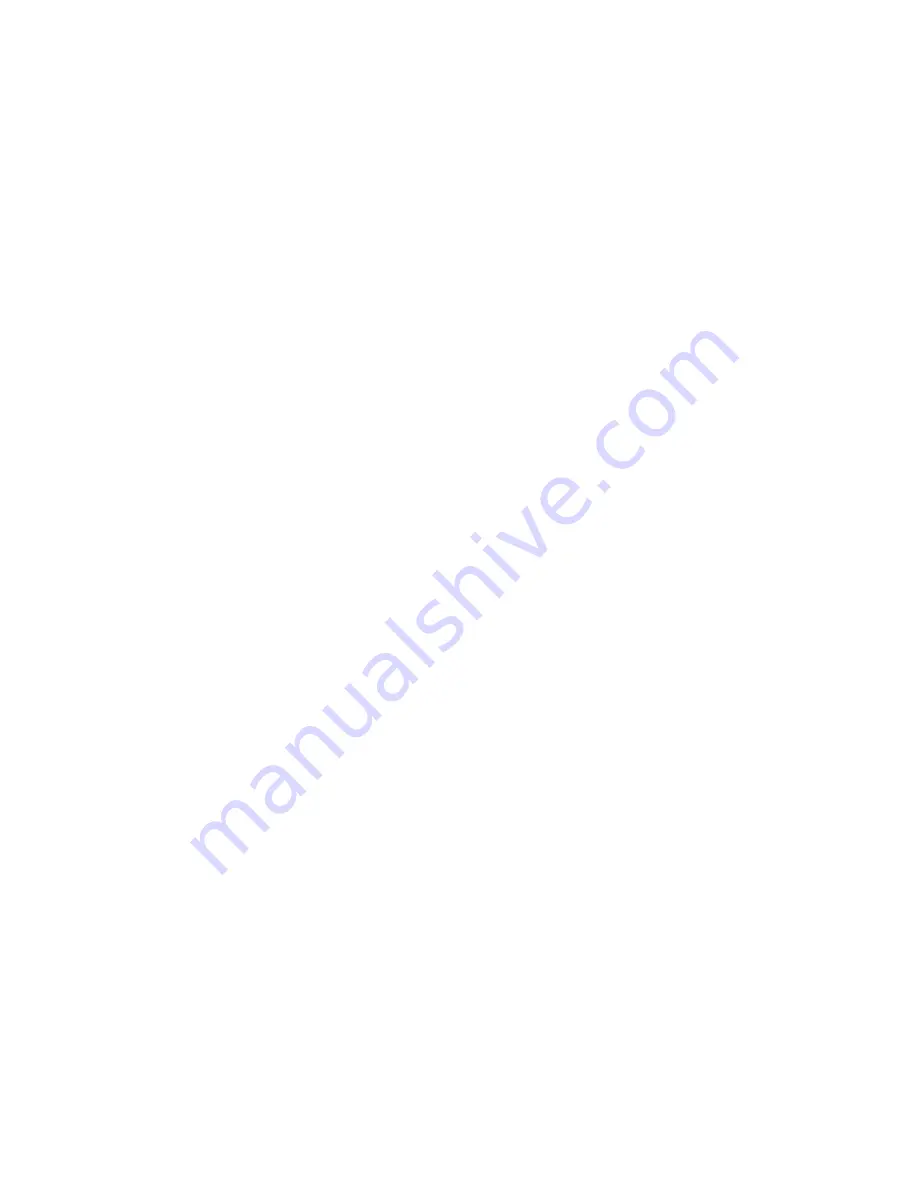
machine with a centering chuck to fit the valve stem for the purpose. In grinding take off
only as much material as needed to remedy the defect. The cylindrical bead on the
edge of the valve head should be no thinner than 1 mm.
Measure the side play between the valve stem and the guide with the help of an
indicator, the feeler pin of which should rest against the valve stem end with the valve
moved 3/16 inch / 4 mm off the seat (Fig. 4.3-3).
Guide wear should not exceed .010 inch / 0.25 mm. If there is excessive clearance,
measure the valve stem and determine whether the wear is in the valve stem, the guide,
or both. For this purpose measure the diameter of the valve stem and the guide bushing
at a distance of 1/4 inch / 5 mm inside the upper and lower edges of working surfaces. If
the wear of the valve stem exceeds .005 inch / 0.12 mm, replace the valve; if the wear of
the guide bushing exceeds .006 inch / 0.15 mm replace the guide.
Valve Guide Replacement
1. Decarbonize the guide (especially its neck).
2. Fasten the cylinder head in the vice, insert mandrel 345-047-3 and press out the
valve guide bushing. The head may be heated to facilitate guide removal.
3. Check the condition of the hole into which the valve guide is to be fitted. When you
are ready to install the new guide, heat the head to 390
°
F/200
°
C. Place the cold
valve guide on the mandrel 345-047-3, and quickly press the guide in place. Deck
height of the valve guide should be 20 mm measured from spring washer land on
head, to top of guide (without spring washer in place). Guide should be enough of a
press fit in the head casting that the guide does not fall out even when the head is
hot.
WARNING: Take precautions to avoid burns while handling the heated cylinder
head.
After the head has been allowed to cool, check that the guide is firmly retained in the
casting, then ream the guide to 8.00- 8.03 mm diameter, using reamer 055-150-3.
Check the hole for straightness with the help of 7.98 mm gauge 403-747.
After installing a new valve guide, check the valve seat chamfer concentricity, and, if not
concentric, grind or machine the valve seat chamfer. Check valve-to-seat alignment by
coating the valve seat chamfer with a thin layer of Pal ("Prussian blue") and fit the valve,
turning it while pressing the valve head against the seat. Valve fit is considered normal,
when the paint fillet formed on the valve head is positioned in the center of the chamfer
and its width is within .060 to .070 inch / 1.5 to 1.8 mm.
If necessary, correct the seat chamfer, using a grinding stone or cutters of 30 and 45
degrees. (cutters 032-106-6 032-132 with mandrel 345-558) valve contact area is at 45
degrees, inside chamfer is at 60 degrees (Fig. 4.3-4).
Summary of Contents for 2000 -10 series
Page 1: ...Year 2000 Repair Manual ...
Page 14: ...Table 1 2 1 cont d Lubrication diagram ...
Page 177: ......
Page 178: ......
Page 179: ......
Page 180: ......
Page 181: ......
Page 182: ......
Page 183: ......
Page 184: ......