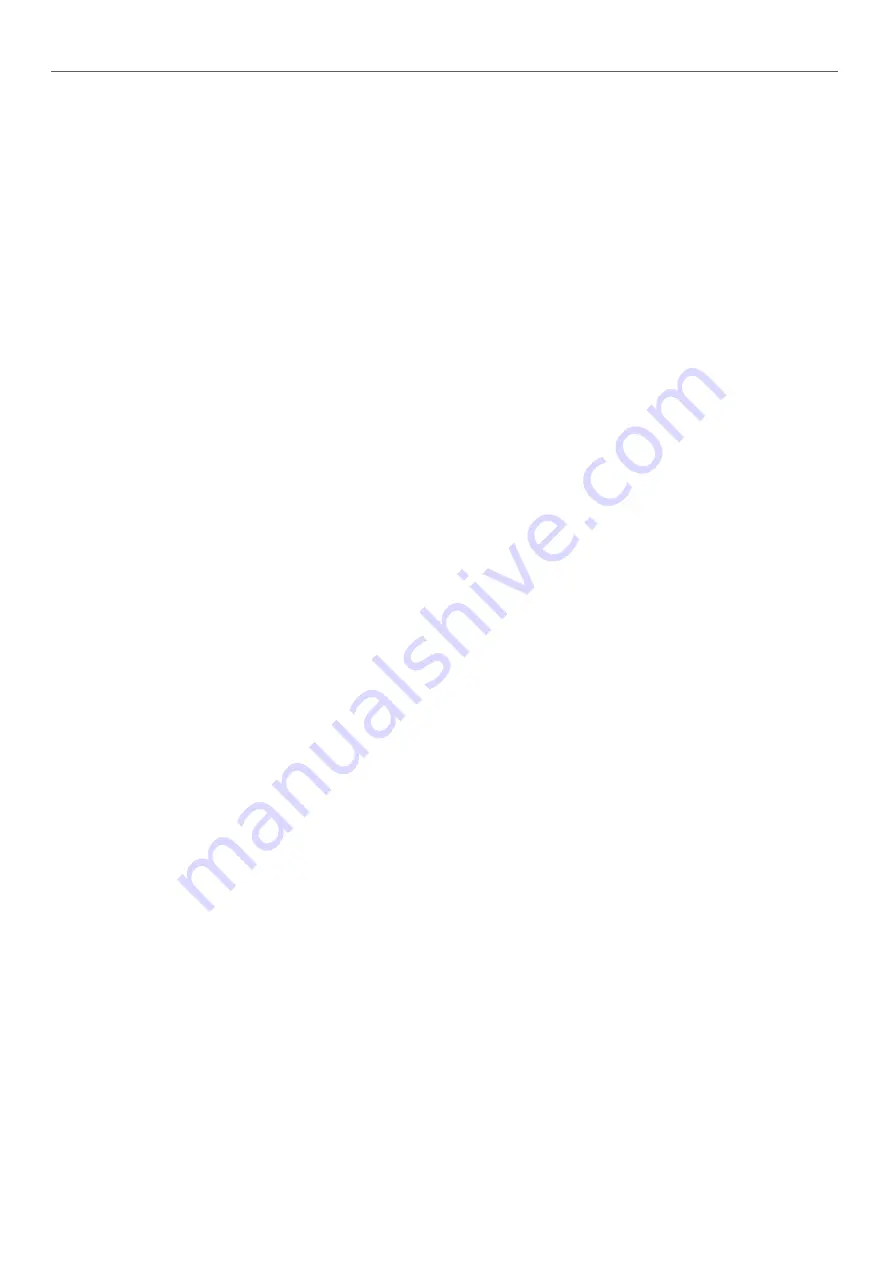
11 - STANDARD MAINTENANCE
To ensure optimal efficiency and reliability of the equipment and
all its functions, we recommend establishing a maintenance
contract with your local Carrier Service organisation. This contract
will include regular inspections by Carrier Service specialists so
that any malfunction is detected and corrected quickly, ensuring
that no serious damage can occur. A Carrier Service maintenance
contract is the best way to ensure the maximum operating life for
your equipment and, through the expertise of Carrier's qualified
personnel, provides the ideal way to manage your system energy
consumption effectively.
The refrigeration equipment must be sericed by professionals;
however, routine checks may be carried out locally by specially-
trained technicians. See the standard EN 378-4.
All refrigerant charging, removal and recovery operations
must be carried out by a qualified technician and with the
correct equipment for the unit. Any inappropriate handling
can lead to uncontrolled fluid or pressure leaks.
