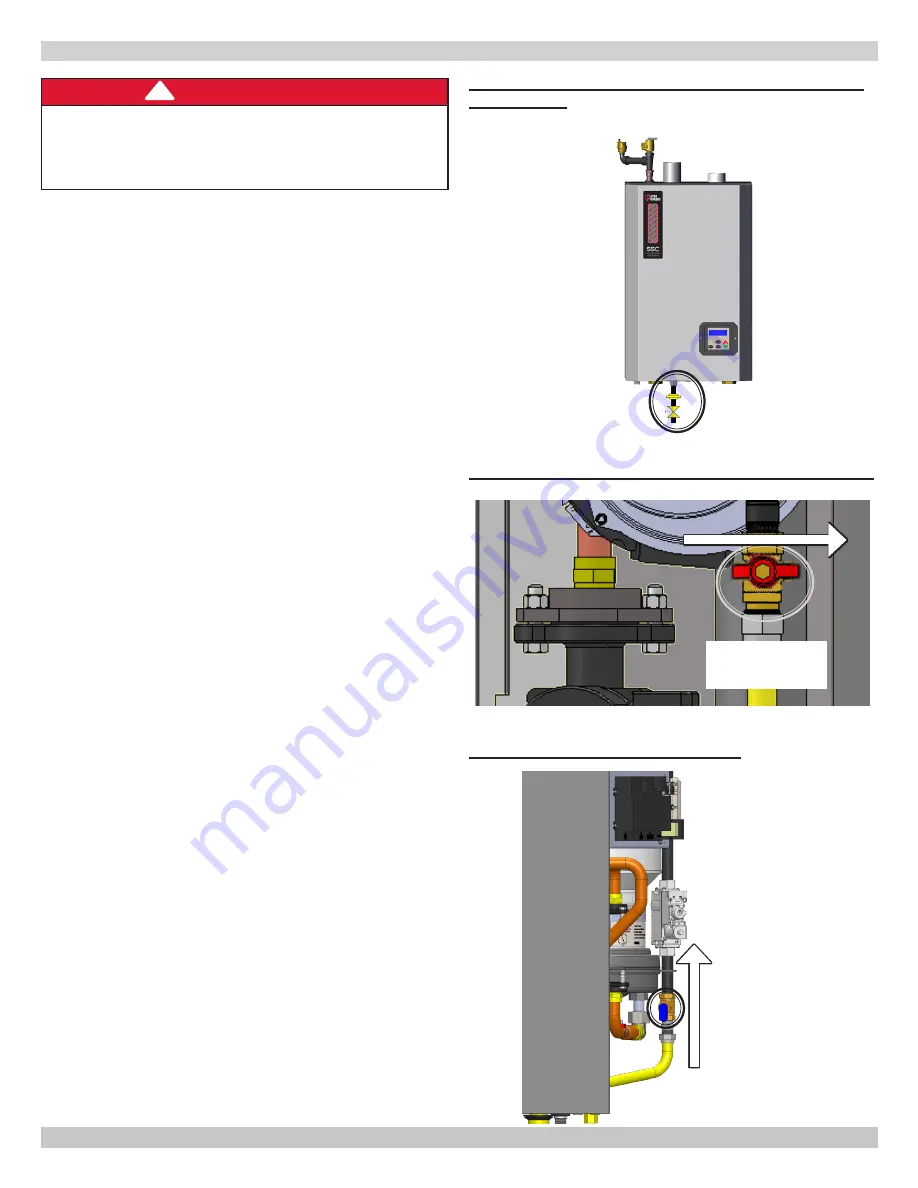
35
FIGURE 7-2 Manual Main Gas Shutoff Valve Outside
Boiler Jacket
7.3
Leak Check Gas Piping
Pressure test boiler and gas connection before placing
boiler in operation.
• Pressure test over 1/2 psig (3.5 kPa). Disconnect
boiler and its individual gas shutoff valve from gas
supply system.
• Pressure test at 1/2 psig (3.5 kPa) or less. Isolate
boiler from gas supply system by closing manual
gas shutoff valve. See figure 7-2.
• Locate leakage using gas detector, noncorrosive
detection fluid, or other leak detection method
acceptable to authority having jurisdiction. Do
not use matches, candles, open flames, or other
methods that can provide ignition source.
• Correct leaks immediately and retest.
Manual Main Gas
Shutoff Valve
FIGURE 7-3 Gas Shutoff Valve - 050/075/100/150/200
DANGER
Fire Hazard. Do not use matches, candles, open
flames, or other methods providing ignition source.
Failure to comply will result in death or serious
injury.
!
Gas shutoff valve
(shown in closed
position)
FIGURE 7-4 Gas Shutoff Valve - 299
Gas shutoff valve
(shown in open
position)
7 - GAS SUPPLY PIPING
PN 240011320 Rev. G 10/01/2021]