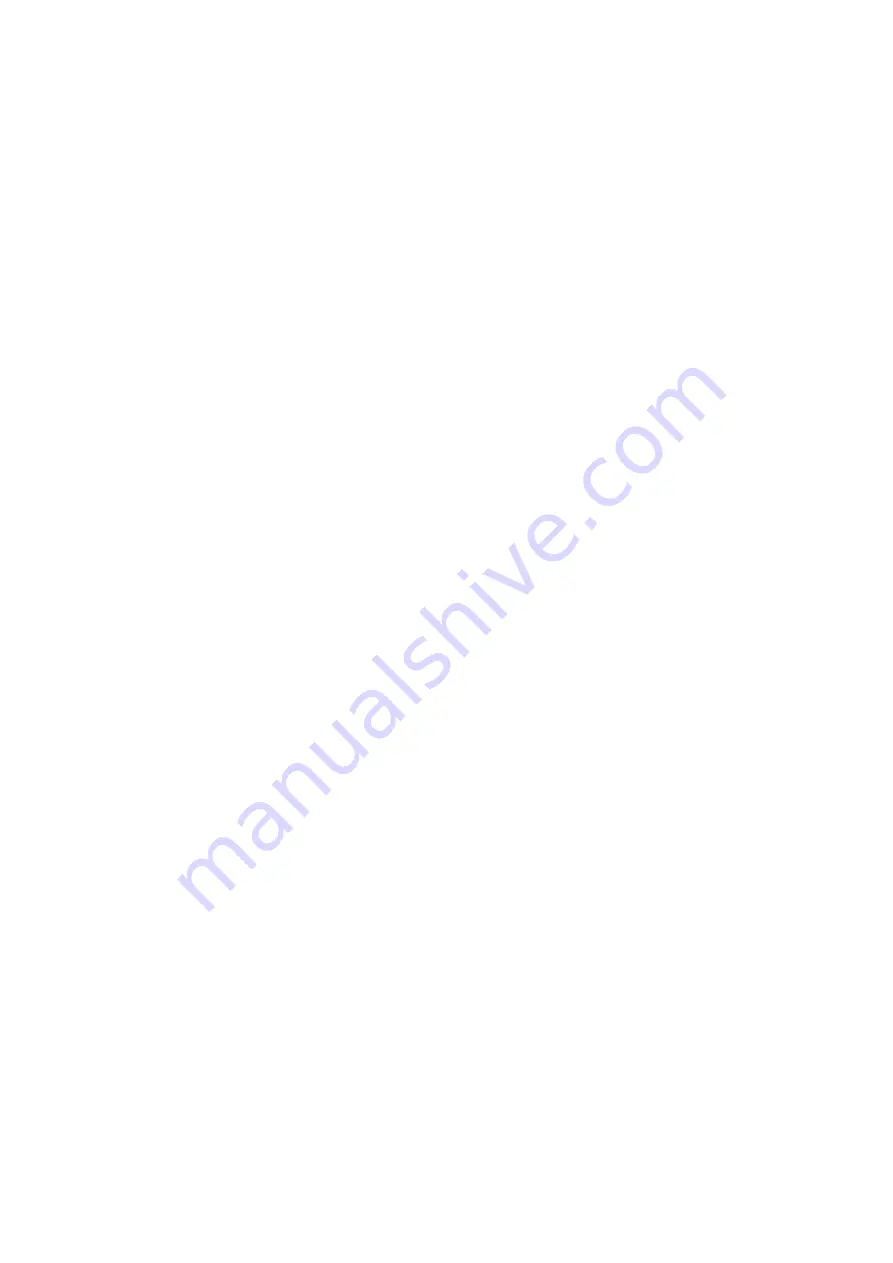
21
4. Apply anti-loosening liquid to 2 HSHCS’
③
, then affix the brake plate
⑤
at a tightening torque of 294 to
392 N
・
cm {30 to 40 kgf
・
cm}.
5. Turn on the power source, and make sure the brake works normally. If the gap is small, the armature
⑥
will make contact with the lining
⑦
when it’s turning. Re-adjust the gap in this case.
6. Affix the brake cover packing
⑧
to the matching surface of the brake cover, then fasten to the motor with
4 HSHCS’
①
.
(Note) In case the brake cover packing develops a crack or is cut, change to new packing or apply sealing
agent to maintain sealing performance.
When the grooves in the break lining wear out, it is no longer effective
.
(2) Manual release operation
Conduct the following in the case the brake is released manually without turning on the brake power.
Never apply any load to the screw shaft when manually releasing it.
1. Loosen the (2) nuts
⑩
until they come in contact with the head of the bolt.
2. By screwing the (2) bolts
⑨
in evenly, the tip of the bolt will make contact with the armature
⑥
, causing
it to suddenly become heavy and thus releasing the brake.
Note: Forcefully screwing in the bolts may deform the armature or damage the bolts and/or the tap
holes at brake cover.
3. With the above-mentioned operation, when the brake lining
⑦
separates from the armature
⑥
, the
braking force ablates.
4. When resetting to the original brake operation state, loosen the brake cover bolts
⑨
and return to their
original position. Move the nut
⑩
to its original position and tighten. Once finished, conduct a test run
to ensure the brake is running as normal.
Note: Make sure the nut
⑩
is tightened properly to ensure a good seal.