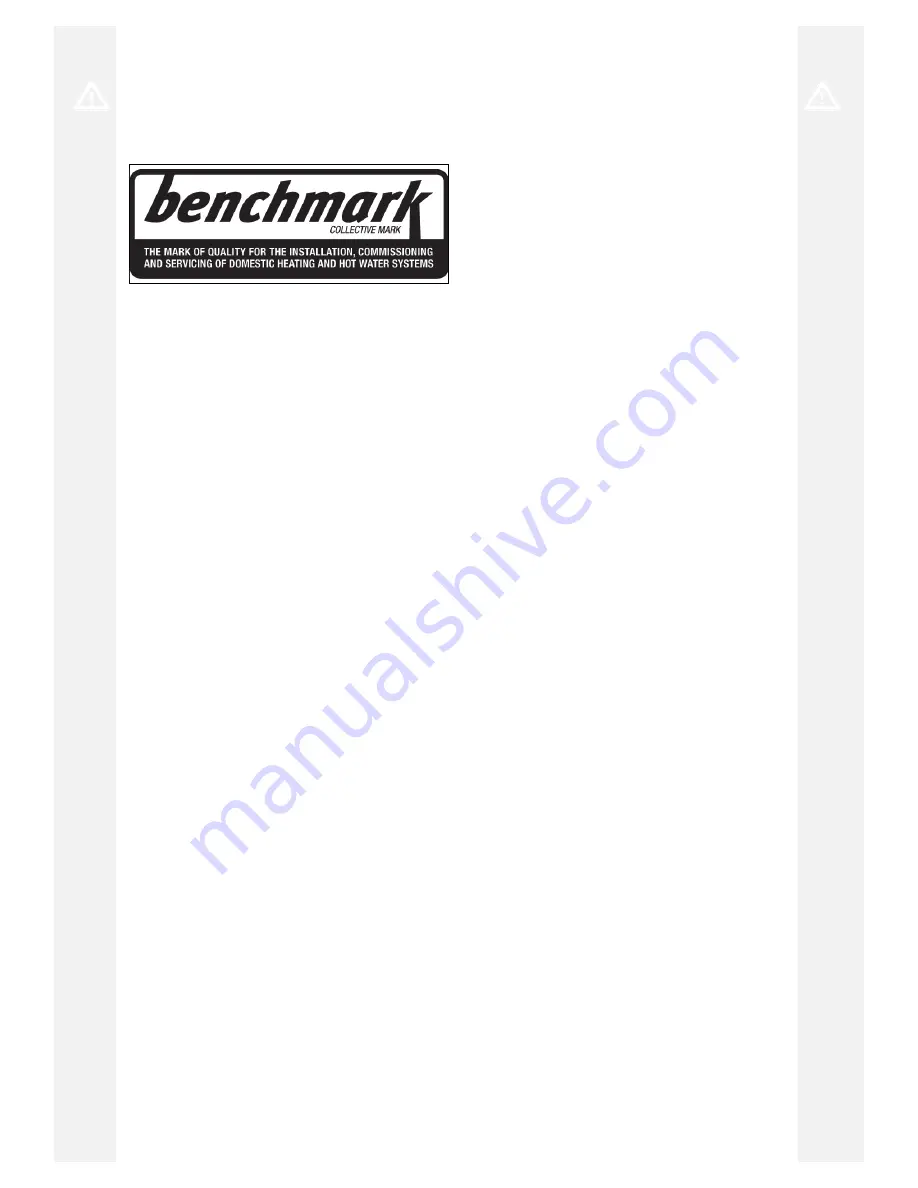
Safety 1
0020147164_07 aroTHERM Installation instructions
5
which is available from the Heating and Hot-
water Industry Council who manage and pro-
mote the Scheme.
Visit www.centralheating.co.uk for more in-
formation.
Planning consent and Building works notific-
ation should be submitted either to Building
Control or to a Competent Person Provider.
1.8
Regulations
1.8.1 Statutory requirements
Where no British Standards exists, materials
and equipment should be fi t for their purpose
and of suitable quality and workmanship.
The installation of this appliance must be car-
ried out by a competent person in accord-
ance the rules in force in the countries of des-
tination.
Manufacturer’s instructions must not be taken
as overriding statutory requirements.
1.8.2 Standards
On installing and commissioning the appli-
ance you must adhere to the technical rules,
standards and provisions in eff ect at the
time.
1.8.3 Reminder of existing regulatory acts
–
EC regulation No. 20372000 from the 29th
of June 2000 This European regulation re-
peals regulation No. 3093/94 and presents
the elimination schedules of CFC and
HCFC. It also deals with the collection of
refrigerants, system leaks, particularly sys-
tems containing more than 3 kg of CFC
or HCFC, as well as the minimum level of
qualifi cation required by the technicians.
–
EC regulation No. 0842/2006 from the 17th
of May 2006 regarding the containment,
use, collection and disposal of the fl uorin-
ated greenhouse gases, the labelling and
elimination of the products and equipment
containing these gases, the restriction of
use and banning of certain products from
the market, as well as the training and cer-
tifi cation of personnel and companies op-
erating in the activities targeted by this reg-
ulation: refrigeration, air-conditioning, heat
pumps and fi re protection systems con-
taining greenhouse gases.
1.9
Other regulations
1.9.1 Control of Substances Hazardous to
Health
Under Section 6 of The Health and Safety at
Work Act 1974, we are required to provide in-
formation on substances hazardous to health.
The adhesives and sealants used in this ap-
pliance are cured and give no known hazard
in this state.
The refrigerant used in this appliance is
R410a the use of which is strictly controlled
by F Gas regulation EN842/2006.
1.10 Intended use
There is a risk of injury or death to the user or
others, or of damage to the product and other
property in the event of improper use or use
for which it is not intended.
The heat pump is an air/water monoblock
system and uses the energy from the outside
air to supply heat to the building.
The heat pumps are intended exclusively for
domestic use as heat generators for closed
heating and hot water central heating sys-
tems and for hot water generation.
Intended use includes the following:
–
observance of accompanying operating,
installation and servicing instructions for
the product and any other system compon-
ents
–
installing and fitting the product in accord-
ance with the product and system approval
–
compliance with all inspection and main-
tenance conditions listed in the instruc-
tions.
Any other use that is not specified in these
instructions, or use beyond that specified in
this document, shall be considered improper
use. Any direct commercial or industrial use
is also deemed to be improper.
Caution.