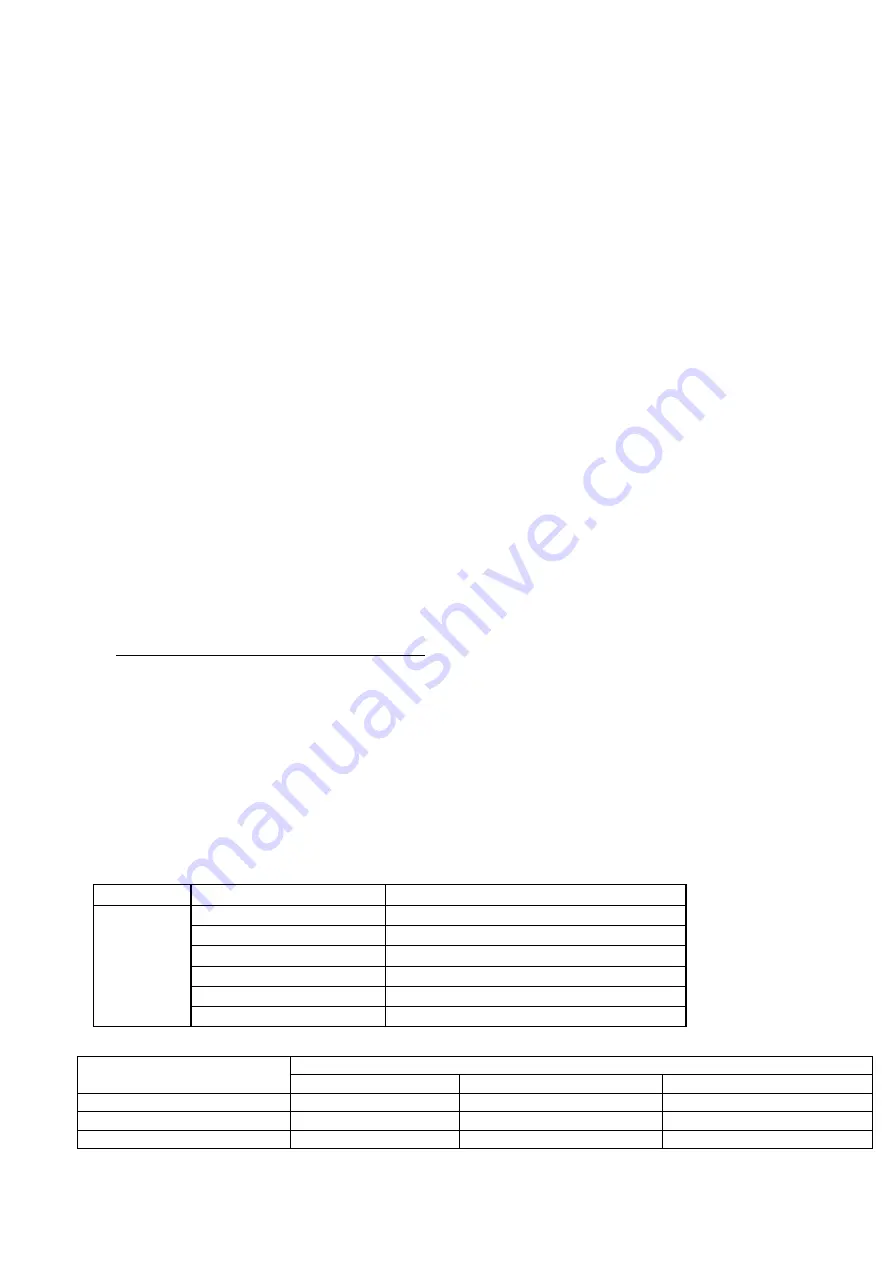
5
by specific load and installation conditions. Also, install a mechanical
stopper within the stroke range in case of emergency.
4. Operation
1.
Be sure that the dynamic or static load carried or sustained by jack does not exceed its capacity.
2.
Make sure that the surface temperature of the housing does not exceed temperature of -15ºC to 80ºC
during operation. If using a traveling nut type unit, measure the traveling nut surface temperature.
3.
The maximum input speed is 1800 rpm as long as the input power dose not exceed the unit’s maximum
allowable input power.
4.
Do not operate continuously. Maximum allowable input power ratings are based on a 20% duty cycle per
30 minutes for the JWM (Machine Screw Type) and 30% for the JWB (Ball Screw Type) and JWH (High
Lead Ball Screw Type). Duty cycle (%) per 30 min. can be calculated using the following formula: (30min.
- off time per cycle) / 30 X 100. For operation longer than that mentioned above or for any continuous
operation, the jacks temperature must be monitored and should not exceed 80ºC max. in order to
determine its duty cycle.
5.
Be sure that starting torque is 200% or more of required running torque.
6.
Be sure that ample driving power is available to drive the jack when using in temperatures below 0ºC.
Low temperatures decrease the jack’s efficiency due to the increased grease viscosity inside the gear
box.
7.
Although JWM has self-locking feature, vibration and shock may affect its efficiency, in which case a
brake unit is required. JWB and JWH must have brake units that over power their holding torque because
of their extremely high efficiencies.
8.
Never approach or touch the rotary parts (input shaft, etc.) or the screw during operation.
5. Maintenance and inspection
1. The jack is shipped prepacked with grease. Recommended grease brands are shown in Table 3. Under
normal operation, lubrication is required every 6 months, however, this interval may vary as frequency of
use and conditions change. Severe operating conditions will require a self-lubricating system. See Table
4 for the lubrication cycle.
※
In case of the made-to order type, confirm with the final drawing, used grease might not be same as
standard.
2. When lubricating the screw, use a brush to spread the grease on the screw after the old grease has been
removed. See Table 5 for the amount of grease to be applied.
Jack operating cycle
Lubricating Cycle
Machine screw
Ball screw
Gear housing
50 to 100 times / day
1 month
3 months
3 months
10 to 50 times / day
3 month
3 to 6 months
3 to 6 months
1 to 10
times / day
6 mo.s to 1 yr.
6 mo.s to 1 yr.
6 mo.s to 1 yr.
Part
Maker
Grease
Shaft
Reducer
Unit
Tsubakimoto Chain
JWGS
Idemitsu Kosan
※
Daphne Eponex Grease SR No.1
Nippon Grease
Niglube EP-1K
Exson Mobile
Mobilux EP No.1
Cosmo Lubricants
Cosmo Grease Dynamax EP No.1
Showa Shell
Shell Alvania EP Grease 1
Table 3. Recommended Grease
※
Daphne Eponex
is prepacked.
Note: JWGS100G is
available in 100g tube.
Table 4. Lubrication Intervals
★