IMPORTANT: Before performing any work on the machine
ensure it is deenergized. If a refrigerant circuit is opened, it
must be evacuated, recharged and tested for leaks. Before
any operation on a refrigerating circuit, it is necessary to
evacuate the refrigerant charge from the device using a
charge transfer unit.
Simple preventive maintenance will allow you to get the best
performance from your heat pump:
-
Improved refrigerating performance,
-
Reduced electricy consumption,
-
Accidental breakge of components prevented,
-
Prevention of major time-consuming and costly interventions,
-
Protection of the environment.
There are five maintenance levels for the heat pump, as defined
by the AFNOR X60-010 standard.
NOTE: Any deviation from or failure to adhere to these
maintenance criteria will render the warranty conditions for
the heat pump null and void, and release the manufacturer,
Carrier SCS, from any liability.
11.1 -
Level 1 maintenance
These simple procedures can be carried out by the user:
-
Visual check for traces of oil (indicates a refrigerant leak),
-
Check for leaks in the hydraulic circuit (monthly),
-
Clean the air heat exchangers (see chapter 11.6 Air coil -
Level 1 cleaning),
-
Check that the protective grilles are present and in good
condition, and that the doors and covers are properly closed,
-
Check the unit's alarm report (see 30RQM/30RQP control
manual),
-
Verify the refrigerant charge in the liquid line sight glass,
-
Verify the chilled water temperature difference at the heat
exchanger outlet is correct,
-
Check for any general signs of deterioration,
-
Check the anti-corrosion coatings.
11.2 -
Level 2 maintenance
This level requires specific expertise in electrical, hydraulic and
mechanical systems. This expertise may be available locally:
maintenance service, industrial site, specialist subcontractor.
The frequency of this maintenance may be monthly or annual,
depending on the type of check.
In these cases, the following maintenance operations are
recommended:
Carry out all level 1 operations, then:
Electrical checks (annual checks):
-
At least once a year tighten the electrical connections for the
power supply circuits (see tightening torques table),
-
Check and tighten all control connections, if required,
-
Check the labelling of the system and instruments, re-apply
the missing labels if required,
-
Remove the dust and clean the interior of the electrical boxes.
Be careful not to blow dust or debris into components; use
a brush and vacuum wherever possible,
-
Clean the insulators and bus bar supports (dust combined
with moisture reduces the insulation gaps and increases
current leakage between phases and from phase to ground),
-
Check the presence, condition and operation of electrical
protective devices,
-
Check the presence, condition and operation of control
components,
-
Check that all heaters are operating correctly,
-
Replace the fuses every 3 years or every 15000 hours
(ageing),
-
Check that no water has penetrated into the electrical box,
-
On the electrical box and for units equipped with a variable
frequency drive, regularly check the cleanliness of the filter
media to maintain the correct air flow.
-
Check the correct operation of the capacitor (power factor
correction option 231)
Mechanical:
-
Check the tightness of the fan sub-assemblies, fan,
compressor and electrical box fixing bolts.
Hydraulic:
-
When working on the hydraulic circuit, take care not to
damage the adjacent air heat exchanger,
-
Verify the hydraulic connections,
-
Check the condition of the expansion tank (presence of
corrosion or loss of gas pressure) and replace it if required,
-
Drain the hydraulic circuit,
-
Clean the water filter,
-
Replace the gland packing of the pump after 20000 hours of
operation and the bearings after 17500 hours,
-
Check the operation of the low water flow safety device,
-
Check the condition of pipe thermal insulation,
-
Check the concentration of the anti-freeze protection solution
(ethylene glycol or propylene glycol),
-
Check the water flow using the heat exchanger pressure
difference,
-
Check the condition of the heat transfer fluid or the water
quality,
-
Check for corrosion of the steel pipe work.
Refrigerant circuit checks:
-
Clean the air heat exchangers (see chapter 11.6 Air coil -
Level 2 cleaning),
-
Check the unit operating parameters and compare them with
the previous values,
-
Check the operation of high pressure switches. Replace as
necessary.
-
Check the fouling of the filter drier. Replace it if required.
-
Keep an up-to-date service booklet attached to the heat pump
in question.
Ensure all adequate safety measures are taken for all these
operations: use appropriate PPE (personal protective
equipment), comply with all industry and local regulations,
use common sense.
56
Summary of Contents for Carrier 30RQM 160
Page 63: ......