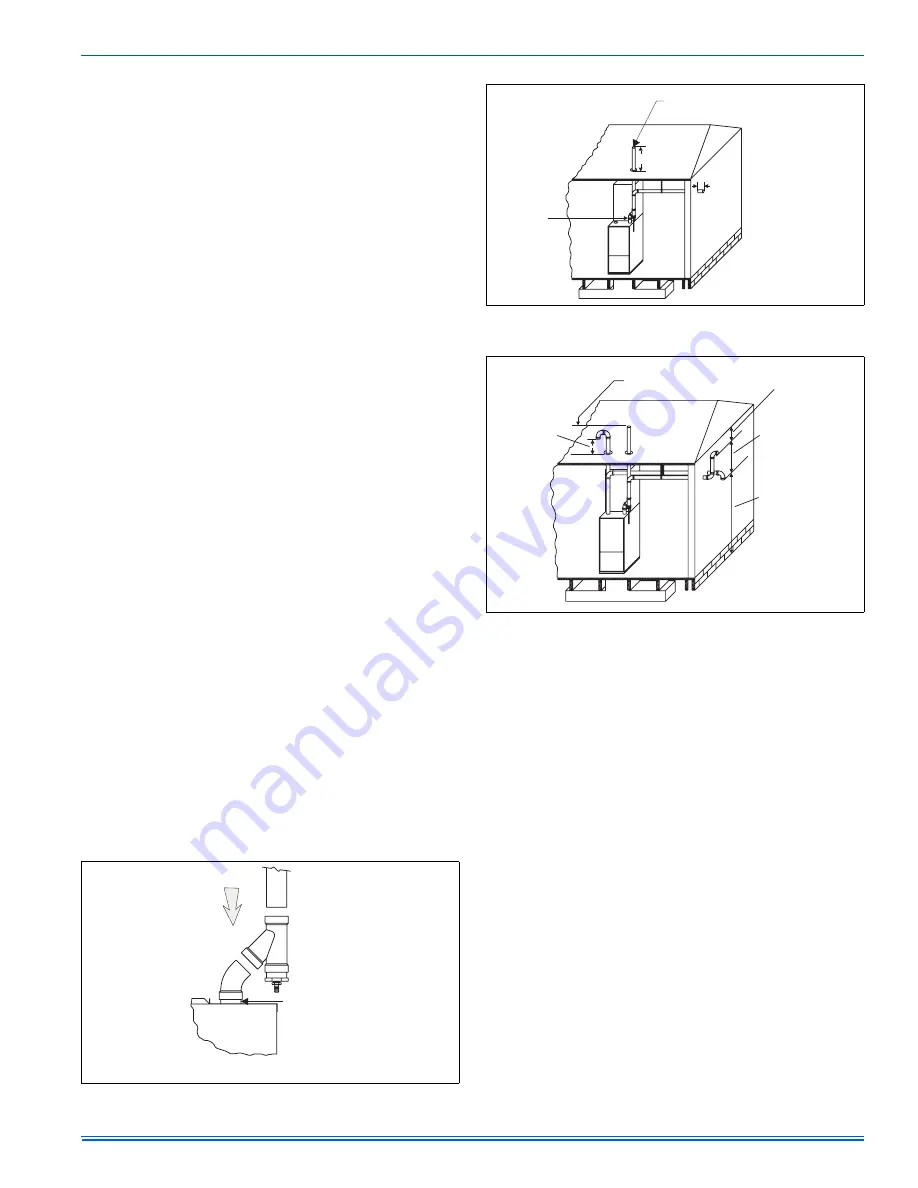
268882-UIM-A-0407
Unitary Products Group
15
VENT SYSTEM
This furnace is certified to be installed with one of two possible vent
configurations.
1.
Horizontal vent system. This vent system can be installed com-
pletely horizontal or combinations of horizontal, vertical, or offset
using elbows.
2.
Vertical vent system. This vent system can be installed completely
vertical or a combination of horizontal, vertical, or offset using
elbows.
HORIZONTAL VENT APPLICATIONS AND
TERMINATION
When selecting the location for a horizontal combustion air / vent termi-
nation, the following should be considered:
1.
