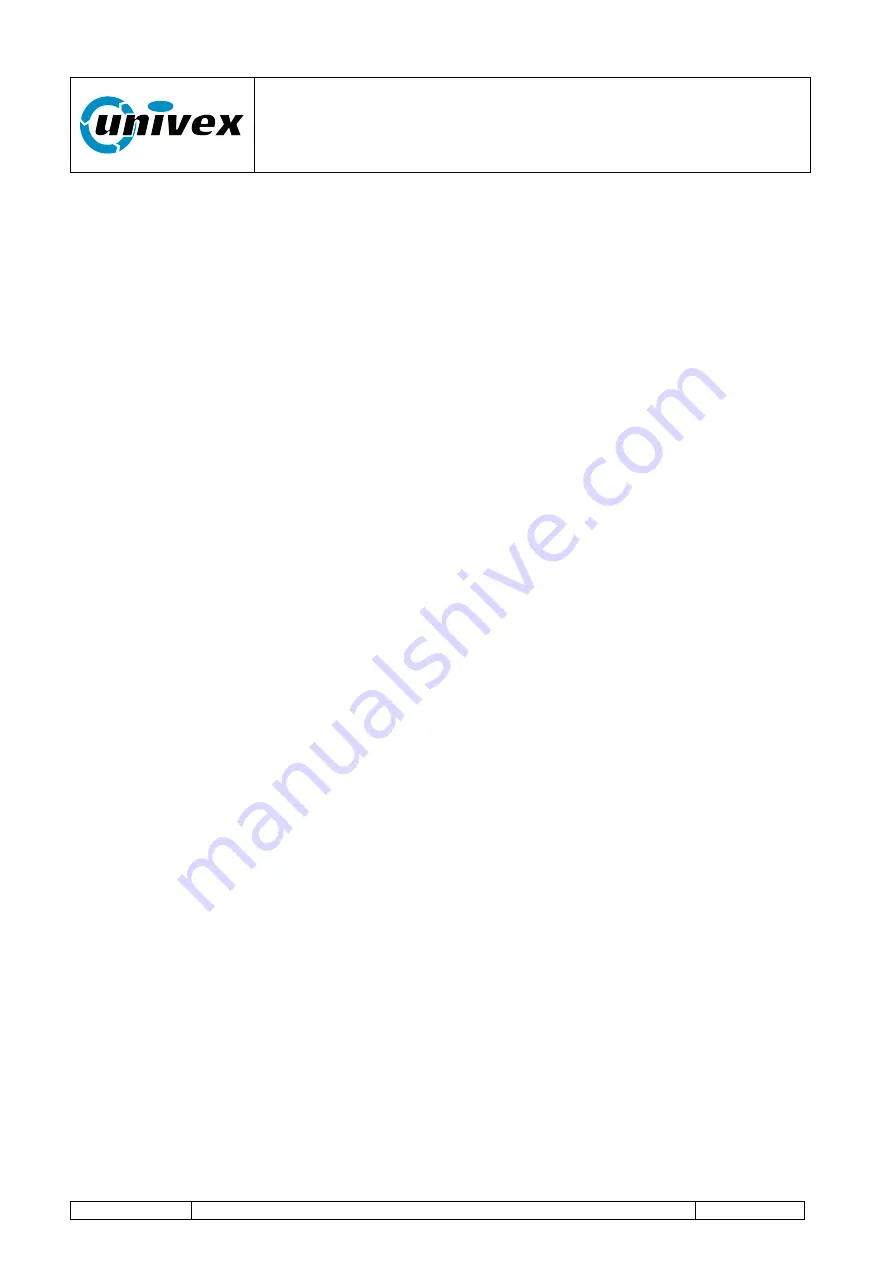
Gas burning pizza brickoven
R-001 100518
Page 3 of 33
Table of Contents
............................................................................................ 6
Manufacturer's name and address
....................................................................................... 9
Information on technical support and maintenance .............................................. 10
TECHNICAL INFORMATION AND SPECIFICATIONS
................................................. 11
................................................................................. 13
................................................................................... 14
7.3.1 Electrical specifications ......................................................................................... 18
7.4
.............................................................................................. 30
INTERVENTION REQUEST FORM - REPLACEMENT PARTS
................................. 31
.................................................................................... 32
................................................................................................ 32