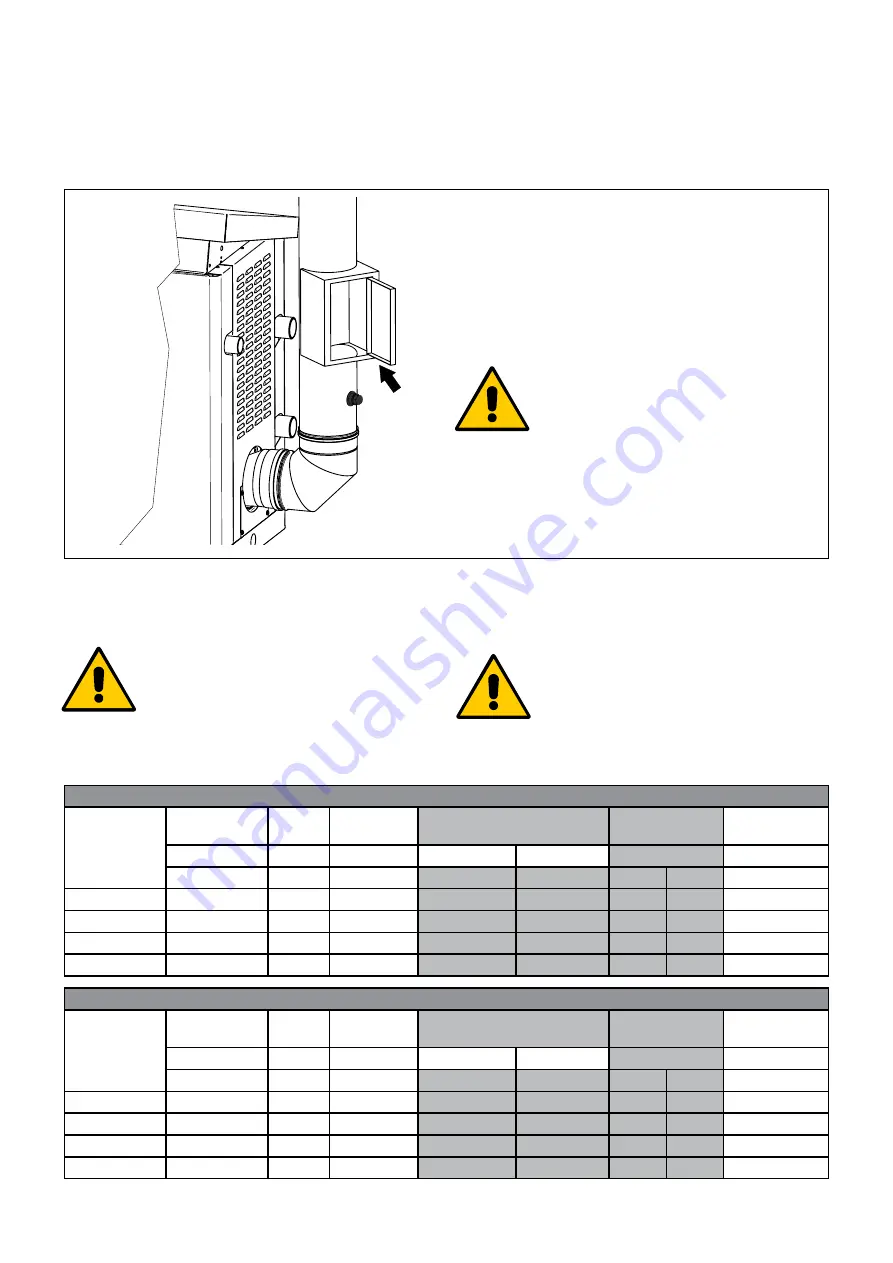
36
Follow this procedure to also adjust the other modules.
If the capacity read is too low, make sure the power feed and
drain system (feed and drain pipes) are not clogged.
If they are not clogged, make sure the burner and/or heat ex-
changer is not dirty.
C) CONCLUsION OF ThE BAsIC CALIBRATIONs
- check the co2 values at minimum and maximum levels.
- If necessary, make any adjustments.
For proper operation, the CO
2
values must be
calibrated with particular attention, observing
the values indicated in the table.
NOTE: Do not force the end stroke limits of
the adjustment screw.
ATTENTION
To calibrate the
vG (Gas valves)
in the
boiler room, follow the procedures below.
The vG must be calibrated
with chimney pressure = 0 Pa;
for this reason:
- open the smoke duct 1 inspection door,
after calibration, restore the door gasket.
NOZZLEs - PREssURE - CAPACITY TABLE
MODULEX EXT: 100 - 150 - 200 - 250 - 300 - 350
Type of Gas
Supply Press.
Ø noz-
zles
collector
fan speed
co
2
levels
Start.
power
[mbar]
(mm)
[mm]
min fl
max fu
[%]
[%]
min
max
IG
nat. gas (G20)
20
7
-
31
98
9.1
9.1
80
nat. gas (G25)
25
9
-
31
98
9.1
9.1
80
nat. gas (G27)
20
9
-
31
96
9.2
9.1
80
Propane (G31)
37
7
-
30
91
10.8
10.8
80
MODULEX EXT: 116
Type of Gas
Supply Press.
Ø noz-
zles
collector
fan speed
co
2
levels
Start.
power
[mbar]
(mm)
[mm]
min fl
max fu
[%]
[%]
min
max
IG
nat. gas (G20)
20
7
-
31
76
9.1
9.1
80
nat. gas (G25)
25
9
-
31
76
9.1
9.1
80
nat. gas (G27)
20
9
-
31
96
9.2
9.1
80
Propane (G31)
37
7
-
30
74
10.8
10.8
80
1
- Close the flue gas inspection inlet (1) with the specific cap
(2 - 3)