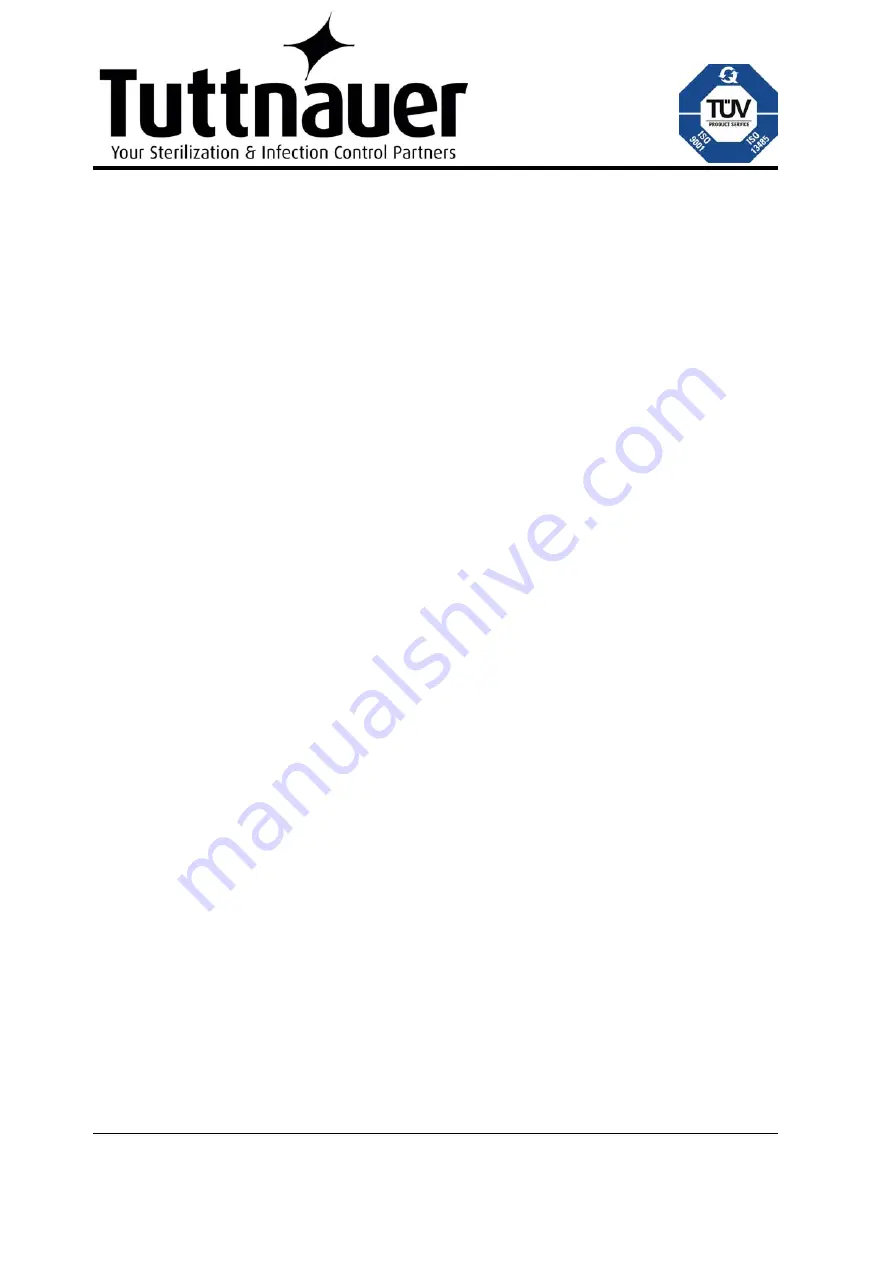
www.shanghaidelan.com
TECHNICIAN
MANUAL
E-type Electronic Table -Top Autoclaves
models 1730, 2340, 2540, 3140, 3850, 3870
E, EK, EA & EKA
Cat. No.
MAN205-0064000EN Rev. H
Tuttnauer Europe b.v., Paardeweide 36, 4824 EH, Breda, P.O. Box 7191, 4800 GD Breda, Netherlands.
+31/76-5423510,
Fax:
+31/76-5423540
Summary of Contents for 1730EK
Page 2: ...w w w s h a n g h a i d e l a n c o m...
Page 29: ...w w w s h a n g h a i d e l a n c o m 27 Electronic box 1730 Electronic box 2340 2540 7...
Page 30: ...w w w s h a n g h a i d e l a n c o m 28 Electronic box 3140 3850 3870...
Page 78: ...w w w s h a n g h a i d e l a n c o m 76 FRONT VIEW Model 2340 2540 Model 1730...
Page 80: ...w w w s h a n g h a i d e l a n c o m 78 VESSEL ASSEMBLY...
Page 82: ...w w w s h a n g h a i d e l a n c o m 80 OUTER CABINET ASSEMBLY...
Page 103: ...w w w s h a n g h a i d e l a n c o m 101 PIPING DIAGRAM FOR MODELS 1730 E AND EK...
Page 104: ...w w w s h a n g h a i d e l a n c o m 102 PIPING DIAGRAM FOR MODELS E AND EK EXCEPT 1730...
Page 105: ...w w w s h a n g h a i d e l a n c o m 103 PIPING DIAGRAM FOR MODELS EA AND EKA...
Page 106: ...w w w s h a n g h a i d e l a n c o m 104 ELECTRICAL WIRING DIAGRAM MODELS 1730 120 230V...
Page 107: ...w w w s h a n g h a i d e l a n c o m 105 ELECTRICAL WIRING DIAGRAM MODELS 2340 2540E 120 230V...
Page 109: ...w w w s h a n g h a i d e l a n c o m 107 ELECTRICAL WIRING DIAGRAM MODELS 3140E 230V...
Page 110: ...w w w s h a n g h a i d e l a n c o m 108 ELECTRICAL WIRING DIAGRAM MODELS 3870 3850E 120 230V...