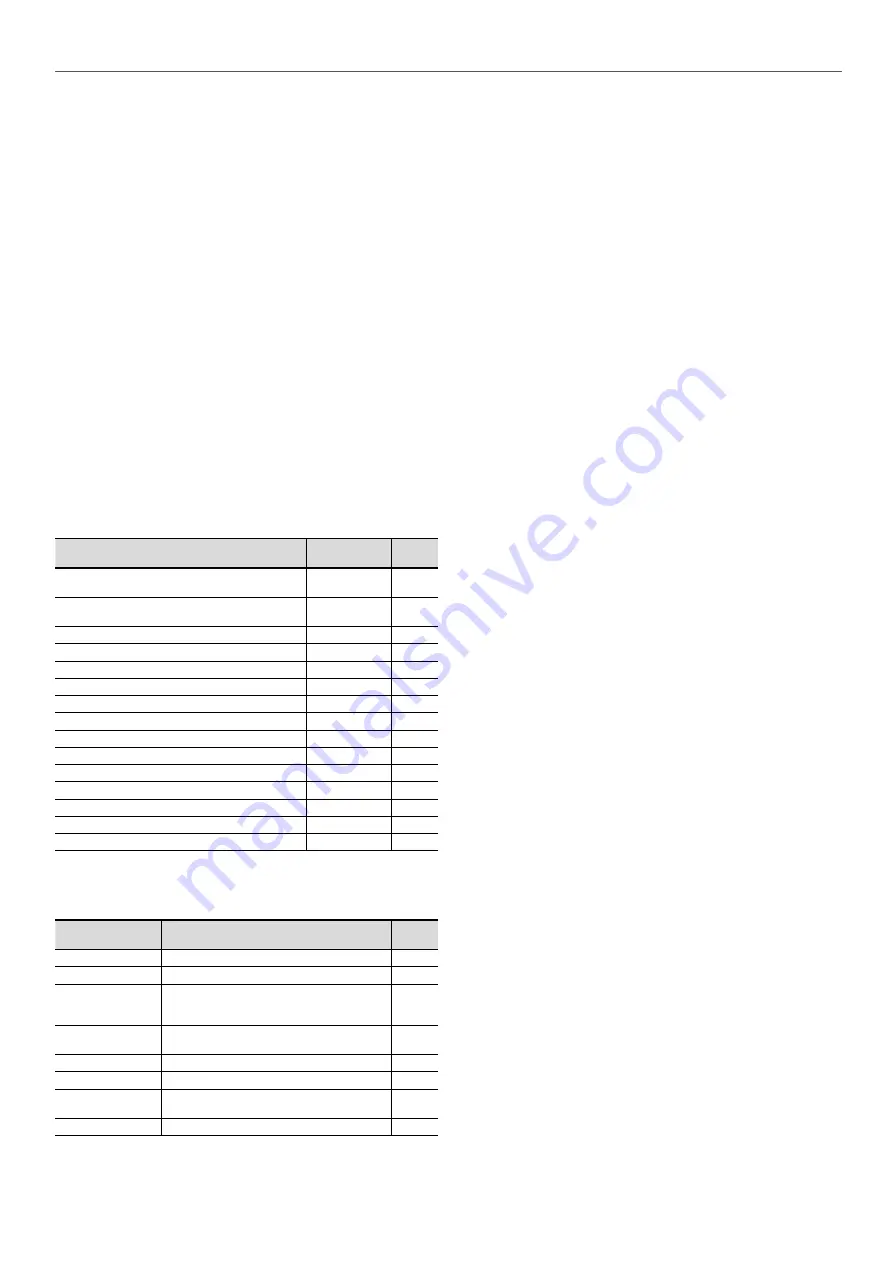
11.3 -
Level 3 (or higher) maintenance
Maintenance at this level requires specific skills, qualifications,
tools and expertise. Only the manufacturer, his representative or
authorised agent are permitted to carry out this work.
This maintenance work relates to the following:
-
Replacement of major components (compressor, water heat
exchanger),
-
Operations on the refrigerant circuit (handling refrigerant),
-
Modification of factory-set parameters (change of application),
-
Moving or dismantling the heat pump,
-
Any operation due to proven lack of maintenance,
-
Any operation covered by the warranty.
