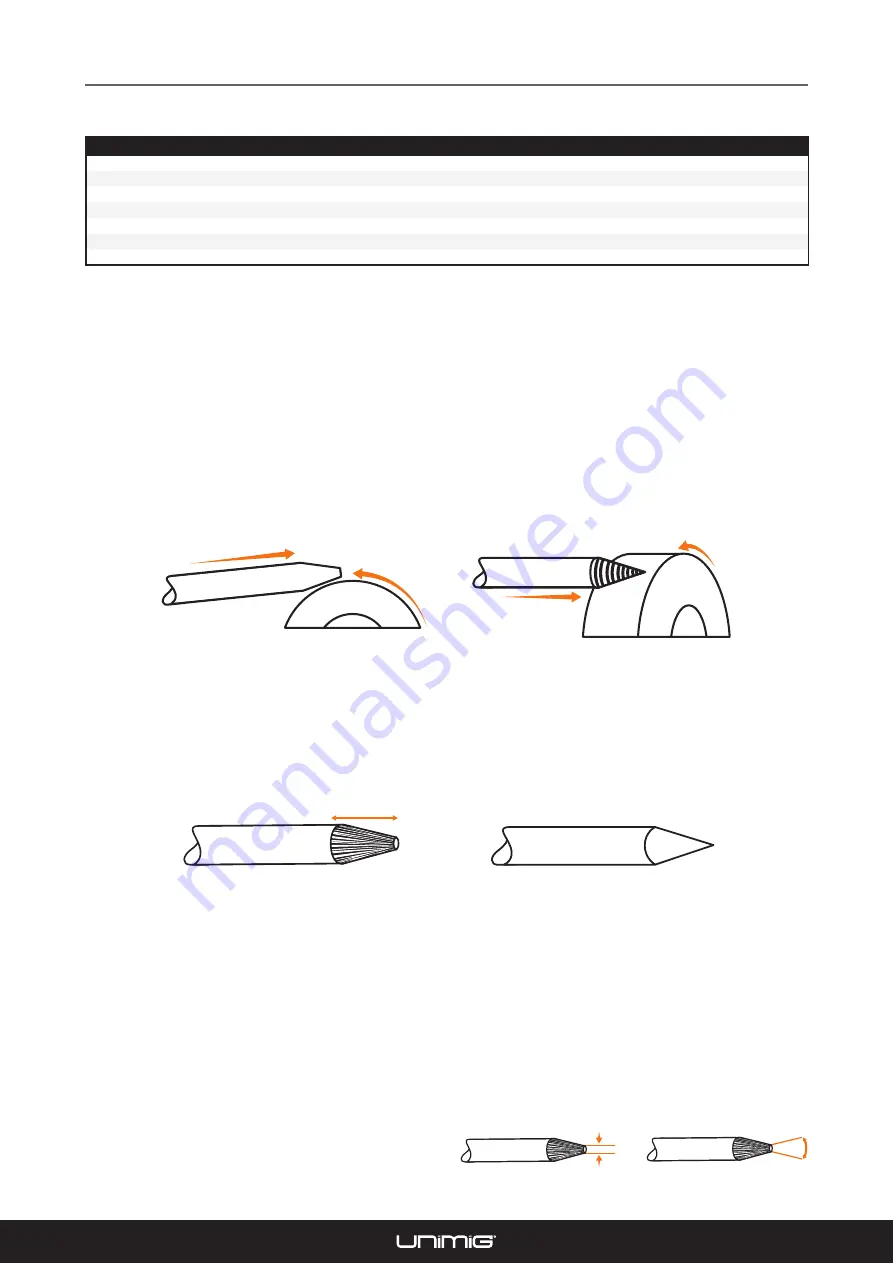
Electrode Included Angle/Taper - DC
Tungsten electrodes for DC welding should be
ground longitudinally and concentrically with
diamond wheels to a specific included angle in
conjunction with the tip/flat preparation. Different
angles produce different arc shapes and offer
different weld penetration capabilities. In general,
blunter electrodes that have a larger included angle
provide the following benefits:
• Last Longer
• Have better weld penetration
• Have a narrower arc shape
• Can handle more amperage without eroding.
Sharper electrodes with smaller included angle
provide:
• Offer less arc weld
• Have a wider arc
• Have a more consistent arc
The included angle determines the weld bead shape
and size. Generally, as the included angle increases,
penetration increases and bead width decreases.
Tungsten Electrodes Rating for Welding Currents
Tungsten Diameter (mm)
Diameter at the Tip (mm)
Constant Included Angle (°)
Current Range (Amps)
Current Range (Pulsed Amps)
1.0mm
0.25
20
5 - 30
5 - 60
1.6mm
0.5
25
8 - 50
5 - 100
1.6mm
0.8
30
10 - 70
10 - 140
2.4mm
0.8
35
12 - 90
12 - 180
2.4mm
1.1
45
15 - 150
15 - 250
3.2mm
1.1
60
20 - 200
20 - 300
3.2mm
1.5
90
25 - 250
25 - 350
Tungsten Preparation
Always use DIAMOND wheels when grinding and cutting. While tungsten is a tough material, the surface of
a diamond wheel is harder, and this makes for smooth grinding. Grinding without diamond wheels, such as
aluminium oxide wheels, can lead to jagged edges, imperfections, or poor surface finishes not visible to the
eye that will contribute to weld inconsistency and weld defects.
Always ensure to grind the tungsten in a longitudinal direction on the grinding wheel. Tungsten electrodes
are manufactured with the molecular structure of the grain running lengthwise and thus grinding crosswise
is “grinding against the grain.” If electrodes are ground crosswise, the electrons have to jump across the
grinding marks, and the arc can start before the tip and wander. Grinding longitudinally with the grain causes
the electrons to flow steadily and easily to the end of the tungsten tip. The arc starts straight and remains
narrow, concentrated, and stable.
Grind longitudinal on the
grinding wheel
2.5x tungsten diameter
Flat tip
Pointed tip
Flat spot
diameter
Included
angle
Don’t grind across
the grinding wheel
Electrode Tip/Flat
The shape of the tungsten electrode tip is an important process variable in precision arc welding. A good
selection of tip/flat size will balance the need for several advantages. The bigger the flat, the more likely arc
wander will occur and the more difficult it will be to arc start. However, increasing the flat to the maximum
level that still allows arc start and eliminates arc wonder will improve the weld penetration and increase the
electrode life. Some welders still grind electrodes to a sharp point, which makes arc starting easier. However,
they risk decreased welding performance from melting at the tip and the possibility of the point falling off into
the weld pool.
TIG WELDING GUIDE
30
Summary of Contents for RAZOR 320 AC/DC
Page 1: ...RAZOR 320 AC DC KUMJRRW320ACDC Operating Manual...
Page 2: ...2...
Page 45: ...NOTES 45...
Page 46: ...NOTES 46...
Page 47: ...NOTES 47...