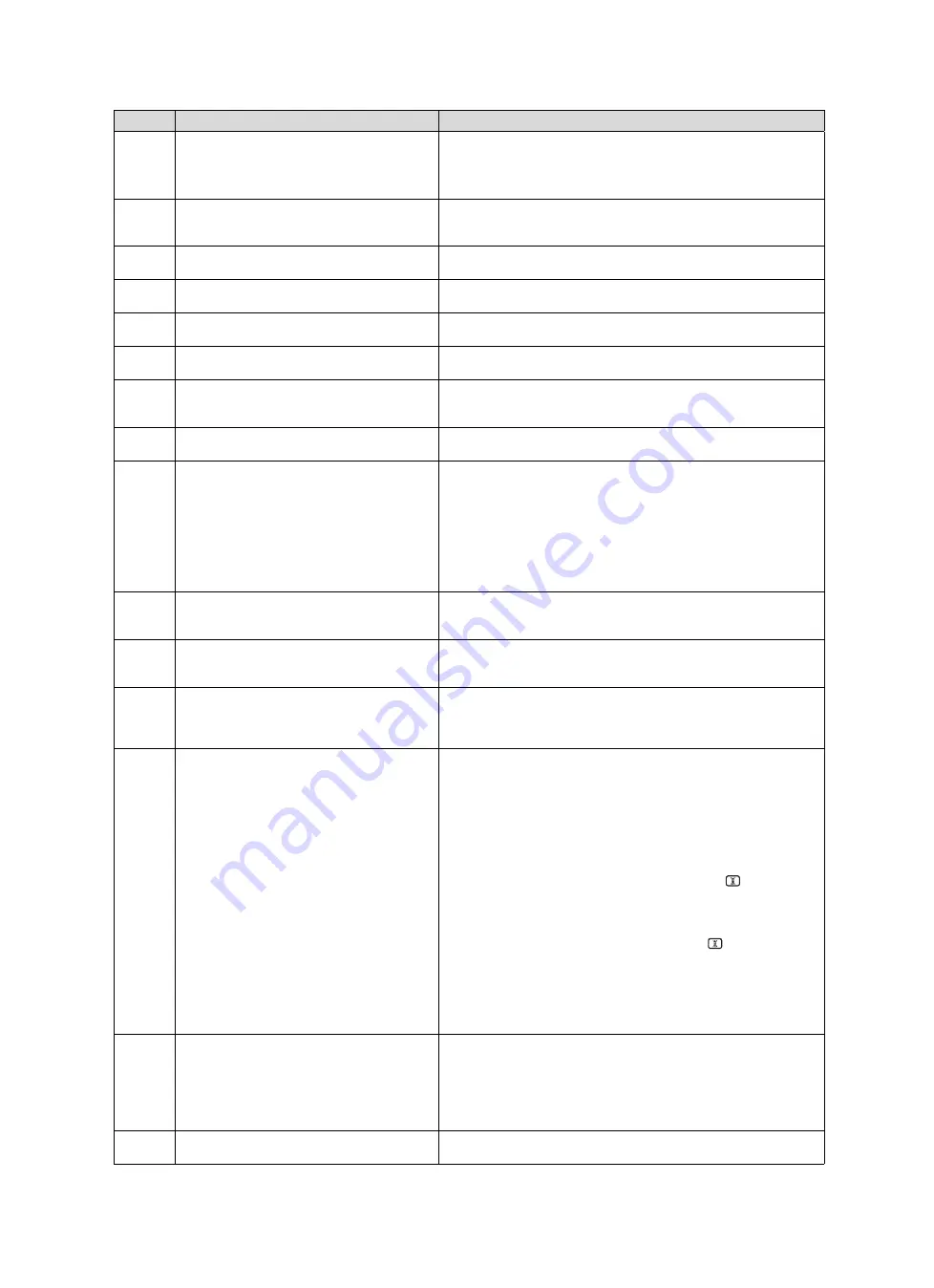
Appendix
42
Installation and maintenance instructions ecoTEC exclusive 0020186710_06
Code
Parameter
Possible causes
F.13
Short circuit: Cylinder sensor
Combination product: Warm start sensor/cylinder sensor short circuit
Combination product with actoSTOR: Short circuit cylinder sensor (NTC)
only in combination with F.91
NTC defective, short circuit in cable harness, cable/housing
F.20
Safety switch-off: Temperature limiter
Incorrect earth connection between cable harness and product, flow or
return NTC defective (loose connection), stray spark via ignition cable,
ignition plug or ignition electrode
F.22
Safety switch-off: Low water pressure
No or insufficient water in the product, water pressure sensor defective,
cable to pump or water pressure sensor loose/not connected/defective
F.23
Safety switch-off: Temp.spread too large
Pump blocked, insufficient pump output, air in product, flow and return
NTC connected the wrong way round
F.24
Safety switch-off: Temp. incr. too fast
Pump blocked, insufficient pump output, air in product, system pressure
too low, non-return valve blocked/incorrectly installed
F.25
Safety switch-off: Flue temp. too high
Break in plug connection for optional flue gas safety cut-out (SCO),
break in cable harness
F.26
Fault: Fuel valve not working
Gas valve assembly stepper motor not connected, multiple plug on the
PCB not plugged in correctly, interruption in cable harness, gas valve
assembly stepper motor defective, electronics defective
F.27
Safety switch-off: Flame simulation
Moisture on the electronics, electronics (flame monitor) defective, gas
solenoid valve leaking
F.28
Start-up failure: Ignit. unsuccessful
Gas meter defective or gas flow monitor has triggered, air in gas, gas
flow pressure too low, thermal isolator (TAE) has triggered, condensate
route blocked, incorrect gas injector, incorrect spare part gas valve as-
sembly, value in
D.052
does not correspond to the printed value on the
current gas valve assembly, fault on the gas valve assembly, multiple
