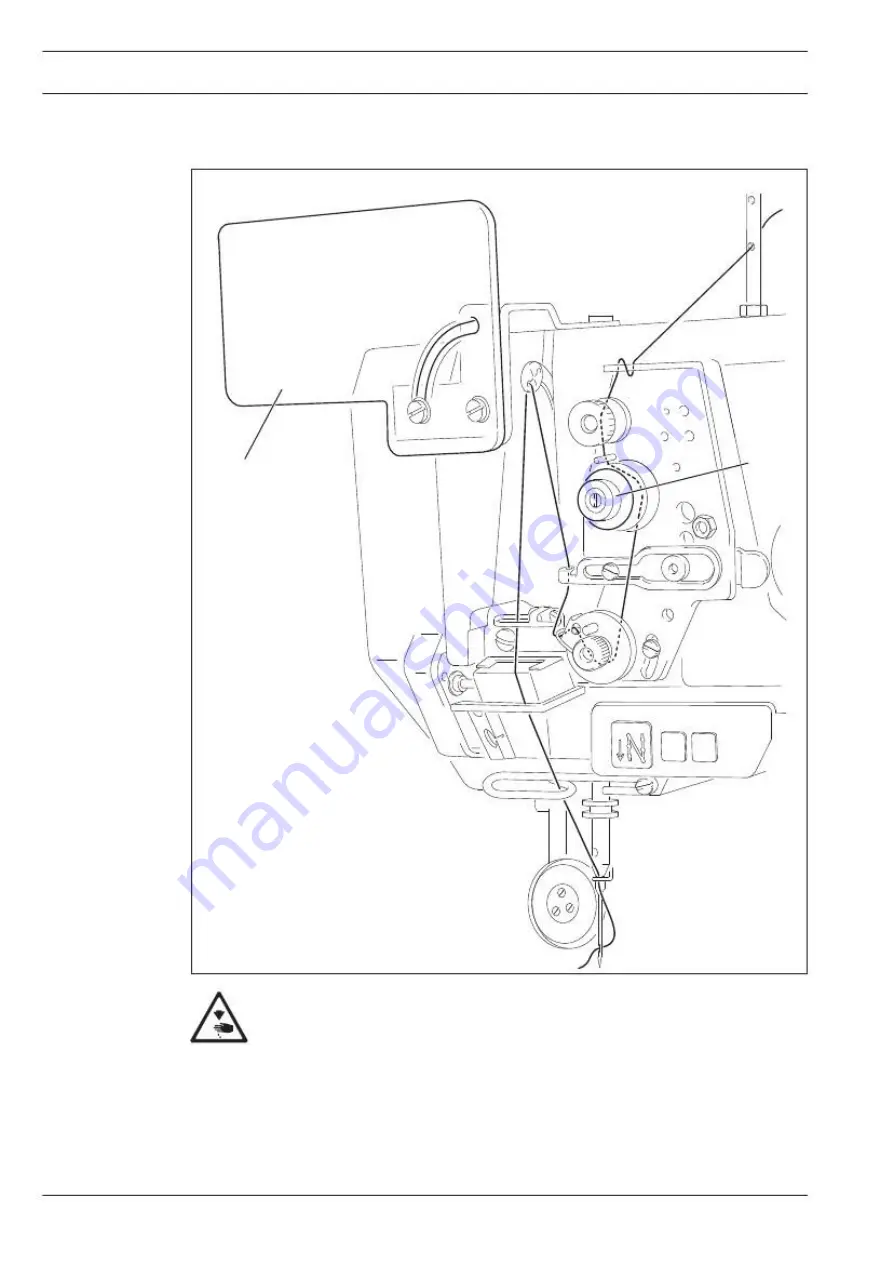
Setting up
9
.05
Threading the needle thread and regulating its tension on
model 571 and 591
1
2
Fig. 9 - 05
129-037
Switch the machine off!
Danger of injury if the machine is started accidentally!
● Tilt up the eye guard
1.
● Thread the needle thread as shown in Fig.
9-05.
● On model
571
the needle is threaded from the
right to the left,
and on model
591
from
the
left to the right.
● Adjust the needle thread tension by turning milled screw
2.
34