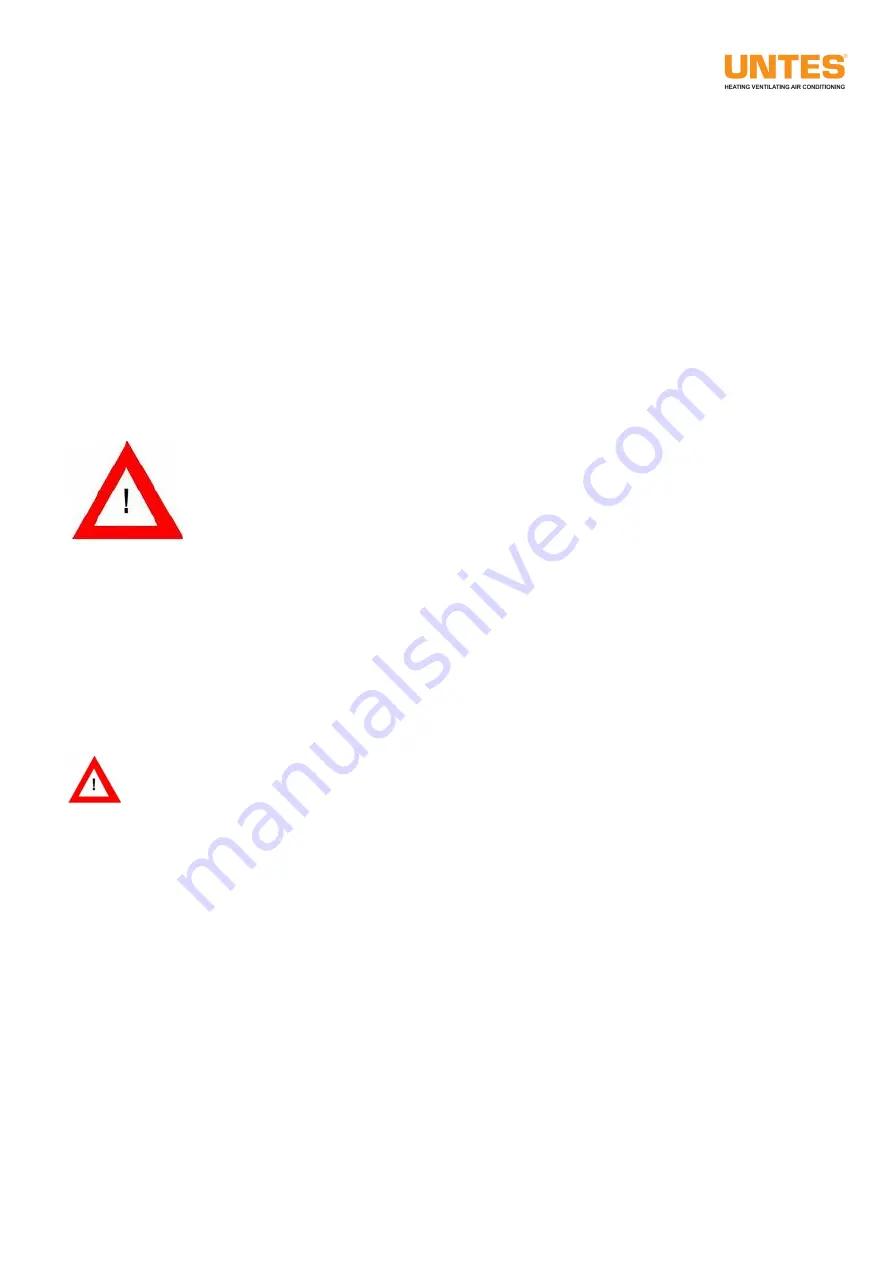
51
10.1.6. Control of Electric Equipment
Before starting to work on commissioning, power circuits of the device should be checked and compliance
of voltage levels should be confirmed. Later on, it should be ensured that all studs on the terminal are fixed.
The same control should be performed on other equipments working linked to the terminal.
Tag value of the voltage should be checked to stay within ± %5 tolerances by the help of a voltmeter. And
another important factor is to check rotation direction of fans. Fans must be checked to rotate in the right
direction by providing power to them. Otherwise, fans must be made to turn in the right direction by
changing between two phases in fan electricity connection. This control should be conducted in all
electricity connections. Whether phase sequence is correct should be checked by phase protection relay.
Before activating compressors, current values consumed by fans should be checked on values given at
electric schemas. If current draw values exceed limit values, mechanic operation conditions of fans should
be checked and probable problems should be eliminated. Later on, when compressors are commissioned, it
should also be checked whether current values consumed by compressors are above limit values.
The units have phase sequence and phase protection relay in scroll compressor. In case
phase sequence is correctly connected and all phases are in order in the unit supply
connection, led light on the phase protection relay on the panel will be green. Otherwise,
the led light isn’t on and doesn’t let the system operate. In this case, phase connections
should be checked and unless any correction, phase sequence should be changed. Phase
protection relay should never be deactivated. Otherwise, compressor is irreversibly damaged. This case is
assessed as an operational error and is non-warrantable.
10.1.7. Operation Control of Cooling Circuit
Approximately twenty four hours before commissioning, switch on the device’s supply line should be turned
into off position (there is electric connection).
Therefore,
lubricant crankcase heater is given electricity and
the lubricant inside lets the refrigerant in a mixed state evaporate. And this prevents compressors from
getting damaged at the first operation.
This procedure should also be repeated after the device electricity is
cut off for a long time. Electric on the device isn’t cut off under normal operation status.
Future probable damages on the machine are regarded as an operational error and is non-
warrantable.
From now on, you may turn the device into an activated status by pressing the “on” button on the device’s
microprocessor. After 15–20 minutes, it should be checked whether equipments on cooling circuit operate or
not. By this purpose, control procedures below should be gone through;
Gas Charge Status within the Circuit
Evaporation Pressure
Condensation Pressure
Contamination Status of Filters in Liquid Line
Power Used by Compressor
Operation Status of High Pressure Switch
Operation Status of Low Pressure Sensor
Operation Temperature of Compressor