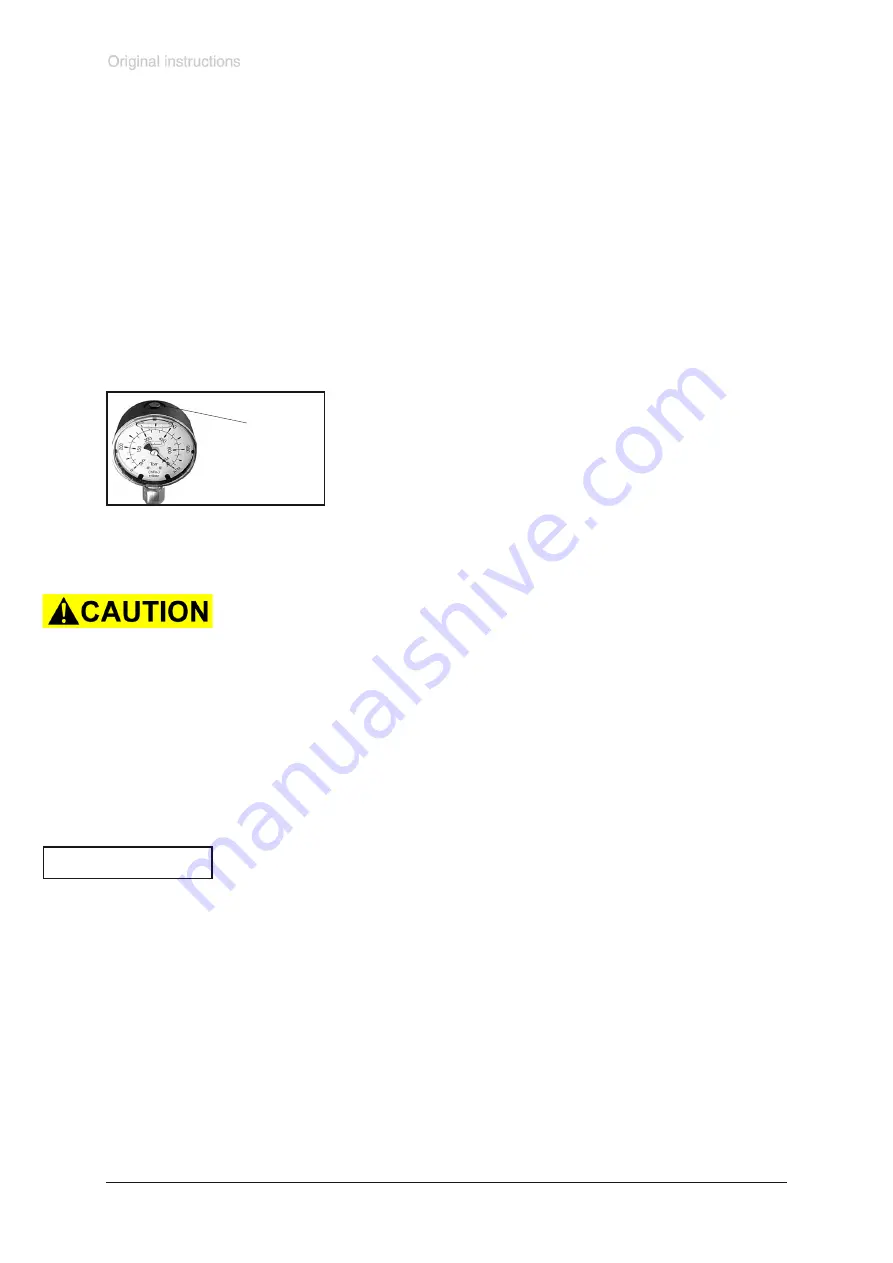
Documents are only to be used and distributed completely and unchanged. It is strictly the users’ responsibility to check carefully
the validity of this document with respect to his product. Manual-no.: 999155 / 29/01/2009
page 18 of 36
During operation
•
Maximum ambient temperature
: 40 °C
• Make sure ventilation is adequate especially if the pump is installed in a housing
or if the ambient temperature is elevated.
•
Potentially dangerous gases or vapours
at the outlet of the pump have to be
drained and disposed appropriately.
• Due to the high compression ratio of the pumps, the pressure at the outlet port
might get higher than the maximally permitted pressure compatible with the
me-
chanical stability
of the system. Ensure that the pump outlet is not blocked or
restricted.
ME 4R NT:
•
Attention
: Do not unscrew the dispensing screw completely! There are no stops
at the end of the threads!
If the pump is installed in altitudes of more than 1000 m above mean sea level check
compatibility with applicable safety requirements, especially IEC 60034 (motor might
overheat due to insufficient cooling).
Do not start the pump if the
pressure difference between inlet and outlet ports
exceeds
max. 1.1 bar
. Attempts to start the pump at higher difference may cause
blockade and damage of the motor.
Check compatibility with
maximally permitted pressure
at outlet and
maximum
pressure difference
between inlet and outlet ports.
ME 4R NT:
For continuous operation at inlet pressures above atmospheric pressure the inlet
pressure must not exceed the outlet pressure. The maximally permitted pressure
at the outlet is 4 bar absolute.
Operating the pump at high inlet pressure or pumping dusty gases for a long time
may cause clogging of the silencer. Check the silencer regularly and replace or install
a hose nozzle (order no. 639758) with clamping ring (order no. 639729) instead.
Use of a suitable valve to isolate the pump from the vacuum system is recommended
to allow the pump to warm up before pumping condensable vapours or to clean the
pump before it is switched off.
When assembling, ensure
vacuum-tightness
. After assembly, check the whole sys-
tem for leaks.
Secure hose connections at the pump appropriately against unintentional detach-
ing.
Notes prior to the use of the manometers (only ME 4R NT):
The manometers used are manometers with glycerin filling. The overpressure ma-
nometer indicates the overpressure relative to the atmospheric pressure at the place
of installation. The vacuum meter indicates the absolute pressure.
Install the pump in the room of operation.
Prior to use the reference chambers have to be ventilated.
Else, not ventilating the manometer may lead to a systematic measuring error.
Ventilate the manometer using the pressure compensation
valve. Close the valve after ventilation.
☞
Repeat if necessary until dial shows zero with measuring
connection ventilated to atmosphere.
pressure
compensation
valve
NOTICE