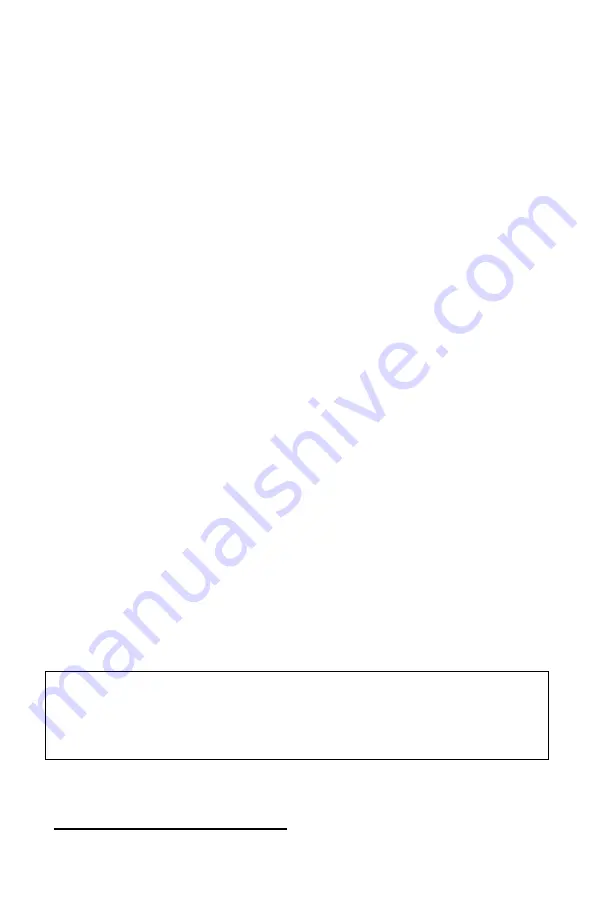
"quality control" inspection.
PC Board Inspection:
Before applying power to your kit, give it a thorough QC (quality control)
inspection. This will help you find inadvertent assembly errors that might
prevent the filter from working or cause damage to sensitive parts.
Follow this procedure:
Compare parts locations against the parts-placement diagram. Was
each part installed where it is supposed to be? Was the correct
value used? Start at one side of the board and work your way across
in an organized pattern.
Inspect the solder side of the board for cold-solder joints and solder
bridges between tracks or pads. Use a magnifying glass to obtain a
clear view of the track area. If you suspect a solder bridge, hold the
board in front of a bright light for a better view. All joints should be
smooth and shiny, indicating good solder wetting and flow. Resolder
any beaded or dull-appearing connections. Lead Free solder will not
be as shiny as the lead-tin solder.
If you find a construction error and need to remove a part or two, it will be
easier if you have the right tools. One very convenient item for freeing
soldered-in parts is a "solder sucker". This consists of a suction bulb or a
spring loaded vacuum pump that draws molten solder away from the pad
and lead. Alternatively, you may use a special copper braid called "solder
wick" (solder suckers and solder wick are both available at your local
Radio Shack or electronics supply house). If you suspect you've
damaged a component during removal, better to replace it than risk
reusing it!
Finally, rosin flux can absorb moisture, which may cause a problem for
some electronic equipment. To remove flux, use isopropyl alcohol (or
95% grain alcohol) and an old toothbrush. Apply a generous amount of
alcohol with the toothbrush and scrub gently. Once the flux has fully
dissolved, blot the bottom of the board dry with an untreated tissue. Give
it a final alcohol wash, and allow to dry thoroughly.
Caution: alcohol is highly flammable and must be used
with adequate ventilation! Use safety goggles,
and avoid prolonged skin contact. It's also best
to do this outdoors.
Now that assembly and inspection is completed, you're ready to begin the
testing and alignment phase of construction.
TESTING AND ALIGNMENT
The best way to test the VEC-821K is with a calibrated audio signal