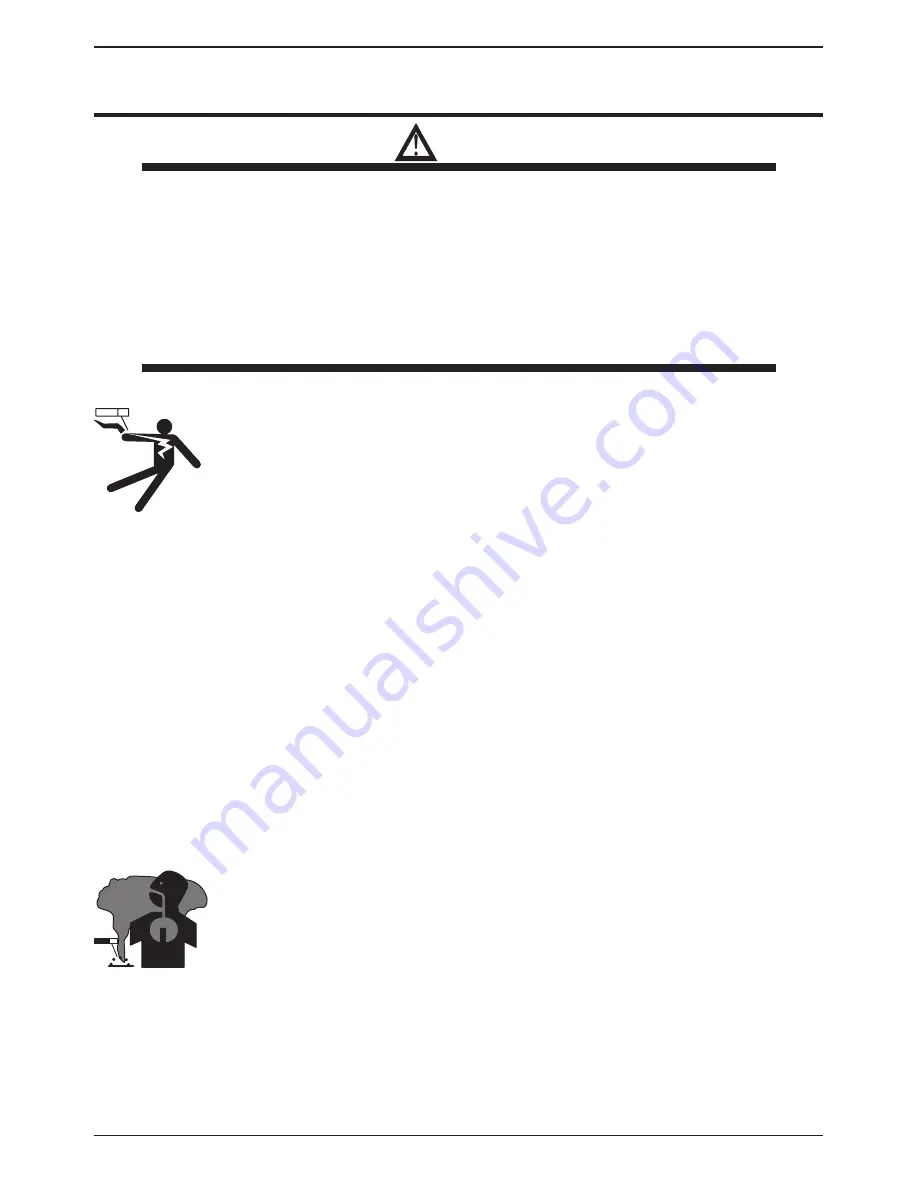
SET-UP AND SAFE OPERATING PROCEDURES
1-1
89210007
Safety Precautions
SECTION 1:
SAFETY PRECAUTIONS
WARNING
SERIOUS INJURY OR DEATH
may result if welding and cutting equipment is not properly
installed, used, and maintained. Misuse of this equipment and other unsafe practices
can be hazardous. The operator, supervisor, and helper must read and understand the
following safety warnings and instructions before installing or using any welding or cutting
equipment, and be aware of the dangers of the welding or cutting process. Training
and proper supervision are important for a safe work place. Keep these instructions for
future use. Additional recommended safety and operating information is referenced in
each section.
ELECTRIC SHOCK CAN CAUSE INJURY OR DEATH
Install and maintain equipment in accordance with the National Electrical Code (NFPA
70) and local codes.
Do not
service or repair equipment with power ON.
Do not
operate
equipment with protective insulators or covers removed. Service or repair to equipment
must be done by qualified and/or trained personnel only.
Do not
contact electrically live parts.
Always
wear dry welding gloves that are in good
condition. Aluminized, protective clothing can become part of the electrical path. Keep oxygen cylinders,
chains, wires, ropes, cranes, and hoists away from any part of the electrical path. All ground connections
must be checked periodically to determine if they are mechanically strong, and electrically adequate for
the required current. When engaged in AC welding/cutting under wet conditions or where perspiration
is a factor, the use of automatic controls for reducing the no load voltage is recommended to reduce
shock hazards. Accidental contact must be prevented when using open circuit voltage exceeding 80
volts AC, or 100 volts DC by adequate insulation or other means. When welding is to be suspended for
any length of time, such as during lunch or overnight, all electrode holders and electrodes should be
removed from the electrode holder and the power supply should be turned OFF to prevent accidental
contact. Keep MIG-Guns, electrode holders, Tig torches, Plasma torches, and electrodes away from
moisture and water.
See safety and operating references 1, 2, and 8.
SMOKE, FUMES, AND GASES CAN BE DANGEROUS TO YOUR HEALTH
Ventilation must be adequate to remove smoke, fumes, and gases during operation to
protect operators and others in the area. Vapors of chlorinated solvents can form the
toxic gas “Phosgene” when exposed to ultraviolet radiation from an electric arc. All
solvents, degreasers, and potential sources of these vapors must be removed from the
operating area. Use air-supplied respirators if ventilation is not adequate to remove all
fumes and gases. Oxygen supports, and vigorously accelerates fire and should
never
be used for
ventilation.
See safety and operating references 1, 2, 3, and 4.