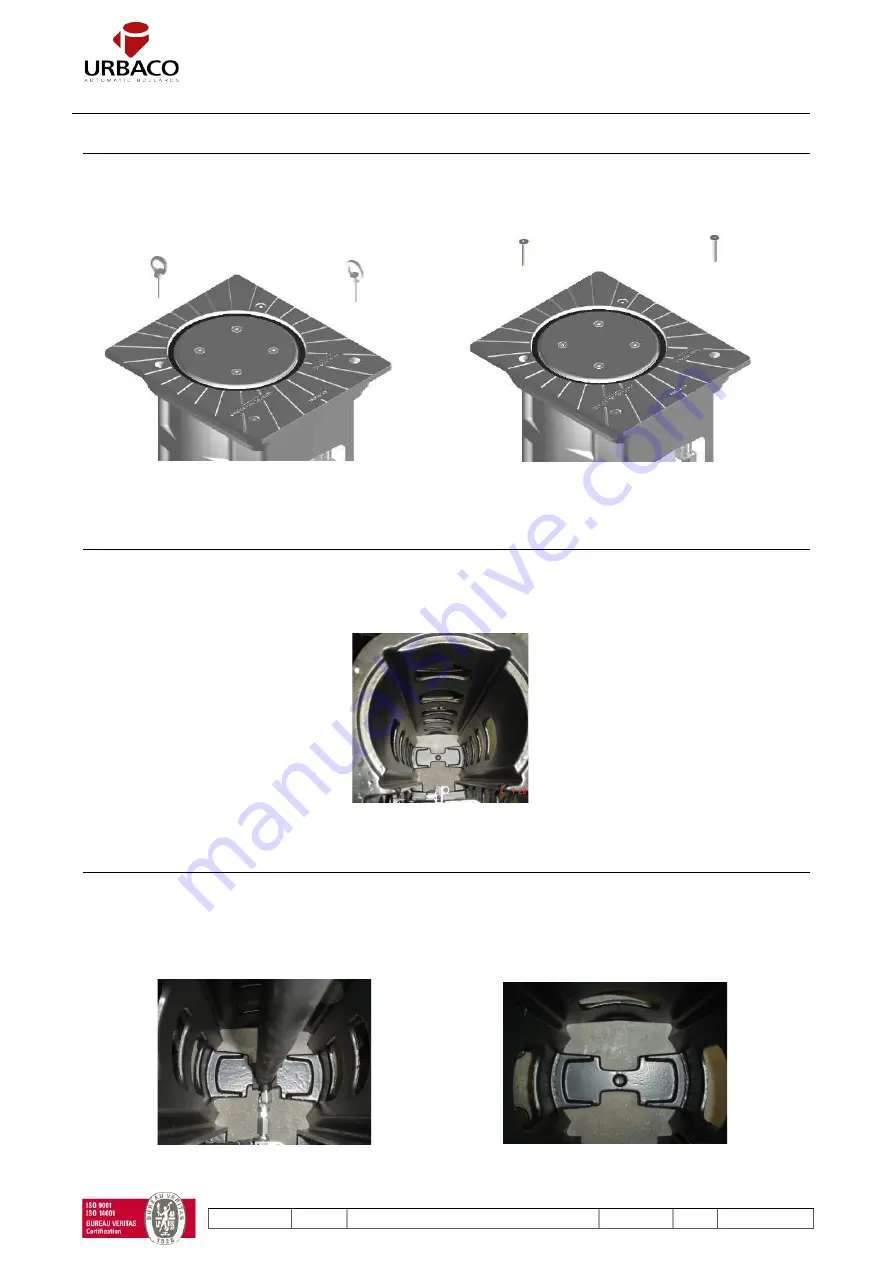
11/2015
NT BEA-G6EVO
V3.0
EN
p. 32/58
5.2. COMMON CHECK POINTS DETAILS
5.2.1. Cover well fastened – Check Point N°1
Remove the hoisting rings, clean the casing threading holes (using compressed air) and apply grease (Molykote
CU7439 Molykote or equivalent) before placing back the screws. Firmly tighten all screws.
5.2.2. Guides are cleaned – Check Point N°2
Make sure the casing's guides and the bollard head guides are cleaned and freed from deposits. Before reassembling
the bollard, spray the guides with Molykote 3402C or equivalent lubrication.
5.2.3. Cylinder well positioned – Check point N°3
NOTE: to perform this action, remove the cover and action the bollard in the raised position (without dismantling the
bollard head).
Check that the cylinder is properly centred in the cross-bar on the bottom of the casing.
Figure 36: Guide rails view
Figure 38: Casing crossbar
Figure 37: Cylinder position
Figure 35: Put the two screws back in place
Figure 34: Remove the two hoisting ring