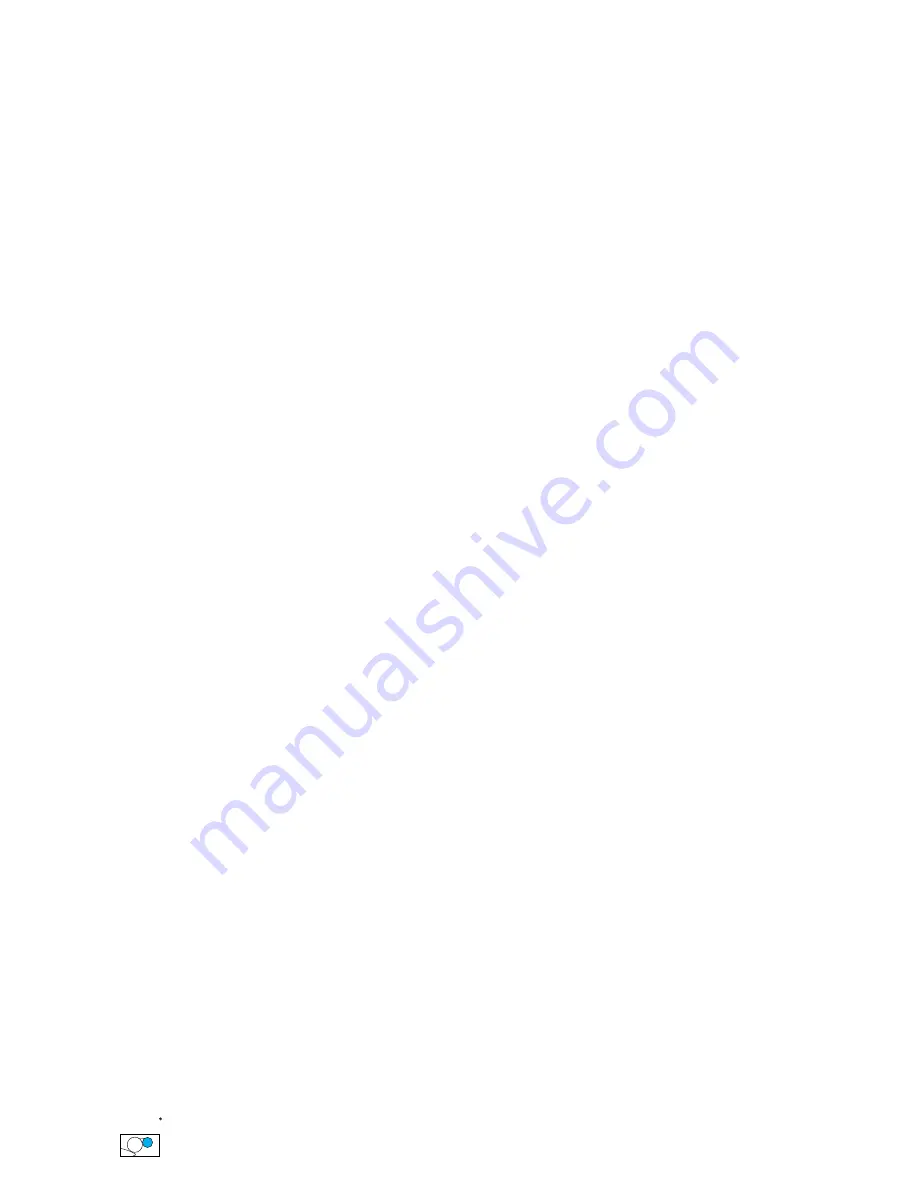
28
Production Considerations
The
iColor coater
, in many ways, far exceeds the production needs for most jobs. We recommend
that, prior to production; you review some of the following suggestions for trouble free and reduced
cost operation.
1.
Slower is smoother. Coating needs time to settle (flow out). There are a few ways to accomplish
this:
b.
Slowing down the conveyor (which increases flow out time)
c.
Using a thin viscosity coating (somewhat limited by your print engine)
d.
Warming the coating (which increases flow out)
The challenge is to balance the look of the product with desired production speed. If you are
using a toner based printer you must keep in mind that your toner will re-wet at around 120ºF
(40º) or slightly above. In order to get the best look you have to match the speed of the con
-
veyor with the lamp intensity. Generally the belt speed will be between 25 - 50% with the lamp
intensity between 50 - 75%.
2.
It is sensible to use the lowest level of energy needed to do a job. For example: running the lamp on
a setting of 50% would save you nearly 50% of the energy required to power the bulb on the maxi-
mum setting.
3. The coating should be stored in a climate-controlled environment. As coating gets colder it thickens
and is much harder to deal with. Ideally coating likes to be at a temperature between 70-90°F
(21-32°C). This allows for good flow out and a smooth look.
4. Paper can make a tremendous difference in the way your coating looks, especially absorbent paper.
The same job run on the same printer with different paper can coat differently. The most noticeable
effect of absorbent paper is that after being coated the printed area looks good however the unprint-
ed area appears to have not received enough coating. Three potential solutions are to increase the
belt speed, increase the amount of coating going to the paper or use a thicker coating.
5. When operating the
iColor coater
, the form roller
SHOULD NOT
be in contact with the impression
roller
except the very ends of the roller that are slightly larger due to the pressure from the seals.
Even
this small amount of contact can be eliminated by making sure that the coating lever is in the
OFF
position when not feeding paper. This will eliminate the possibility of any coating getting onto
the
reverse side of the product being run.
6. Any time you stop the coater check for stray coating. If any is found, clean with a lint free rag and
Uninet
approved cleaning solution. This will help to insure trouble free operation of your coater.