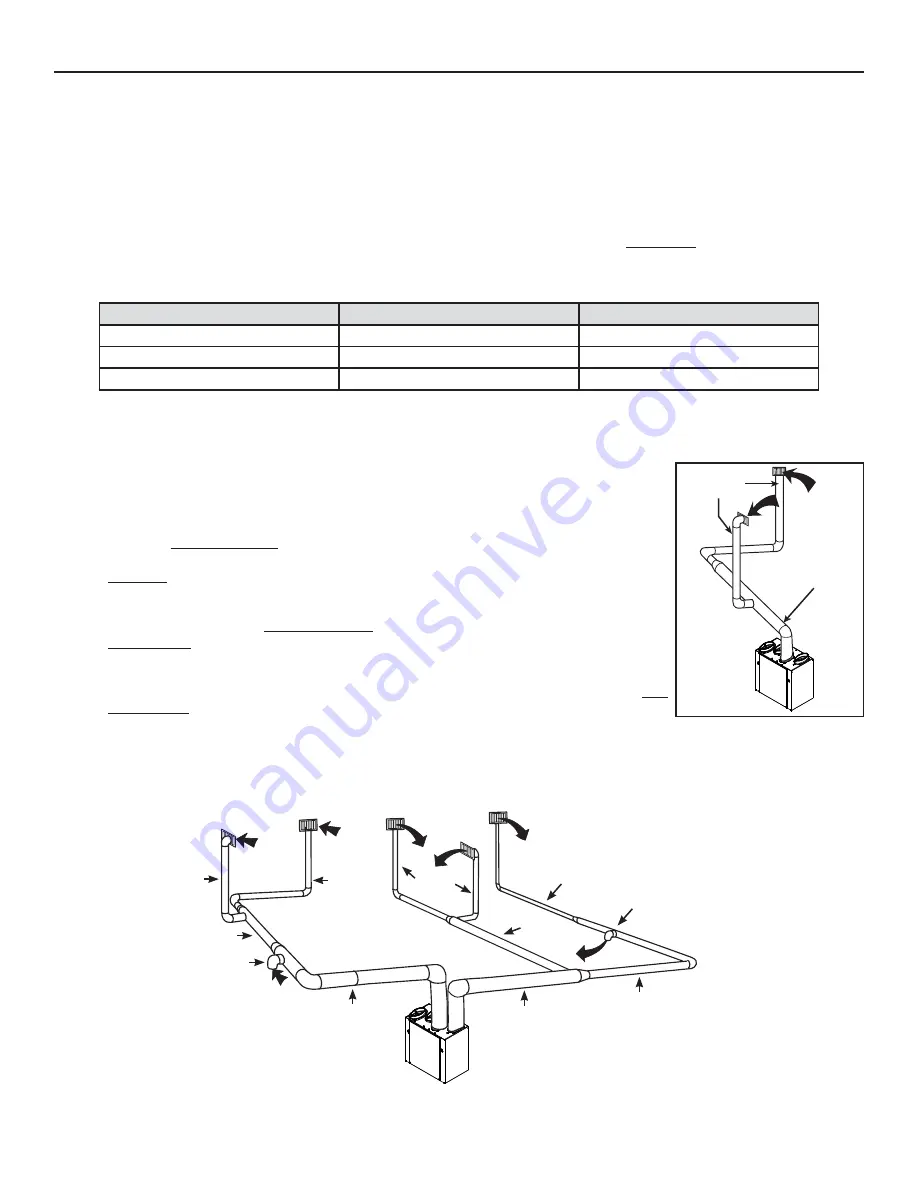
7
3. INSTALLATION
(
CONT
’
D
)
3.4 P
LANNING
OF
THE
D
UCTWORK
• Keep it simple. Plan for a minimum of bends and joints.
• Keep the length of insulated ducts to a minimum.
• Do not ventilate crawl spaces or cold rooms. Do not attempt to recover the exhaust air from a dryer or a range hood. This would cause
clogging of the filters and recovery module.
• If the house has two floors or more, be sure to plan for at least one exhaust register on the highest lived-in level.
3.5 C
ALCULATING
D
UCT
SIZE
Use the table below to ensure that the ducts you intend to install will be carrying air flows at or under the recommended values.
Avoid installing ducts that will have to carry air flows near the maximum values and never install a duct if its air flow exceeds
the maximum value.
D
UCT
D
IAMETER
R
ECOMMENDED
A
IR
F
LOW
M
AXIMUM
A
IR
F
LOW
4” Ø (102
MM
)
40
CFM
(19
L
/
S
OR
68
M
³/
H
)
60
CFM
(28
L
/
S
OR
102
M
³/
H
)
5” Ø (127
MM
)
75
CFM
(35
L
/
S
OR
127
M
³/
H
)
110
CFM
(52
L
/
S
OR
187
M
³/
H
)
6” Ø (152
MM
)
120
CFM
(57
L
/
S
OR
204
M
³/
H
)
180
CFM
(85
L
/
S
OR
306
M
³/
H
)
NOTE: Examples 3.5.1 and 3.5.2 use imperial units. The same calculation applies to metric units.
3.5.1
E
XAMPLE
OF
CALCULATION
Problem:
My installation requires two exhaust registers (one for the kitchen, and the other for
the bathroom). I will connect these registers to a main duct which will connect to the unit (high
speed performance value of 140 cfm). What size of duct should I use for the main exhaust duct
and for both end branches leading to the registers? (See illustration at right.)
Solution:
Simplified method. (For a more detailed method of calculating duct size, refer to the
ASHRAE or HRAI HANDBOOK.)
Main duct: Table indicates for a 6” Ø duct: recommended air flow: 120 cfm, maximum air flow:
180 cfm. The 140 cfm high speed air flow is close enough to the recommended value (120)
and far away enough from the maximum value (180). Therefore, a 6” Ø duct or larger is an
appropriate choice for the main exhaust duct.
End branches: Each end branch will have to transport a 70 cfm air flow (140 divided by 2). Table
indicates for a 5” Ø duct: recommended air flow: 75 cfm; maximum air flow: 110 cfm. The high
speed air flow of 70 cfm is close enough to the recommended value (75) and far away enough
from the maximum value (110). Therefore, a 5” Ø duct or larger is an appropriate choice for both
end branches.
NOTE: A 4” Ø duct would have been too small because the maximum acceptable value for a 4” Ø duct is 60 cfm.
3.5.2 Example of a design for a fully ducted system with a unit having a high speed performance of 160 cfm.
VI0016
E
ND
BRANCHES
M
AIN
BRANCH
6" Ø, 140
CFM
5" Ø,
70
CFM
VI0017
4" Ø, 47
CFM
5" Ø, 93
CFM
5" Ø, 67
CFM
4"
4"
4"
4"
4"
4"
4"
5"
5"
5"
5"
6"
6"
6" Ø, 160
CFM
6" Ø, 160
CFM
5" Ø, 86
CFM
5" Ø, 62
CFM
4" Ø, 24
CFM
4" Ø,
37
CFM
4" Ø,
46
CFM
5" Ø,
74
CFM