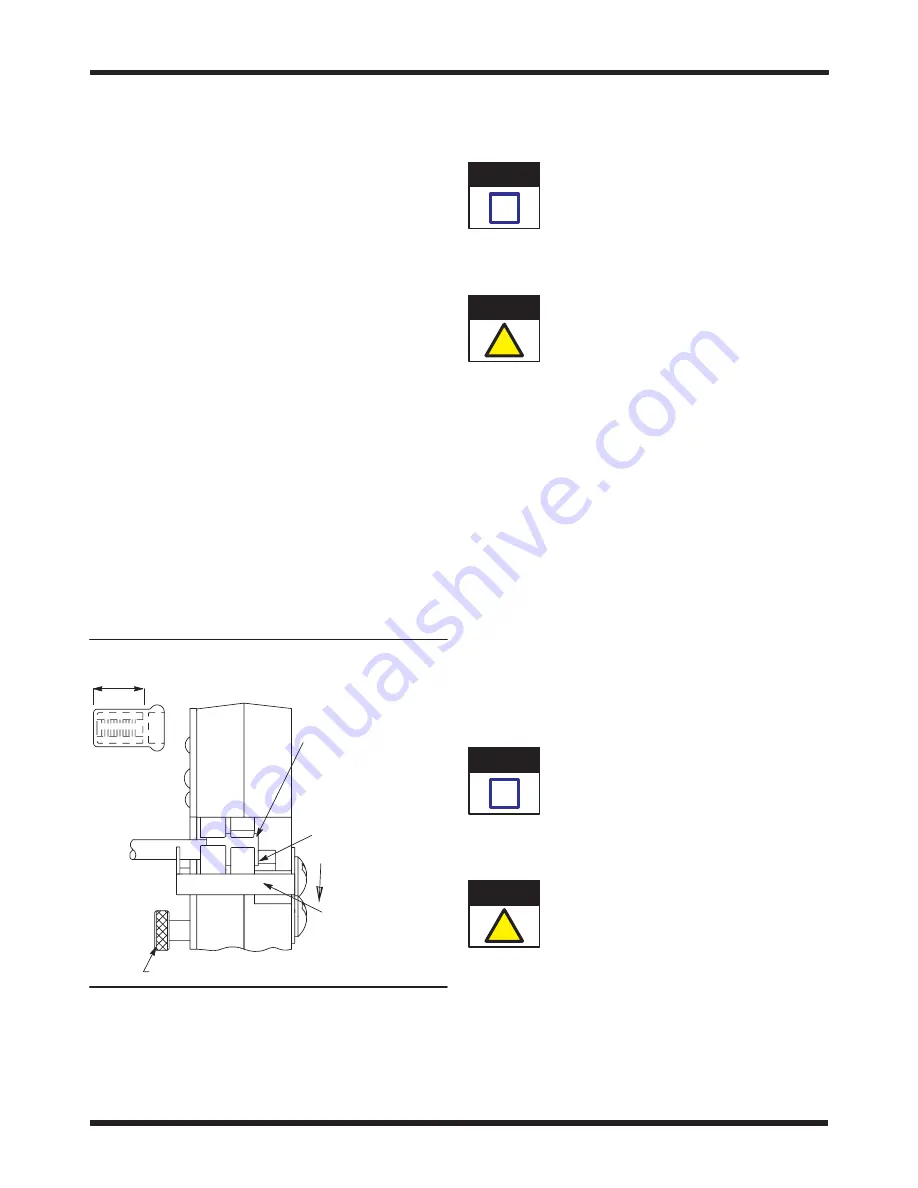
408-1261
HHHT 59239-4, 59239-8, 59287-2, and 525692
Rev F
4 of 9
Tyco Electronics Corporation
8. Inspect the crimp to make sure that it conforms
to Figures 7 and 8. Splices not meeting the
described conditions should NOT be used.
C. Spare Wire Cap
1. Place the tool insulation adjustment pins in the
Position 3.
2. Close the tool handles until the crimping dies
partially close, but leave enough space for the
spare wire cap to be inserted in the crimping
chamber.
3. Depress the locator so that the end of the spare
wire cap rests against the recessed surface of the
locator. See Figure 6.
4. Close the tool handles until the spare wire cap is
held firmly in place. Do NOT deform the spare wire
cap.
5. Insert a properly stripped wire into the spare
wire cap until the wire conductor(s) bottoms.
6. Hold the wire in position, and complete the
crimp by closing the tool handles until the ratchet
releases.
7. Release the tool handles, allow the handles to
open FULLY, and remove the crimped spare wire
cap.
8. Inspect the crimp to make sure that it conforms
to Figures 7 and 8. Spare wire caps not meeting
the described conditions should NOT be used.
Figure 6
Crimping a Spare Wire Cap
Wire Conductor(s)
Bottomed in
Spare Wire Cap
Insulation Adjustment Pin in Position 3
Locator
Depressed
B" Equals Wire Barrel
B"
End of Spare Wire Cap
Against Recessed
Surface of Locator
4. INSULATION CRIMP ADJUSTMENT
The insulation crimping section of the hand tool has
three positions: 1 (tight), 2 (medium), and 3 (loose).
To adjust the grip resulting from the crimp of the
insulation barrel, proceed as follows:
4.1. PIDG Terminal and Splice
PIDG terminals and splices feature a wire
insulation grip.
1. Insert each insulation crimp adjustment pin into
Position 3. Refer to Figure 1.
Make sure that both insulation crimp adjustment
pins are in the same position.
2. Place the terminal or splice into the crimping
chamber as described in Section 3.
3. Insert an UNSTRIPPED wire into ONLY the
insulation barrel of the terminal or splice.
4. Close the tool handles until the ratchet releases.
5. Release the tool handles, and allow the handles
to open FULLY. Remove the crimped terminal or
splice.
6. Check the insulation barrel crimp by bending the
wire back and forth once. The terminal or splice
should retain its grip on the wire insulation. If it
does not, insert each insulation crimp adjustment
pin into the next position (Position 2).
7. Repeat Steps 2 through 6 until the correct
insulation barrel grip is attained. DO NOT use a
tighter position than is necessary.
4.2. PLASTI-GRIP Terminal
PLASTI-GRIP terminals and splices feature a
wire insulation support" only. Ideally, the terminal
orsplice insulation should be in contact with the
wire insulation.
Insert each insulation crimp adjustment pin into
position according to the following:
Make sure that both insulation crimp adjustment
pins are in the same position.
— Position 3 for wire having a large insulation
diameter.
— Position 2 for wire having a medium insulation
diameter.
— Position 1 for wire having a small insulation
diameter.
NOTE
i
CAUTION
!
NOTE
i
CAUTION
!