plug on PCB incorrectly plugged in, break in cable harness, ignition sys-
tem (ignition transformer, ignition cable, ignition plug, ignition electrode)
defective, ionisation flow interrupted (cable, electrode), incorrect earthing
of product, electronics defective
F.29
Operating failure: Ignit. unsuccessful
Gas supply temporarily stopped, flue gas recirculation, condensate route
blocked, defective earthing of product, ignition transformer has spark
failure
F.32
Fault: Fan
Plug on fan not correctly plugged in, multiple plug on PCB not correctly
plugged in, break in cable harness, fan blocked, Hall sensor defective,
electronics defective
F.33
Pressure switch
Check: Cable harness, vacuum hose (blockage), supply air/flue gas
route (blockage), panel (correct type), flue pipe (length), air pressure
sensor, settings (if necessary, switch
D.132
to multiple-flue configura-
tion), pressure switch, fan.
F.35
Fault: Air/flue gas duct
Check the entire air/flue pipe for:
–
Permitted design
–
Restriction or blockage in the air/flue pipe caused by obstructions
–
Damage
The air/flue pipe must be installed in accordance with the recognised
rules
If the supply of combustion air (air pipe) or discharge of flue gas (flue
pipe) occurs with no problems, reset the product using
and start it up
If
F.35
occurs again after start-up and the air/flue pipe is present and
correct, the function for checking the air/flue pipe can be deactivated via
D.145
If the function is deactivated via
D.145
, the product
can be reset and
it can be started up
Note
D.145
can be used to permanently activate or deactivate the function
After the function is deactivated, the product no longer automatically
checks whether there are restrictions for the air/flue pipe.
F.42
Fault: Coding resistor
Gas family coding resistor short circuit/interruption (on the PCB)
–
Gas family coding resistor missing
–
The coding resistor does not match the gas type selection under
D.087
Incorrect coding resistor or incorrect gas type selected
F.49
Fault: eBUS
Short circuit on eBUS, eBUS overload or two power supplies with differ-
ent polarities on the eBUS