To reduce waste, the refrigerant and the oil must be transferred
in accordance with applicable regulations, using methods
that limit refrigerant leaks and pressure drops and with
materials that are suitable for the products.
Any leaks detected must be repaired immediately.
The compressor oil that is recovered during maintenance
contains refrigerant and must be treated accordingly.
Pressurised refrigerant must not left open to purge.
For a period of up to one day, cap all openings. If open for
longer, blanket the circuit with an inert gas (e.g. nitrogen) for
longer durations.
11.4 -
Tightening torques for the main electrical
connections
Component
Designation
in the unit
Value
(N.m)
Welded screw PE, customer connection (earth
connection)
-
40
Screw terminal, fuse holder
FU1, FU2,
FU3, FU4
10
Screw terminal, fuse holder
FU100
0,8-1,2
Screw terminal, compressor contactor
KM1-->KM12 3 - 4,5
Brass screw M6, compressor ground
EC-
5
M6 screw, compressor connection
EC-
5
Screw terminal, circuit breakers
QM-, QF-
2
Screw terminal, pump contactor
KM90, KM90A
2,5
M8 screw customer connection (size 160-270)
QS100
15 - 22
M10 screw customer connection (size 310-430)
QS100
30 - 44
M12 screw customer connection (size 470-520)
QS100
50 - 75
Screw terminal, circuit breakers(taille 160-330)
QF100
3,2-3,7
Screw terminal, circuit breakers (taille 380-520)
QF100
8-10
Screw terminal, fuse holder 32A (opt231)
Fu-
2,5
Screw terminal, fuse holder 100A (opt231)
Fu-
3,5 - 4
11.5 -
Tightening torques for the main bolts and
screws
Screw type
Use
Value
(N.m)
Metal screw D=4.8
Air coil sub-assembly, casing, supports
4,2
Metal screw D=6,3 Plastic grille volute
4,2
Taptite M10 screw
Air coil sub-assembly, chassis-structure,
electrical box fixing, plate heat exchanger
and pump
30
Taptite M6 screw
Pipe supports, enclosure, variable
frequency drive supports
7
H M6 screw
Pipe clip
10
H M10 nut
Compressor chassis, Compressor fixing
30
Oil equalisation
screw
Oil equalisation line
145
M16 screw
Refrigerant accumulator tank flange
180
11.6 -
Air coil
We recommend that coils with fins are inspected regularly to check
the degree of cleanliness. This depends on the environment where
the unit is installed, in particular urban and industrial sites, and for
units installed near trees that shed their leaves.
Recommendations for maintenance and cleaning of RTPF
coils:
-
Regularly cleaning the coil surface is essential for correct
unit operation.
-
Eliminating contamination and removal of harmful residue
will increase the operating life of the coils and the unit.
-
Specific recommendation in case of snow: For long term
storage, regularly check that no snow has accumulated on
the coil.
-
Use appropriate PPE including safety glasses and/or mask,
waterproof clothes and safety gloves. It is recommended that
clothing that covers the whole body is worn.
Level 1 cleaning
-
Remove all foreign objects or fragments/debris attached to
the coil surface or wedged between the chassis and the
supports.
-
Use a low pressure dry air jet to remove all traces of dust
from the coil, or use a brush in a careful, vertical motion.
Level 2 cleaning
-
Carry out the level 1 cleaning operations.
-
Clean the coil using suitable products.
Specific Carrier-approved products for cleaning RTPF coils
with untreated fins are available from the Carrier spare parts
network. The use of any other product is strictly prohibited.
After the cleaning product is applied, rinsing with water is
mandatory (see Carrier standard RW01-25).
IMPORTANT: Never use a pressure water spray without a large
diffuser. Concentrated and/or rotating water jets are strictly
prohibited.
Never use a fluid with a temperature above 45°C to clean the
air heat exchangers.
Correct and frequent cleaning (approximately every three
months) will prevent two-thirds of corrosion problems.
Protect the electrics box during cleaning operations.
11.7 -
Water heat exchanger maintenance
Check that:
-
The insulation has not been detached or torn during
operations,
-
The heaters and probes are operating and correctly
positioned in their support,
-
The water-side connections are clean and show no sign of
leakage,
-
The period inspections required by the local regulations have
been carried out.
11 - STANDARD MAINTENANCE
57
Summary of Contents for Carrier 30RQM 160
Page 63: ......