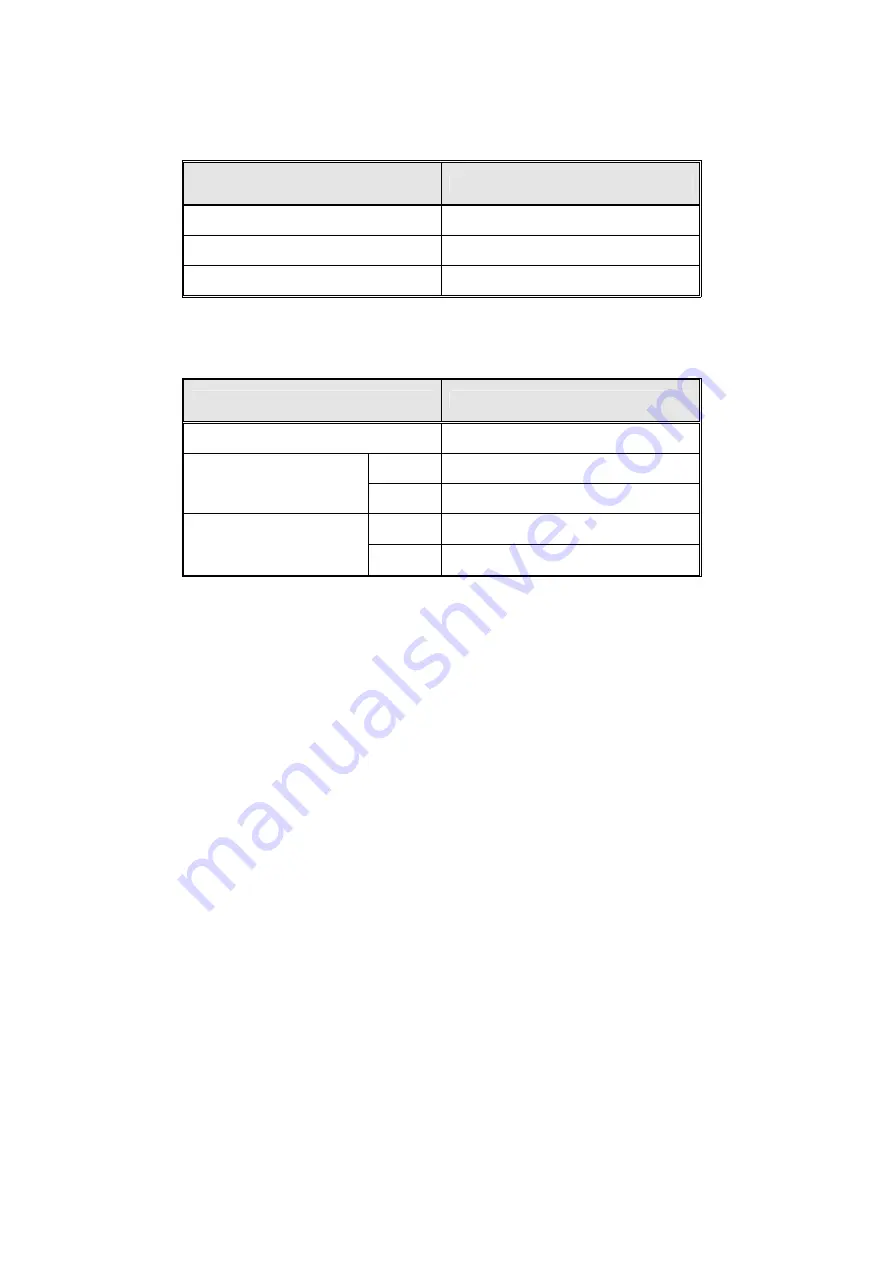
Page 75 of 75 Pages
15.
SPARE PARTS LIST
Description
Cat. No.
Cap for ¼” strainer
FIL175-0027
Strainer element
FIL175-0046
Teflon gasket 4 mm
GAS082-0008
16.
ACCESSORIES
Description
Cat. No.
Printer, PLUSII-S2B-0004
THE002-0052
Stainless steel wire
basket
High
BSK387-0001
Low
BSK387-0002
Stainless steel container
for waste products, with
vents holes
High
BSK387-0005
Low
BSK387-0003
Summary of Contents for 3840 ELVG-D
Page 2: ......
Page 17: ...Page 15 of 75 Pages OVERALL DIMENSIONS DRAWING mm...