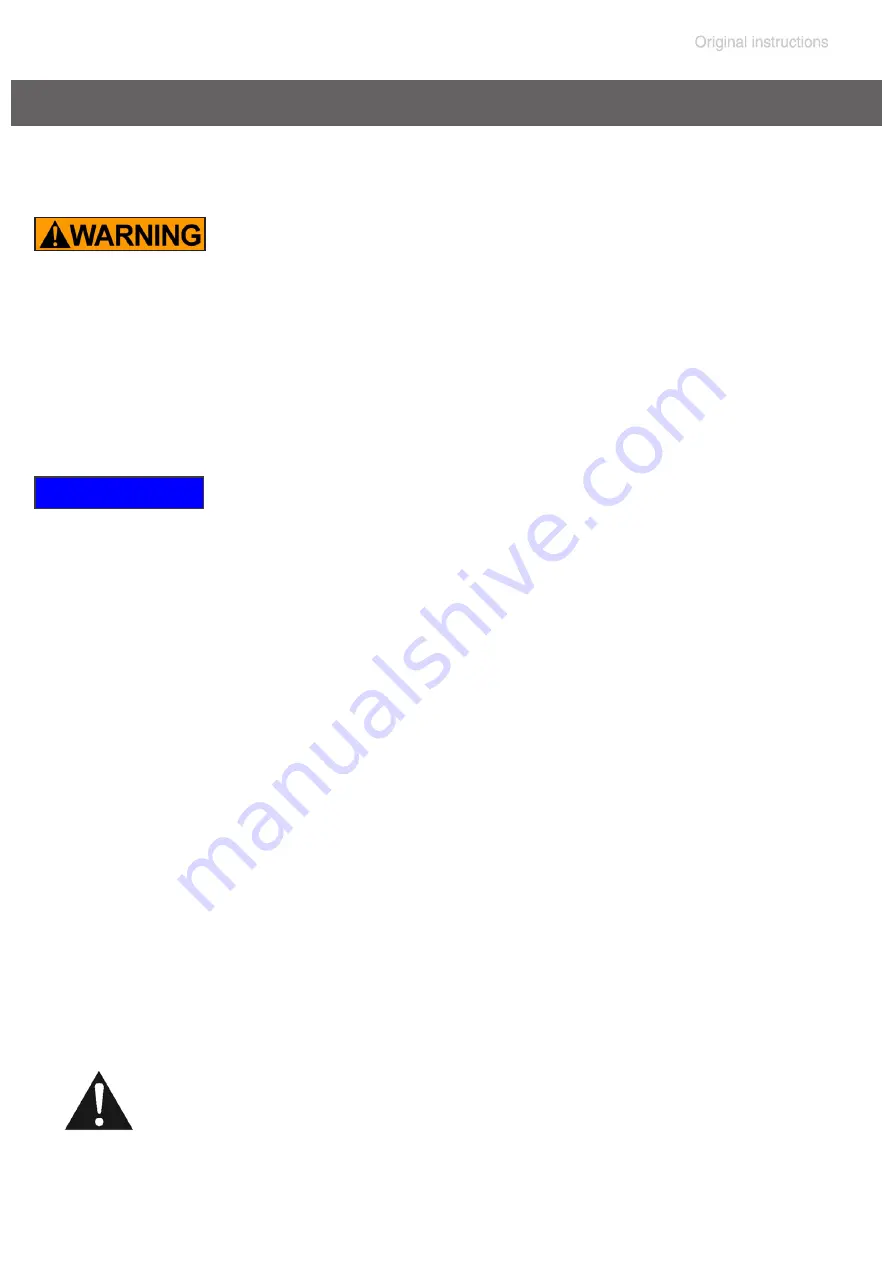
page 9 of 57
Safety information!
Important information!
+
Keep this manual complete and accessible to per-
sonnel at all times!
+
Read this manual carefully before installing or op-
erating the equipment. Observe the instructions
contained in this manual.
+
Do not modify the equipment without authoriza-
tion.
This manual is an integral part of the equipment de-
scribed therein. It describes the safe and proper use
of the vacuum pump.
Make operating personnel aware of dangers arising
from the pump and the pumped substances.
VACUUBRAND disclaims any liability for inappropri-
ate use of these pumps and for damage from failure
to follow instructions contained in this manual.
This manual is only to be used and distributed in its com-
plete and original form. It is strictly the users’ responsibility
to check carefully the validity of this manual with respect
to his product.
Manual-no.: 999241 / 01/12/2012
The following signal word panels and safety
symbols are used throughout this manual:
This is the safety alert symbol. It is used to alert you to po-
tential personal injury hazards. Obey all safety messages
that follow this symbol to avoid possible injury and death.
NOTICE