Observe all clearances listed in vent clearances in these instruc-
tions.
2.
If installing a vertical venting system through any unconditioned
space such as an attic or crawl space, it must be completely insu-
lated to a minimum "R" value of 3.5 either by blown in or wrapped
insulation.
3.
Termination should be positioned where vent vapors will not dam-
age plants or shrubs or air conditioning equipment.
4.
Termination should be located where it will not be affected by wind
gusts, light snow, airborne leaves or allow recirculation of flue
gases.
5.
Termination should be located where it will not be damaged or
exposed to flying stones, balls, etc.
6.
Termination should be positioned where vent vapors are not objec-
tionable.
7.
Horizontal portions of the vent system must slope upwards and be
supported to prevent sagging. The vent system may be supported
by the use of clamps or hangers secured to a permanent part of
the structure every 4 ft. (1.22 m) and that is is angled a minimum
of 1/4" per foot (0.635 cm/m) so that condensate will flow towards
the furnace.
8.
Sealed combustion air systems must be installed so the vent and
the combustion air pipes terminate in the same atmospheric zone.
Refer to Figure 18.
DOWNFLOW VENT ASSEMBLY
1.
Place the 2” (5.1 cm) 45° PVC street elbow on the vent connection
shown in Figure 16.
2.
Place the 2” (5.1 cm) PVC WYE (“Y”) assembly on the 2” (5.1 cm)
45° PVC street elbow as shown in Figure 16.
3.
Locate the rubber condensate hose in front of the blower access
panel.
4.
Slide the hose through the hole in the top cover, and insert the
hose on to the barbed fitting on the bottom of the 2” (5.1 cm) PVC
WYE (“Y”) assembly as shown in Figure 16.
Place 2” rubber sleeve of PVC pipe at top of furnace and place a 2”
piece of PVC pipe in the other end of the 2” rubber sleeve.
VERTICAL VENT APPLICATIONS AND
TERMINATION
Roof mounted vertical terminals may be field fabricated. Standard PVC/
SRD fittings may be used. If installing a vertical venting system through
any unconditioned space such as an attic or crawl space it must be
completely insulated to a minimum "R" value of 3.5.
1.
Observe all clearances listed in vent clearances in these instruc-
tions.
2.
Termination should be positioned where vent vapors are not objec-
tionable.
3.
Termination should be located where it will not be affected by wind
gusts, light snow, or allow recirculation of flue gases.
4.
Termination should be located where it cannot be damaged,
plugged or restricted by tree limbs, leaves and branches.
5.
Horizontal portions of the vent system must slope upwards and be
supported to prevent sagging. The vent system may be supported
by the use of clamps or hangers secured to a permanent part of
the structure every 4 ft. (1.22 m) and that it is angled a minimum of
1/4" per foot (0.635 cm/m) so that condensate will flow towards the
furnace.
FIGURE 16:
Downflow Vent Assembly
DOWNFLOW
2” (5.08 cm)
VENT PIPE
2” PVC
WYE
2” PVC
45°
ELL
FURNACE
VENT PIPE
RETURN
AIR
FIGURE 17:
Termination Configuration - 1 Pipe (Modular Installations
Only)
FIGURE 18:
Termination Configuration - 2 Pipe
12” MIN.
12” MIN.
MAINTAIN 12” MINIMUM CLEARANCE
ABOVE HIGHEST ANTICIPATED SNOW
LEVEL. MAXIMUM 24” ABOVE ROOF.
2” RUBBER
SLEEVE
COUPLING
MAINTAIN 12”
MINIMUM
CLEARANCE
ABOVE HIGHEST
ANTICIPATED
SNOW LEVEL.
12” VERTICAL SEPARATION
BETWEEN COMBUSTION AIR
AND VENT
12” MINIMUM
BELOW
OVERHANG
12” MINIMUM
SEPARATION
BETWEEN BOTTOM
OF COMBUSTION
AIR PIPE AND
BOTTOM OF VENT
MAINTAIN 12”
MINIMUM CLEARANCE
ABOVE HIGHEST
ANTICIPATED SNOW
LEVEL OR GRADE,
WHICHEVER IS
HIGHER