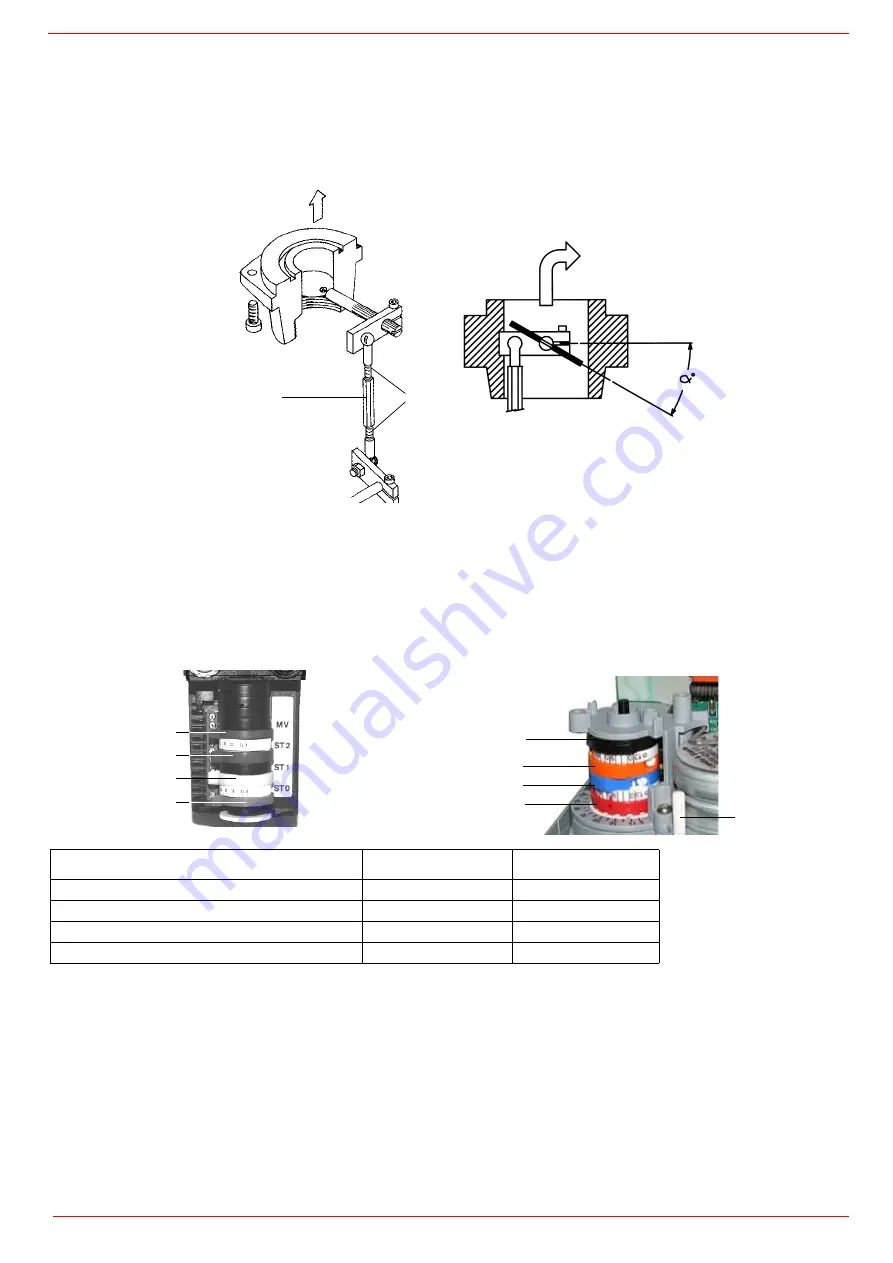
PART III: OPERATION
37
Double-stage burners
9
drive the burner to the low flame stage by means of the
TAB
thermostat;
10 ;In order to change the gas flow rate slacken the nuts
DB
(Fig. 27) and adjust the opening angle of the gas butterfly valve by rota-
ting the rod
TG
(clockwise rotation increases gas flow, anticlockwise rotation decreases it). The slot on the butterfly valve shaft
shows the opening degree of the valve regardingthe horizontal axis (Fig. 27).
NOTE:
At the end of settings, make sure the locking screws
RA
and
DB
are fully tightened.
Fig. 27
11 Now adjust the pressure switches (see page 42).
12 If it is necessary to change the burner output in the low flame stage, move the low flame cam: the low flame position matches the
ignition position. As far as burners fitted with Dungs MBC gas valves, the low flame cam does not match the ignition cam position,
that is why it must be set at about 30° more than the ignition cam.
13 Turn the burner off and then start it up again. If the adjustment is not correct, repeat the previous steps.
Berger STA: on this actuator, the manual control of the air damper is not provided; the setting of the cams is carried out working
with a screwdriver on the
VS
screw placed on the cam.
Berger STA12: a key is provided to move the cams.
Siemens SQN72: a key is provided to move cams I and IV, the other cams can be moved by means of screws.
On the BERGER STA12B3.41 actuator, the manual air damper control is not provided. On the Siemens actuator the AUTO/MAN mode
is provided (see picture).
Berger STA6 B 3.41 (high-low flame burners)
Siemens SQN72.2A4Axx (high-low flame burners)
For DUNGS MB-DLE / Siemens VGD gas valves
Actuator camsBerger
STA
Siemens SQN72
High flame position (set to 90°)
ST2
I (red)
Low flame and ignition position
ST1
III (orange)
Stand-by position (set to 0°)
ST0
II (blue)
Not used
MV
IV (black)
TG
DB
MV
ST2
ST1
ST0
IV
III
II
I
AUTO/MAN