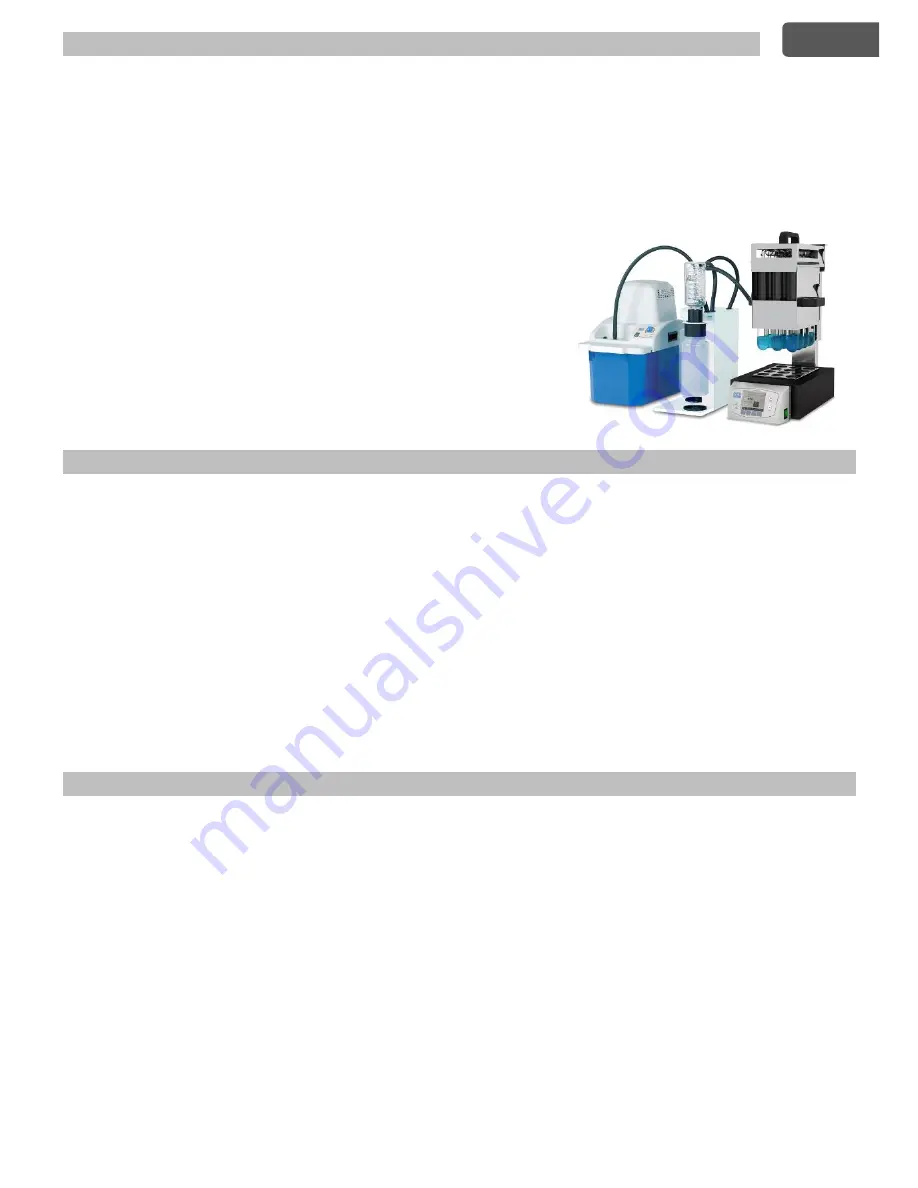
4
1. Introduction
The use of water jet pumps connected to tap is often impeded by a lack of pressure or by their consume which ranges
between 200 and 400 L/h. JP is composed by a plastic water tank in which an impeller driven by an electric motor forces the
water into four water jets developing suction. The water is continuously recirculated and its consumption is nil.
For the movement of equipment use the two handles located in front and rear of the tank. To remove the motor from tank
use the two lateral handles located on the plastic cover. In the upper part of the instrument a tube holder connects to the
internal Venturi ejectors which produce a maximum air flow of 35 l/minute.
The air flow can be regulated from 15 to 35 l/minute by the proper knob. The lateral tube holder can be connected to a
plastic tube for sending residual traces of not neutralized gases to a fume hood or to outside environment. The pump is
equipped by a handy door for the introduction of water and a level indicator for maximum and minimum. A stopcock located
in the rear part of the tank allows the suggested periodical drainage.
It is proposed for the removal and neutralization of corrosive vapours and
gases evolved during high temperature mineralizations (Kjeldahl, digestions
with nitric, sulfuric or perchloric acid). For this application it is suggested to
use with the pump, the SMS fume neutralizer.
As a vacuum source it can be connected to laboratory equipment as rotating
evaporators, Buchner, Gooch or membrane filters, gel dryers, etc.
The JP vacuum pump produces at the aspiration tubes a residual pressure of
35 mm Hg with a water temperature of 15 °C.
2. Assembly and installation
Upon receipt and after having removed the packaging, please check the integrity of the instrument. The box includes:
JP recirculating water pump
Power cable
Instruction manual
The equipment is to be connected to the right electric supply by the electric cable connected to the rear of the upper part by
a panel socket with fuse. Ensure that the electric mains is earthed and that the mains socket is easy to reach.
Fill the tank with tap water through the front door up to the maximum level shown by the external indicator. Turn on the
instrument by the lighted main switch.
Air flow and vacuum level are regulated by the proper knob.
Air flow
: from 15 to 35 l/minute
Vacuum
:
from room pressure (1 bar) to 0.04 bar
Place the instrument at about 15 cm from the walls
.
Attention
: If the unit is used for aspiration of corrosive gases, fumes or liquids or for neutralizing acid gases during Kjeldahl
mineralizations adopt the following precautions:
• Use the SMS
• Connect JP to SMS and SMS to the fume cap by using the supplied Viton tube. Viton is a copolymer of vinylidene
fluoride and hexafluoropropylene withstanding temperatures up to 200 °C and highly resistant to chemicals (oils,
solvents, oxidizing agents, strong alkalies and acids) with good mechanical properties (weathering).
3. Operating controls
3.1 Absorption
The widely applied Kjeldahl method for protein content evaluation uses a high temperature (up to 420 °C) mineralization
step with concentrated sulfuric acid and a catalyst.
During the mineralization corrosive toxic gases such as sulfur dioxide (SO
2
) and sulfur trioxide (SO
3
) are evolved.
JP is able to suck the gases and vapours evolved by up to 20 Kjeldahl digestion tubes. The pump can be connected to SMS
fume neutralizer which removes acid gases by three steps (condensing, neutralization and absorption) allowing a correct
disposal without emission of toxic substances to the environment (air or water drain).
3.2 Time related programs A or B
The efficiency of fume removal equipment SMS is related to the time of residence of fumes deriving from digestion in the
various stages. If the digestion test tubes with the samples and reagents are introduced in a heating block when this is hot
(normally 420 °C) a large amount of acid fumes is developed in the first minutes. In the following minutes the volume of
fumes is reduced.
Thus in the first phase of digestions it is necessary to dispose of a large capacity of gas removal that can be reduced latel y
for a better yield of the system for gas abatement.
This is the reason of the possibility of selection of an optimal sucking power on the JP related to the different phases of
digestion and to the number of digested samples. It is possible to select a work program of JP which changes automatically
the air flow during the digestion and in relation to the used heating block.
EN
Summary of Contents for F30620198
Page 15: ...15...