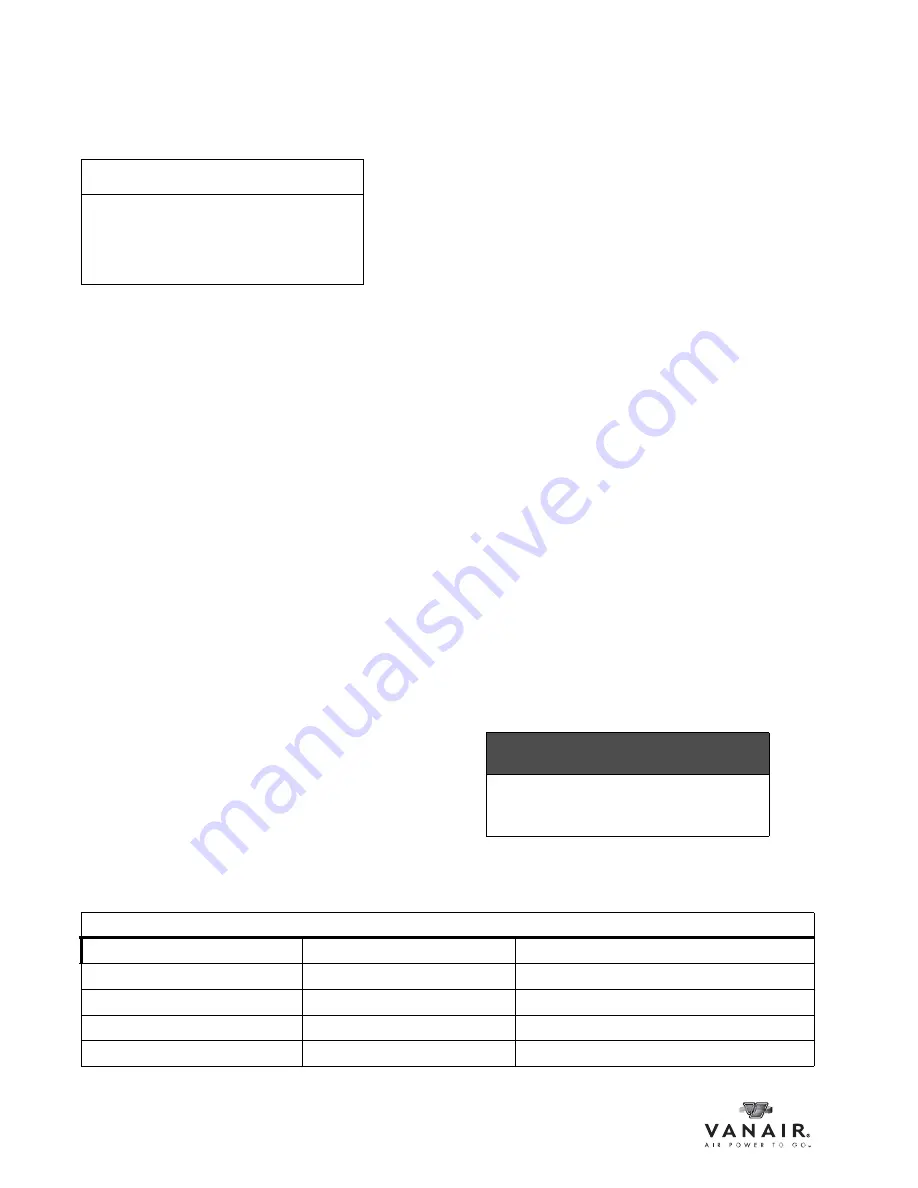
SECTION 5: OPERATION
AIR N ARC
®
300 SERIES ALL-IN-ONE POWER SYSTEM
®
PAGE - 50
090012-OP_r0
1. With the engine shut off, insert the twist lock
connections of the ground clamp and the
electrode holder cables into the welder
connection ports on the control panel. For
Direct Current Electrode Positive (DCEP)
connect the electrode holder to the positive
(+) port, and the ground clamp to the
negative (–) port. For Direct Current
Electrode Negative (DCEN) connect the
electrode holder to the negative (–) port, and
the ground clamp to the positive (+) port.
2. Select the appropriate electrode for the
material and process being performed.
See
Table 5B: ELECTRODE SPECIFICATIONS
for selecting an electrode.
3. Place the ground clamp on the work piece
and insert the appropriate welding rod into
the electrode clamp.
4. Start the engine (
See Section 5.2, Engine
Start-up and Shutdown Procedure
).
5. On the control panel, place the CC/CV switch
in CC mode. Place the DC Charger/Welder
switch in welder mode.
6. Adjust the power dial to the appropriate
amperage setting for the material and the
electrode being used. (See
Table 5B:
ELECTRODE SPECIFICATIONS
for
electrode amperage ratings). At anytime
during welding, the power dial may be
adjusted to the desired amperage level.
7. When you strike the electrode against the
material being welded, the engine will go to
NOTE
For electrode striking technique, consult
Section A.7, Electrode Ignition Procedure
in Appendix A.
TABLE 5B: ELECTRODE SPECIFICATIONS
METAL THICKNESS
ELECTRODE SIZE
WELDING AMPERES
1/16-1/8
3/32
50-90
1/8-1/4
1/8
90-140
¼-3/8
5/32
120-180
3/8-1/2
3/16
150-230
NOTE
If a longer welding lead is desired,
optional 25 and 50 ft. lead segments may
be purchased from Vanair
Manufacturing, Inc. for a maximum lead
length of 100 ft.