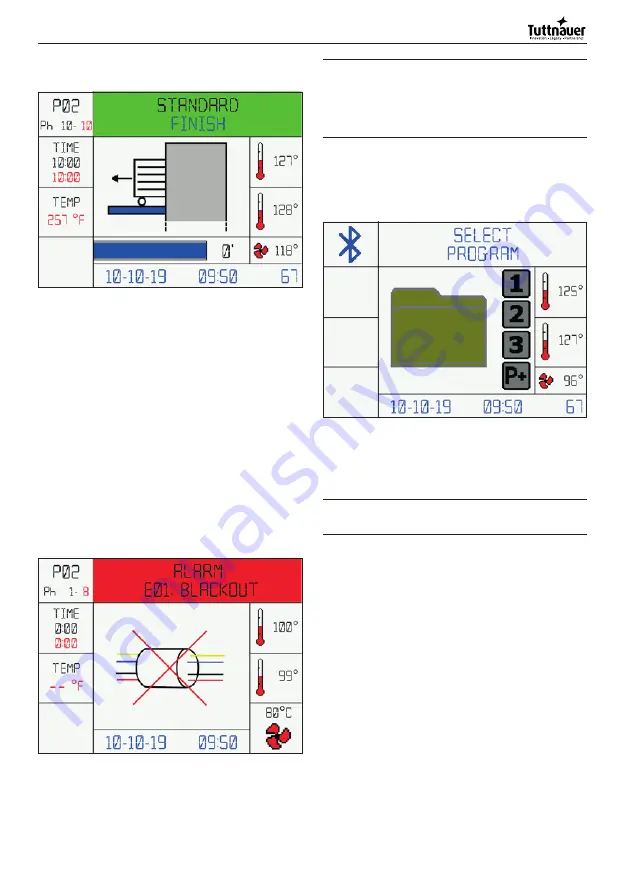
31
Operative Instructions
21) End of the «STANDARD» cycle. Open the door and
remove the rack.
Fig. 18.22
If, for any reason, it is necessary to interrupt the cycle,
simply hold down the RESET key for a few seconds until
an audible alarm (buzzer) is heard and an alarm screen
appears on the display.
Once the problem is resolved, resume the cycle from
the beginning. If the problem cannot be solved, contact
the technical assistance.
7.2.5 Alarm messages
The machine is equipped with an alarm system that
indicates malfunctions detectable with an audible
signal (buzzer), a screen on the graphic display of the
control panel and a red led light in the camber.
At first the image concerning the alarm is displayed (for
5 seconds); then the alarm description is displayed (for
10 seconds).
The image and text alternate until the alarm is reset.
Fig. 19
If the program is interrupted because of an alarm, the
display will show the message «Program interrupted
stop-alarm». Follow the message shown on the display
to reset the alarm.
Ö
IMPORTANT NOTE! If the RESET button is
pressed during the wash cycle, the program
is interrupted and an alarm is displayed with
the message
«Program interrupted
stop -
user
»
. Press RESET to return to initial display.
For the alarms, description and possible solutions see
Annex 12.6.
7.2.6 User settings menu
Start screen
Fig. 20.1
To access the settings menu the procedure is as follows:
Open door -> PRG key for 5 seconds -> If the user and
password are enabled, insert user password.
Ö
IMPORTANT NOTE! USER PIN MANAGEMENT
option on request.
The keys and their operation are shown below,
contextualised according the menu in which you are
located:
- Use P1 and P2 to navigate up and down the menu.
- Press START to access the entry of the menu selected.
- Within the parameter, use the 1 and 2 keys to change
the value of the highlighted parameter.
- Press START to go to the next parameter.
- Press PRG to return to the previous menu.
Summary of Contents for TIVA8-L
Page 55: ...55 Operative Instructions...