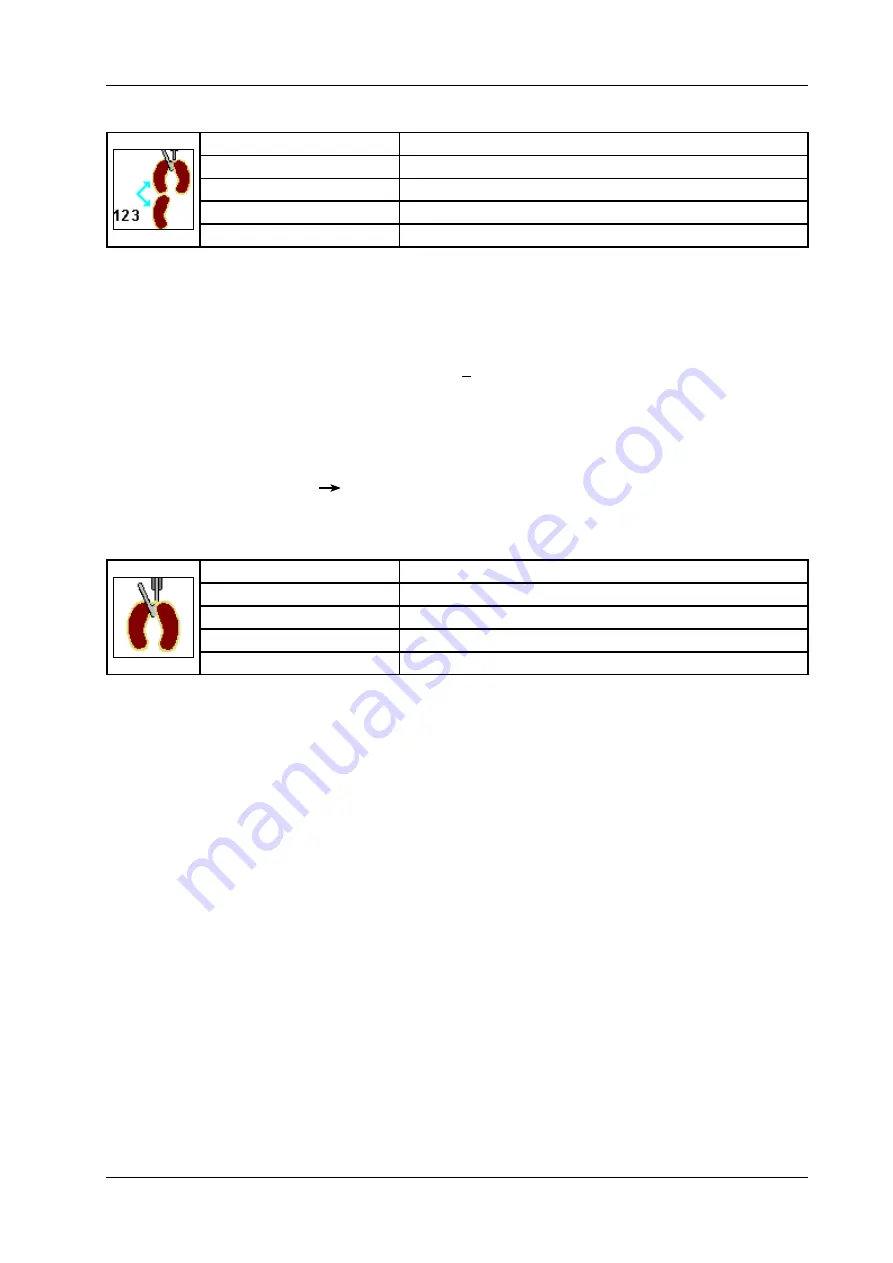
HP10E / HP12E / HP15E / HP20E - Dairy design
6. Graphical control
6-41
© VEMAG 2013
6.6.4.27 Sausages on last hook
Display:
Sausages on last hook
Unit:
Number
Resolution:
1
Setting range:
1 – 50
Application:
AH 204, AH 212
• Enter the number of sausages to hang on the last hook.
• Press
Enter
.
Conditions:
Stop counter switched off
„Hooks per stick“ defined
„Remaining portions“ > “Sausages per hook”
Put a tick in the “Tick” field to ensure that there is the same number of
sausages on each hook (= all loops on the smoke stick are the same)
once the machine has stopped (e.g. via natural casing end detection).
“Catch residue” (“Sausages per hook” parameter”) is only taken into con-
sideration for this in the event of cancellation (e.g. split casing).
Section 6.6.4.28
6.6.4.28 Sausages per hook
Display:
Sausages per hook / Catch residue
Unit:
Number
Resolution:
1
Setting range:
1 – 99
Application:
AH 204, AH 212
• Enter the number of sausages to hang between the hooks.
• Press
Enter
.
If you would like to hang rings, enter "1".
• If the last sausages in a casing are to be caught, even if they don’t
form a complete loop, enter a value in the “Catch residue” field.
Summary of Contents for HP10E
Page 8: ......
Page 10: ...HP10E HP12E HP15E HP20E Dairy design 0 Foreword 0 2 VEMAG 2013...
Page 26: ...HP10E HP12E HP15E HP20E Dairy design 3 Installation and commissioning 3 6 VEMAG 2013...
Page 34: ...HP10E HP12E HP15E HP20E Dairy design 4 Setting up 4 8 VEMAG 2013...
Page 38: ...HP10E HP12E HP15E HP20E Dairy design 5 Operation 5 4 VEMAG 2013...
Page 52: ...HP10E HP12E HP15E HP20E Dairy design 6 Graphical control 6 14 VEMAG 2013 Mode group Mode View...
Page 56: ...HP10E HP12E HP15E HP20E Dairy design 6 Graphical control 6 18 VEMAG 2013...
Page 58: ...HP10E HP12E HP15E HP20E Dairy design 6 Graphical control 6 20 VEMAG 2013...
Page 60: ...HP10E HP12E HP15E HP20E Dairy design 6 Graphical control 6 22 VEMAG 2013...
Page 97: ...HP10E HP12E HP15E HP20E Dairy design 6 Graphical control 6 59 VEMAG 2013...
Page 100: ...HP10E HP12E HP15E HP20E Dairy design 6 Graphical control 6 62 VEMAG 2013...