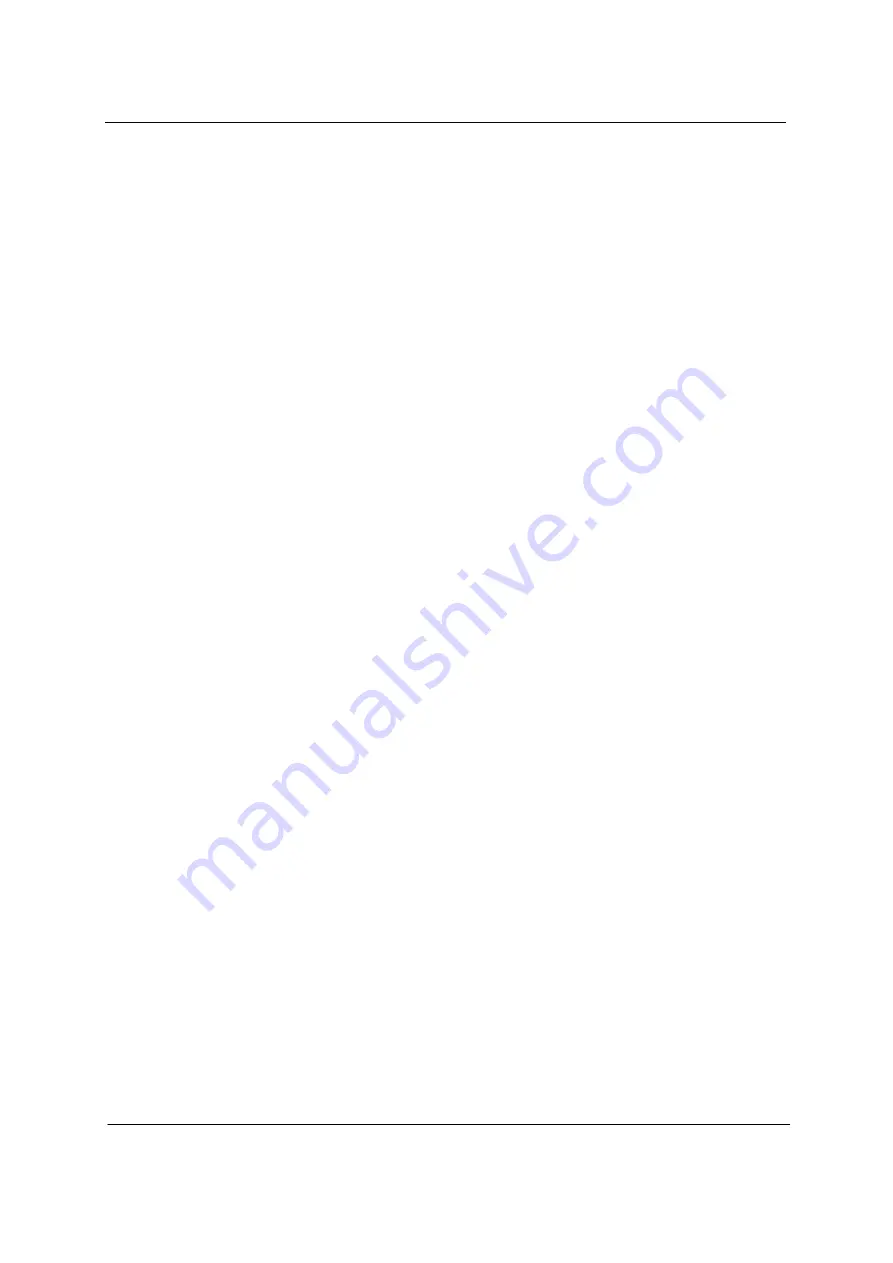
USSI Microlok II Functional description
UM-6800A Rev1.3 July 2005 Page 17 of 27
compilation of application program. This information is clearly defined and
available to the user in the listing file (.mll), which is one product of
compiling an application text file (.ml2). If this file is unavailable, the user
can determine the jumper settings by following the instructions below. By far
the best way to determine the jumper settings, however, is to use the list file.
The jumper settings for each board are determined by the order in which the
boards are defined in the application. The jumper settings do not depend on
the order of the boards that happen to appear in the card file. If the
application program and list file are both unavailable, then the order can also
be found by looking at the configuration menu in the Microlok II
Maintenance Tool.
•
Each address select PCB consists of 6 Nos. of jumpers.
•
Each slot will have its own jumper setting and each one is different from
others.
•
The address select PCB ensures the type of board used in the slot as
defined in the application logic.
•
48 pin address select PCB is used for vital boards & 96-pin address select
PCB is used for non-vital boards
4.1.9. KEYING PLUG
Each of the Microlok II card file slots includes a 12-way female keying guide
next to the 96-pin connector. The guide is used to ensure installation of the
proper circuit board in each card file slot after the complete card file board
configuration has been determined. Each board is equipped with a
corresponding 12-way male keying guide; individual keying tabs are removed
at the factory in a specific pattern for the board part number. Prior to
installing a board, insert keying plugs into the corresponding card file
motherboard keying guide. If it becomes necessary to change the type of
board installed in a given slot, the previously installed keying plugs can be
removed using a knife or a pair of needle nose pliers.
5.1. SERIAL I / O
•
The system will support a minimum of three kind of active ports for
Application Interface processing that is RS-232, RS-423 and RS485
•
All ports will provide, at minimum, Transmit (TXD) and Receive (RXD) data
signals and Request To Send (RTS) and Data Carrier Detect (DCD) control
signals. At least one port will provide a control input for Clear To Send
(CTS)
•
All control lines for all ports will be accessible such that each port can be
modified to support different electrical properties without modification to
the base PCB on which the port resides.