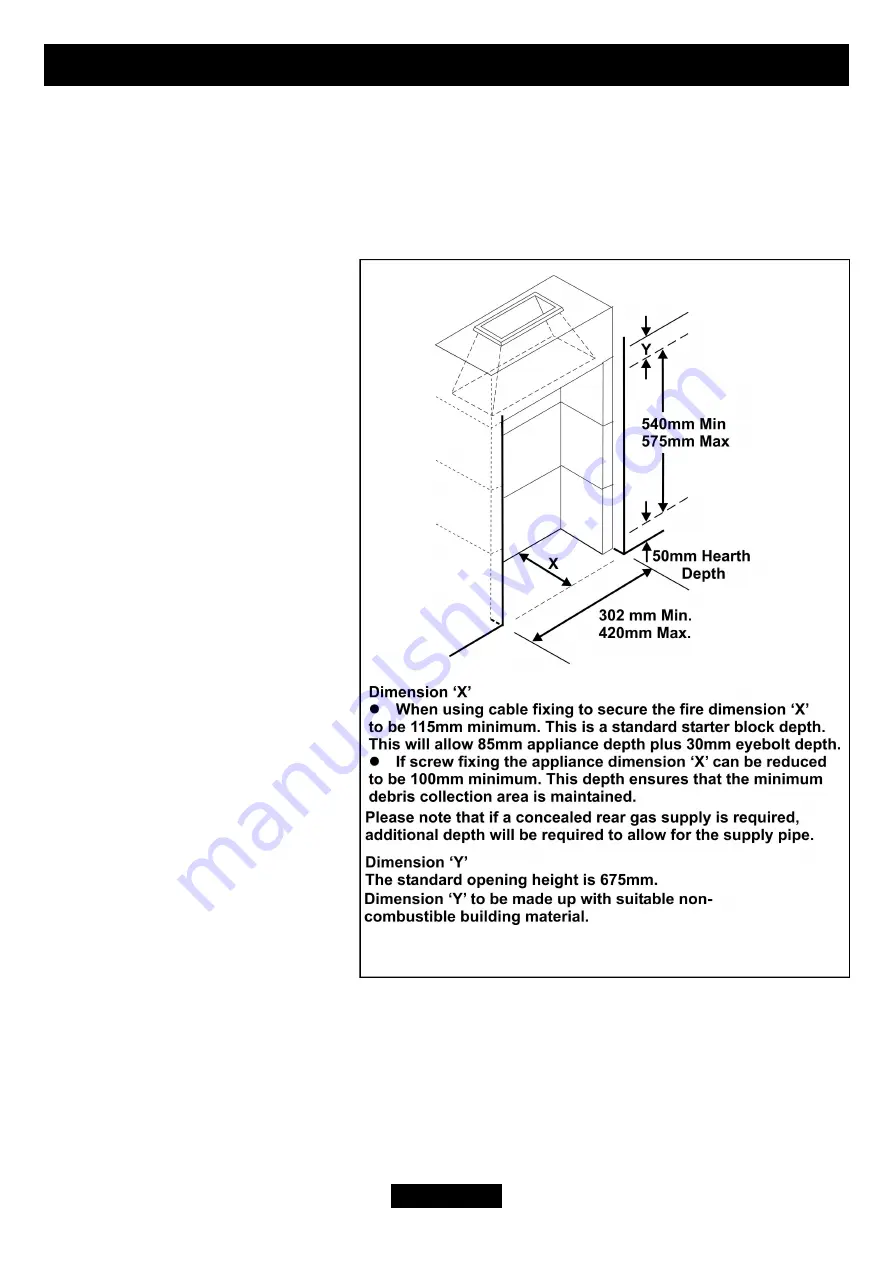
must be
not less than the dimension shown in figure 3.
The current versions of BS1289 and BS EN 1806 recommend that there should be an air
space or insulation between the flue blocks and the plaster because heat transfer may
cause cracking on directly plastered flues. However, generally this appliance is suitable
for installations under all circumstances unless there is a history of cracking problems.
Remember that faults such as cracking may be caused by poorly built and restrictive
flues, e.g. mortar extrusions, too
many bends, flue heights below
three metres, restrictive
terminations, etc.
3.2.4
If the fireplace opening is
greater than the acceptable
dimensions given in this guide, do
not use the back of a fire surround
or marble to reduce the opening.
This may cause cracking of the
surround back or marble.
3.3
The following flues are
suitable:
!
225mm x 225mm
conventional brick flue.
If a flue liner is used, it must be a
minimum of 125mm diameter.
The liner must be sealed to the
surrounding area above the
fireplace opening and to the top of
the chimney. An approved
terminal must be fitted.
!
200mm diameter factory made
insulated flue manufactured to BS
4543.
!
A properly constructed precast flue conforming to B.S 1289 or BS EN 1806.
!
A flue pipe with a minimum diameter of 175mm. See B.S 6461 Part 1 for suitable
materials. Metal flue pipes must comply with B.S 715.
!
Single wall, twin wall or flexible flue liner of minimum diameter 125mm. The
materials used are stainless steel or aluminium as specified in B.S. 715.
3.3.1
The minimum effective height of the flue must be 3m.
3.3.2
The flue must be clear of any obstruction and its base must be clear of debris.
Page 8
INSTALLER GUIDE
Figure 3. Pre-cast Fireplace