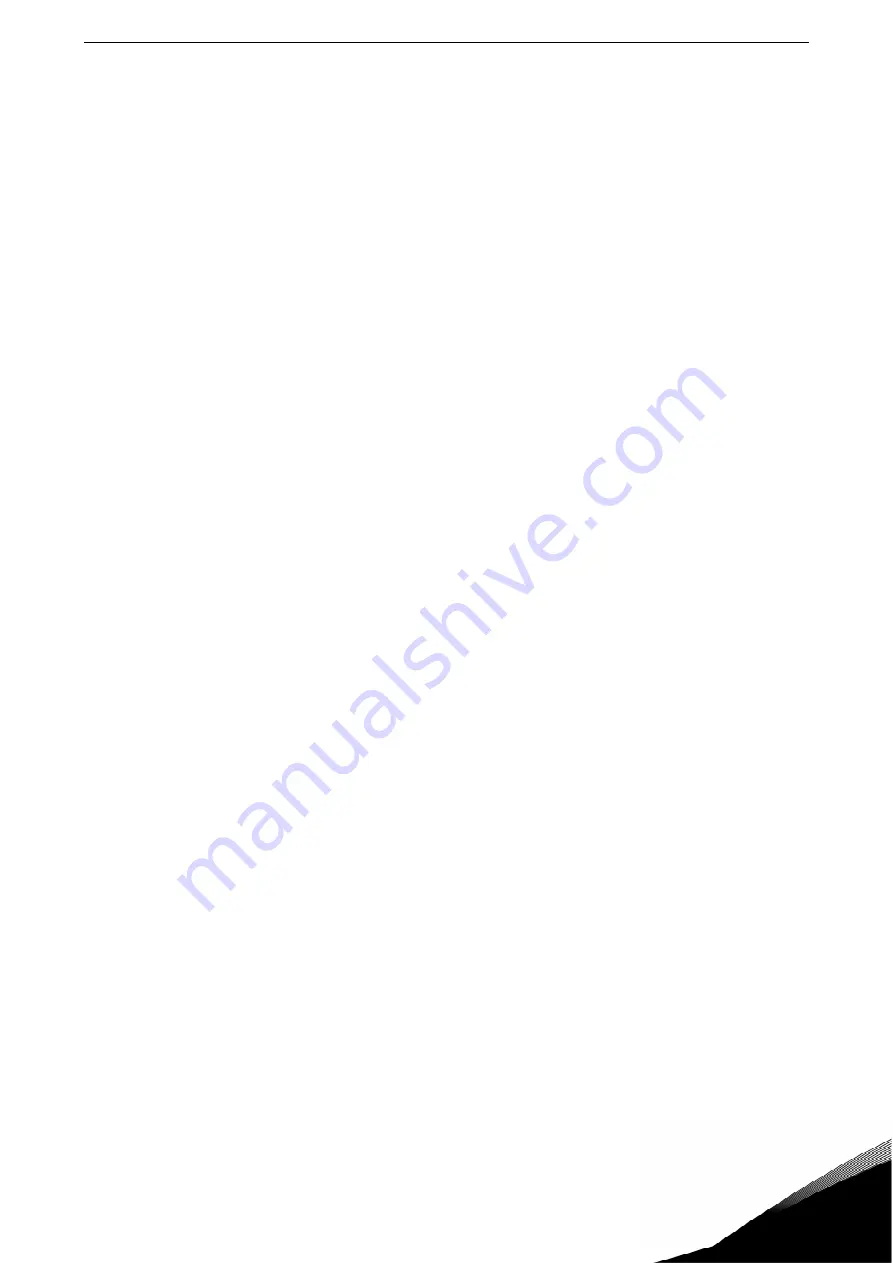
Fault codes and software
email: [email protected] Tel: +358 (0)201 212 575 Fax: +358 (0)204 335 091
29
4
•
Underload protection (ID713) curve knee point (fieldweakening point) was 50 Hz.
Corrected to be same as motor nominal frequency.
•
Local/Remote application: Start stop logic (P2.2.1 / ID300) mode changed inter-
nally to 4 even the mode 8 was selected. Corrected.
•
PID-application: When unit was stopped by stop command (not switched off), the
PI output was freezed to value on stopping moment and started next time from that
point. Changed to start from min. freq. as it do after power up.
•
PID-application: Easychangeover from PID to keypad or motpotreference did not
work. Corrected.
•
Multipurpose appplication (ASFIFF06V310): If reference sleep function was used,
the function was not following the mode 14 of parameter P2.1.11 (ID117). Cor-
rected.
•
Multipurpose application (ASFIFF06V310): Parameter set selection P2.2.7.21
(ID496) only loads the sets. In previous version it also saved the sets. Note! The
parameter values are stored only when selecting P6.3.1 Parameter sets Store Set 1
or Store Set 2 in System menu or from NCDrive: Drive > Parameter Sets.
•
PFC-application: PI output is not freezed anymore when limit controllers (current
limit etc.) are active or unit is stopped.
•
PFC-application: Motor identification run added.
•
PFC-application: There was possible to happen overflow when analogue input was
scaled to narrow area. Corrected.
10. 3. 2. 7. NXS00001V166
Replaced version: NXS00001V165.VCN
System software version: 11.69.8170
Changes in system software:
•
Revision 165 did not support ready-state when evacuation mode (special applica-
tions) and low dc-bus voltage.
•
Frequency limit conditions of the stall protection function was not active in revision
165 but protection was active through whole frequency area.
•
When downloading parameters from panel and the parameter value is not within
the allowed max. / min. range of unit, the parameter is set to default value.
Changes in applications:
•
All applications: If one reset input was active, the unit did not accept reset from
other source. (For instance when I/O terminal RESET was high, reset via Profibus
was not possible).
•
Local/Remote control: When mode 0 was selected to Place A Start/Stop logic
(P2.2.1), the Reverse input did not work. Corrected.
•
Local/Remote control: Reading of analogue inputs did not work when corresponding
input filtering time was not set down to 10 ms. Corrected.