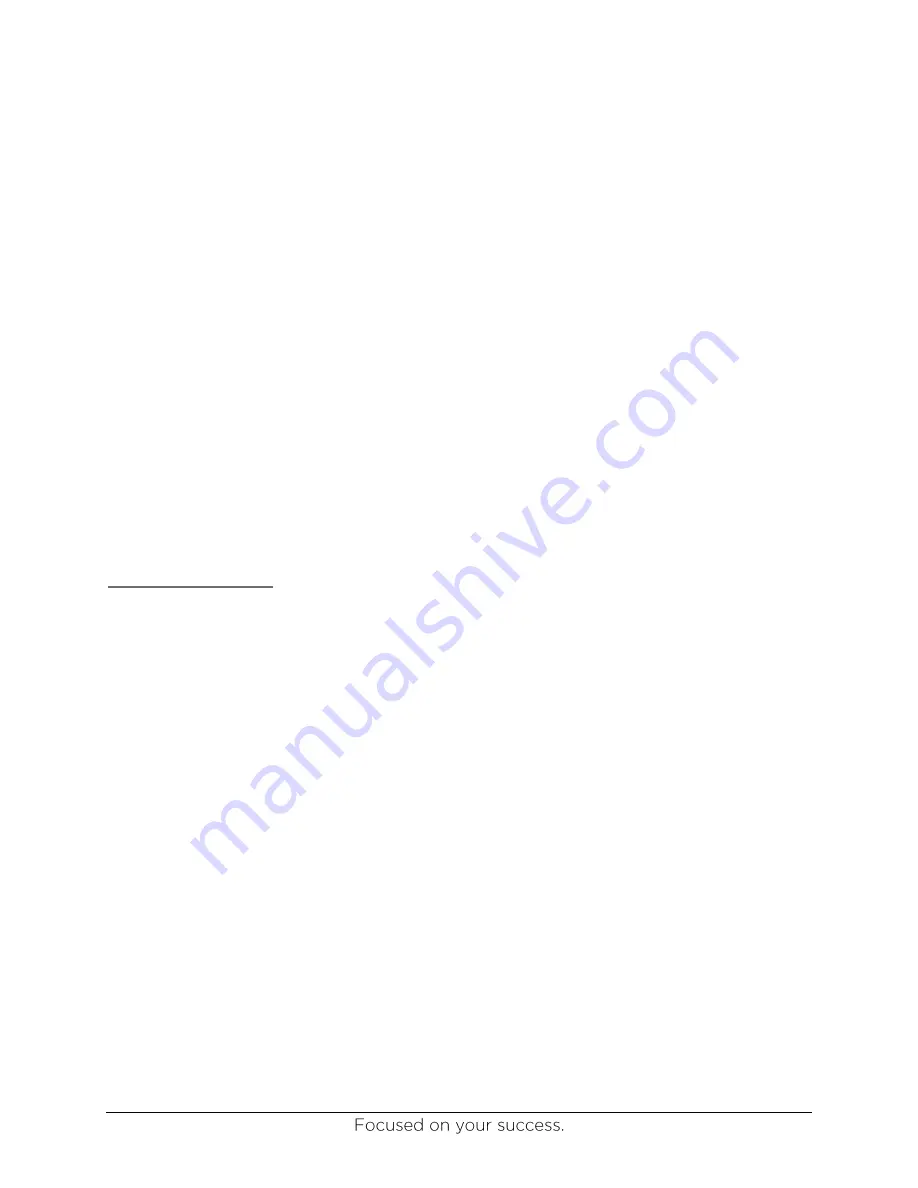
www.ultraoptics.com
page 1
Required Utilities
The following facility utilities are required to operate the 44R. The provisions for these facilities
are the responsibility of the customer and are not included in the scope of supply for this
machine.
Electrical Power
: 220 VAC, single phase, 4-wire (NEMA L14-30), 30 amp circuit.
Compressed Air
: 80 psig, 18 cfm. The connection on the machine is a 1/4
” quick
connect
Deionized Water
: Consumption of 7.6 L/hr at periodic rates of 0.3 L/min of deionized
water flow rate with
≥ 1 megaohm resistivity. The connection on the
machine is 3/8
” barbed fitting.
Water Drain
: Accessible floor drain required within 30 feet of machine.
System Overview
General Overview
The 44R is the latest back-side hard coat machine from Ultra Optics and represents the state-
of-the-art solution for the optical
industry. The system’s basic functions are based on the highly-
touted robustness of our MR3. The MR3 has been reliably coating lenses for customers for
over 15 years.
In addition to the MR3
’s well-proven coating process technology, the 44R brings system
automation. This innovative system utilizes an industrial standard robotic arm to automatically
load/unload lenses from the trays into the coating machine. The lenses, while still on the block,
are brought to the machine in the standard trays via a conveyor system. The incoming trays
have a work ticket with a bar code that the 44R system will read. This barcode will dictate to the
machine whether or not to coat the lens as well as making sure each lens is returned to its
respective tray. The automated loading process reduces work handling, increases through-put,
and lowers over-all operating costs.
The yield of the process is improved by incorporating the advances recently introduced as part
of our Ultra OTB coating machine. These process improvements include:
Hot water wash
– using hot water to wash the lens improves the system’s ability to
remove any contaminants such as dirt, dust or residual polish material. A completely
clean lens is a fundamental requirement to obtaining a successful coating application.
Water quality monitoring
– our many years of experience have taught us that if the
quality of the de-ionized water starts to diminish, so does the effectiveness of cleaning
the lens. Rather than wait for evidence of poor water to show up in the form of lens