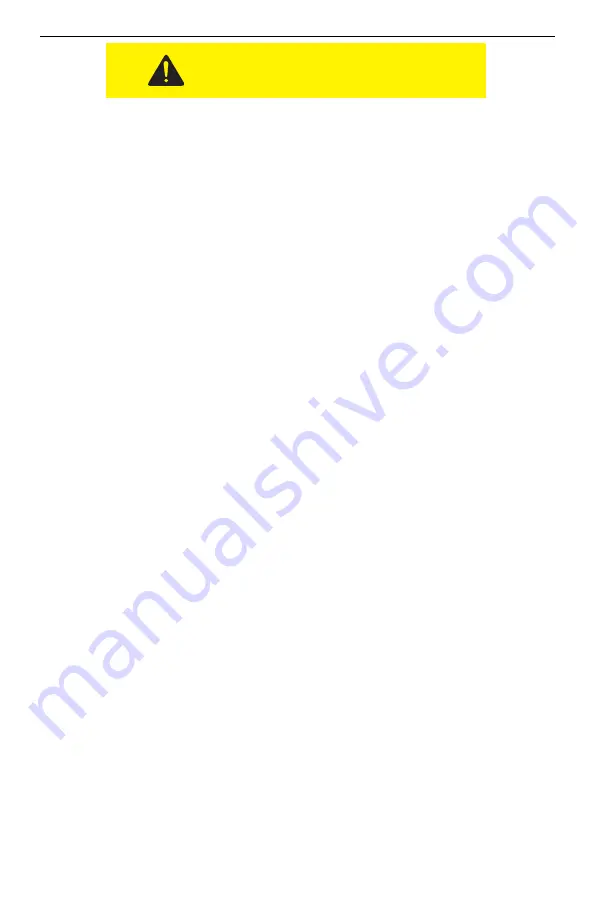
Procedures
MC450 Coring Unit. Operator’s Manual
© 2020 Utilicor Technologies Inc.
25
ATTENTION
Tips for a Successful Coring Operation
1. Mark the area to be cored with a paint slash across the core area before beginning to core. This
will help to properly orient the core when it comes time for reinstatement.
2. Before the coring process begins, manipulate the tilt controls on the skid-steer to make sure the
MC450 is level and flush to the ground.
3. Ensure that the appropriate rate of water is flowing through the pilot bit and the adapter plate
inside the drum. Periodically check for water flow during the coring operation. If the hole in the
pilot bit becomes blocked with asphalt or other debris, remove build-up by inserting a thick gauge
wire into center hole to clean it out. Do not core without adequate water flow to the centre pilot
bit.
4. Let the diamond tipped cutting drum do the work of cutting without excess pressure being
applied. Slow, continuous turning of the orbital control wheel will allow the coring teeth to work
and cut through the pavement without experiencing drum kick back, or stalling of the hydraulic
motor. You are applying too much downward pressure if the drum stops turning, or if the MC450
lifts off the ground.
5. Remember to raise the coring drum completely out of the cut area periodically during the coring
operation. This will help to remove any build up of suspended solids and cutting debris that can
cause the core to become lodged in the drum. Keep the cut space surrounding the core or “kerf”
clean and free of debris.
6. You will know you are through the concrete / asphalt pavement when the slurry changes color,
and begins to include roadbed materials such as sand, gravel, etc. The sound emitted by the PDC
pilot bit (typically a “grinding sound”) will change, and not be as noticeable when it cuts through
the bottom of the pavement. Core for another 1"- 2" more to compensate for the additional length
of the pilot bit and for any slant or unevenness in the core bottom.
7. To ensure that the core is completely cut through, raise the drum and, with a pry-bar in the pilot
hole, gently rock the core back and forth.
8. If the core should become stuck in the drum, use the holes in the top of the coring drum to insert a
push rod or spud-bar to tap the top of stuck core, remembering to rotate the drum a quarter turn
after each tap. Or tap the outside of the drum with a rubber mallet .
9. Check the coring teeth on the drum regularly for wear. You will save time by cutting with sharp
teeth, and reduce the chance of the core becoming stuck inside the drum, which tends to happen
once the life of the teeth has been used up.