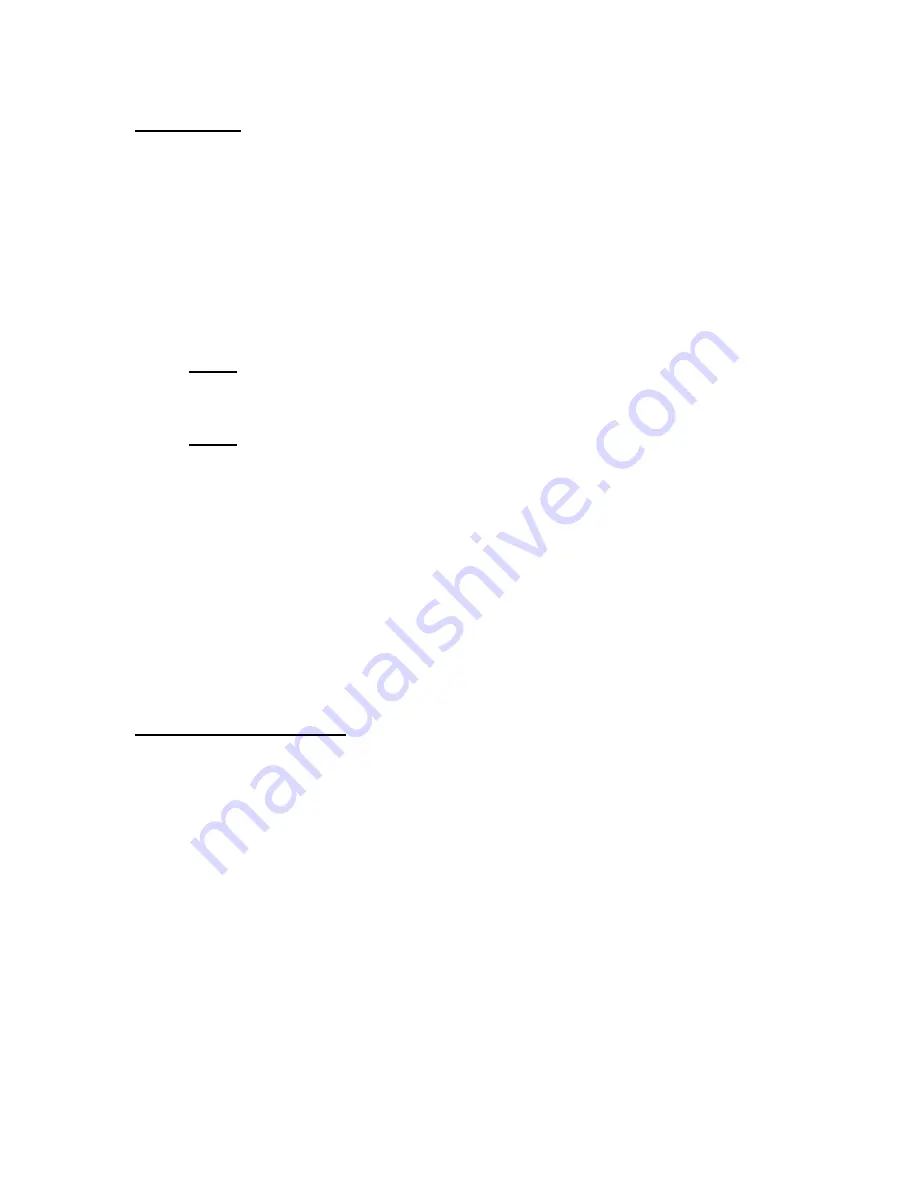
41
41
Grain Filler
Grain filler is used on open pore woods like mahogany to raise the low areas
of the pores and help to level the final finish and not see waves.
The color grain filler used can either be used to simply level the pores or
used to highlight the pores with a contrasting color like black. The latter
creates a visually deep, rich look to the surface of the neck and headstock.
If you built a Sapele guitar, this can also be done on the back and sides.
Note:
Do not apply grain filler to the surface of the fingerboard. This
should already be taped/masked off at this point.
Note:
NEVER apply grain filler to the top of either of the guitars. This
would be incorrect. There are NO deep pores to fill on Cedar or
Spruce.
Before applying grain filler, many professional finishers will use a sealer
coat of shellac on the surface and letting it dry before applying the grain
filler. This will prevent the moisture in the filler from swelling the wood and
creating cracks in the finish later.
Once the grain filler has dried completely, sand the excess off and wipe the
surface with a clean rag.
Nitro-Cellulose Lacquer
The most common finish seen on most production guitars today is nitro-
cellulose lacquer.
It is typically sprayed in a very specific environment with many precautions
taken to comply with the product safety requirements.
This should not be taken lightly as there are significant health and safety
concerns as well as strict laws enforcing proper methods of use and disposal.
USGK offers finishing products from the Behlen company that can produce
excellent results when used properly and in accordance with safety and
application procedures. Products include vinyl sealer and instrument lacquer
for the finish. They also have a full set of rub out products to bring a super
glossy finish to your guitar. You can also use super high grit wet polishing