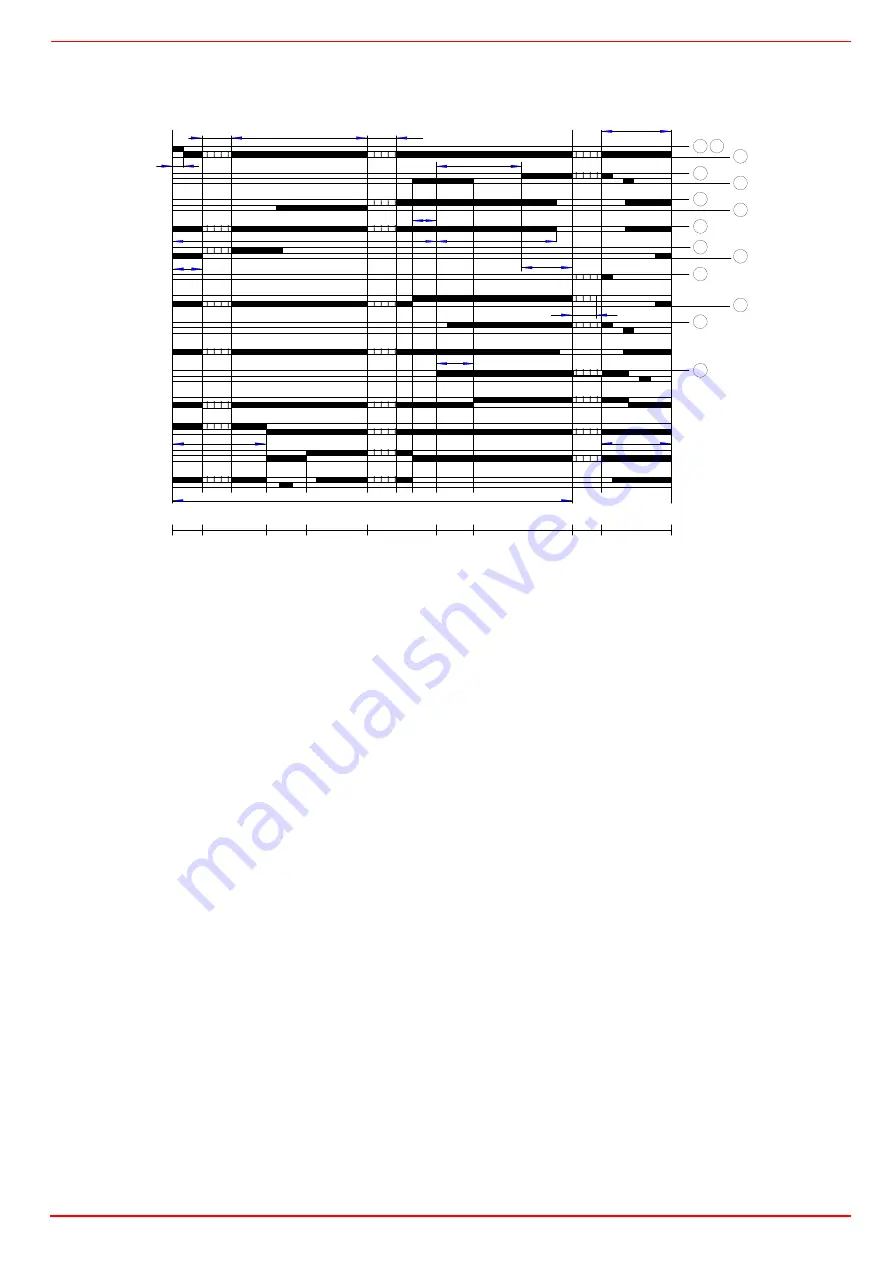
Sequence diagram
Key
t1
Prepurge time with air damper fully open
t2
Safety time
t3
Preignition time, short («Z» connected to terminal 16)
T3’
Preignition time, long («Z» connected to terminal 15)
t3n
Postignition time («Z» connected to terminal 15)
t4
Interval between voltage at terminals 18 and 19 («BV1-BV2»)
t5
Interval between voltage at terminals 19 and 20 («BV2» load
controller)
t6
Postpurge time (with «M2»)
t7
Interval between start command and voltage at terminal 7 (start
delay time for «M2»)
t8
Duration of startup sequence (excluding «t11» and «t12»)
t10
Interval from startup to the beginning of the air pressure check
t11
Air damper running time to the OPEN position
t12
Air damper running time to the low-fire position (MIN)
t13
Permissible afterburn time
t16
Interval to the OPEN command for the air damper
t20
For self-shutdown of the sequence switch
A
t1 1
t7
t1
t1 2
t4
t3
t3 n
B
C
D
t6
t3 "
t2
t5
t2 0
t1 3
t10 *
t1 6
t8
20
4
7
1 9
8
17
15
9
9
10
*
I
II
III
IV
V
V I
V II
V III
IX
X
X I
X II
X III
X IV
a
b
a
b
a
b
a
b
a
b
a
b
a
b
a
b
a
b
a
b
a
b
*
1 2
16
11
1 8
Control output at terminal
Lockout position indication