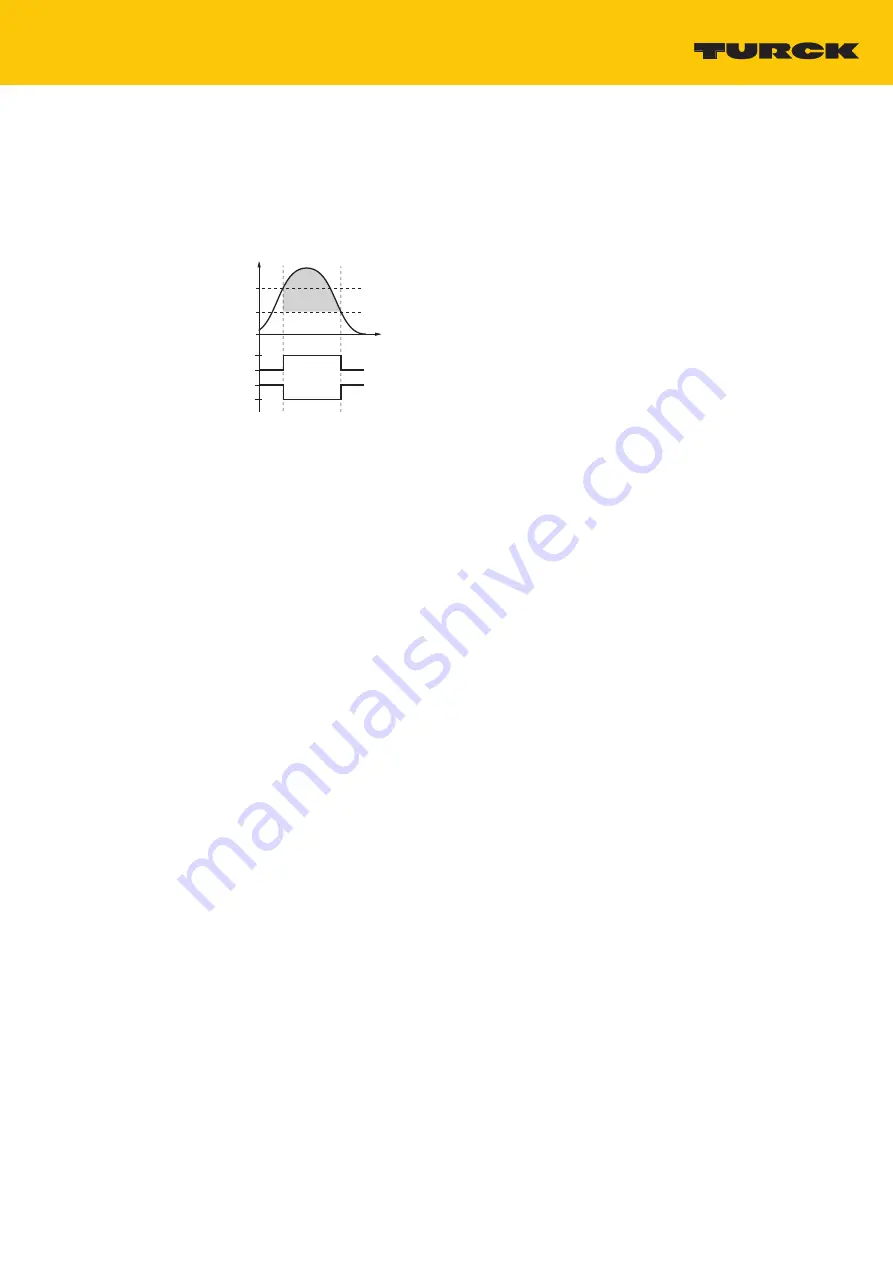
V01.00 | 2021/07
11
Hysteresis function
The hysteresis function is used to teach in a stable switching state that is not affected by sys-
tem-related fluctuations and the defined setpoint. The switching range is defined with a
switching point and a reset point. The minimum hysteresis is 0.5 % of the measuring range. If
the switching point is changed, the reset point is automatically adjusted.
P
SP
1
rSP
t
0
1
0
Hno
Hnc
Hysterese
hysteresis
Fig. 6: Behavior of the switching output – hysteresis function
4.5.5
Output functions – analog output
The analog output of the LRS…LI2UPN8 sensors can be set as either a current or voltage
output. The measuring range can be defined as required.
The minimum distance between the start and end point is 500 mm.
Current output
In the defined measuring range between ASP (analog start point) and AEP (analog end point),
the device supplies an analog current signal. The following output configurations can be set:
n
4…20 mA (factory setting)
n
0…20 mA
n
20…4 mA
n
20…0 mA
Voltage output
In the defined measuring range between ASP (analog start point) and AEP (analog end point),
the device supplies an analog voltage signal. The following output configurations can be set:
n
0…10 V (factory setting)
n
0…5 V
n
1…6 V
n
0.5…4.5 V
n
10…0 V
n
5…0 V
n
6…1 V
4.5.6
IO-Link mode
The devices must be connected to an IO-Link master for operation in IO-Link mode. If the port is
configured in IOL mode, bidirectional IO-Link communication is provided between the IO-Link
master and the device. For this the device is integrated in the controller level via an IO-Link
master. The communication parameters are exchanged first of all; the cyclic data exchange of
the process data (process data objects) then starts.