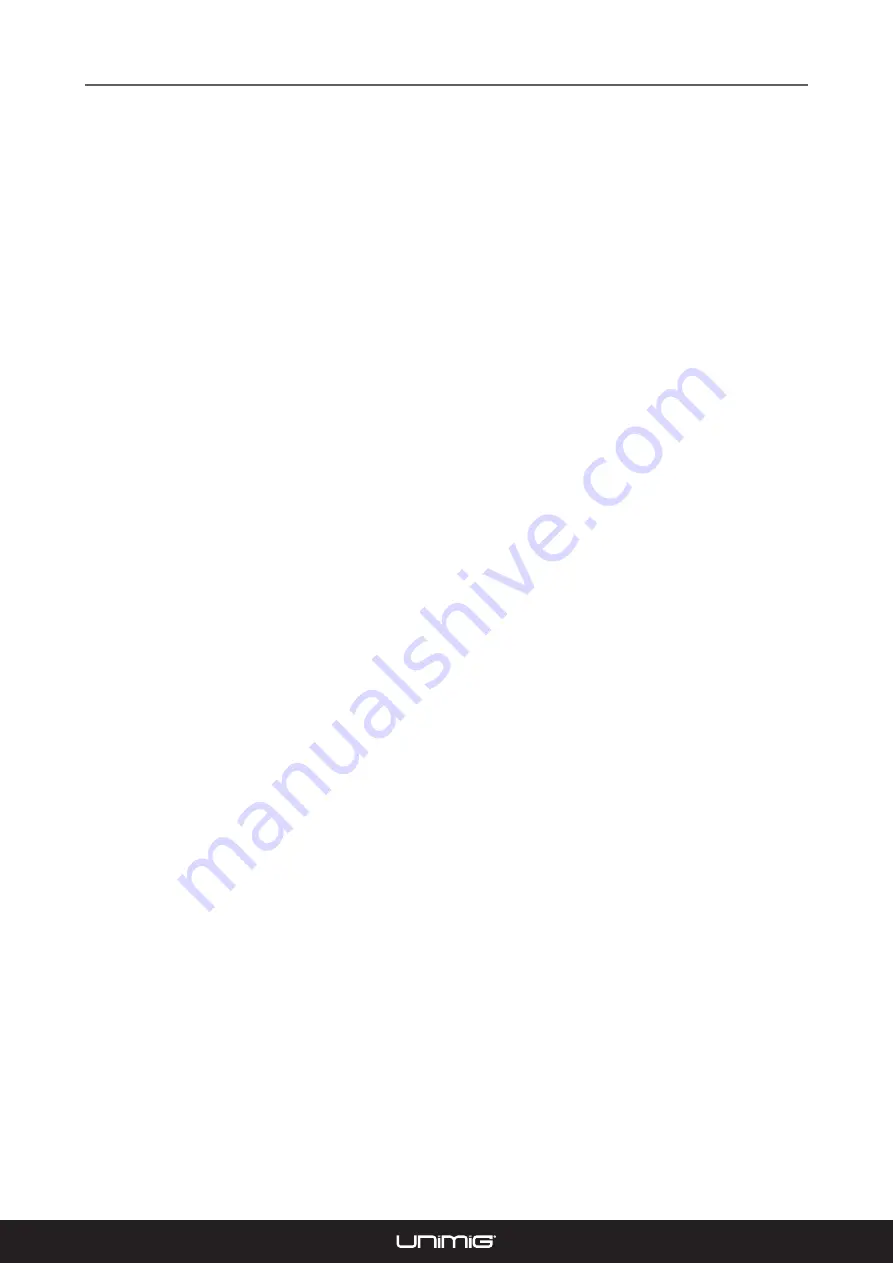
DC MMA ELECTRODE POLARITY - What is the electrode polarity and why
is it important.
When using a DC power source, the question of whether to use electrode negative or positive polarity arises.
Direct current flows in one direction in an electrical circuit and the direction of current flow and the
composition of the elec-trode coating will have a definite effect on the welding arc and weld bead. Refer to
the electrode manufacturers recommenda-tion for polarity choice.
With DC electrode (+) positive (reverse) polarity, more heat is generated at the workpiece. This produces welds
with deep penetration and a narrower weld bead and can reduce the incidence of lack-of-fusion defects in the
weld.
DC electrode (-) negative (straight) polarity generates more heat at the electrode and produces welds with
shallower penetration. DC (-) negative electrode results in a higher burn off rate and therefore a higher
deposition rate at a given current. It is generally the chosen polarity for most GP Electrodes.
AC MMA ELECTRODE Welding.
AC MMA (Stick) welding came about from old technology of AC transformer welding machines. Electrodes
were manufactured to run on these AC machines. In fact, the electrodes made for AC welding will usually
perform better on DC. AC is much louder and delivers a more violent arc which can cause inclusions and slag
in the weld. Generally AC is more diffcult to weld with than DC.
There can be a a phenomenon called “arc-blow” with DC current where a magnetic field can build up and
push the arc off to one side. If you are having issues with magnetism creating arc blow then the AC can help
stabilise the arc and bring things back in line.
But for most other applications, AC is not needed. There are some Aluminium MMA electrodes available that
do require AC current.
ARC FORCE - What is the Arc Force Control and what does it do?
During welding arc voltage drops as the arc gets tighter and can cause the electrode to stick to the work
piece. Arc force should be set according to the electrode diameter, electrode type, welding current and the
technical requirement.
When you set the arc force high the machine senses the drop in voltage, as the electrode is about to stick/
short circuit to the work piece the machine responds by increasing the arc voltage and welding current
momentarily (per millisecond). This boost in arc voltage/current blasts away base metal and elec-trode to
prevent the electrode from sticking itself to the work piece.
High arc force means the molten droplet from the melting electrode is larger with quicker transistion
preventing the electrode from sticking, however too much arc force may create excessive spatter. Low arc
force will result in a softer arc with minimal spatter and a nice shaped weld bead, however it may lead to the
electrode sticking to the work piece easier, therefore the arc force should be adjusted to provide a smooth arc
transistion between the electrode and workpiece without it sticking and without providing excessive spatter.
Higher Arc Force is more suited to thicker electrodes under low amperage settings, out of postion welding,
low hydrogen type electrodes where a forceful arc characteristic is preferred to maintain the arc and better
control penetration. Lower Arc Force is better suited to hardfacing and cast Iron electrodes where a soft
buttery arc is preferred to prevent the electrode material diluting too much with the base metal.
MMA (STICK) ADDITIONAL NOTES
35
Summary of Contents for RAZOR 320 AC/DC
Page 1: ...RAZOR 320 AC DC KUMJRRW320ACDC Operating Manual...
Page 2: ...2...
Page 45: ...NOTES 45...
Page 46: ...NOTES 46...
Page 47: ...NOTES 47...