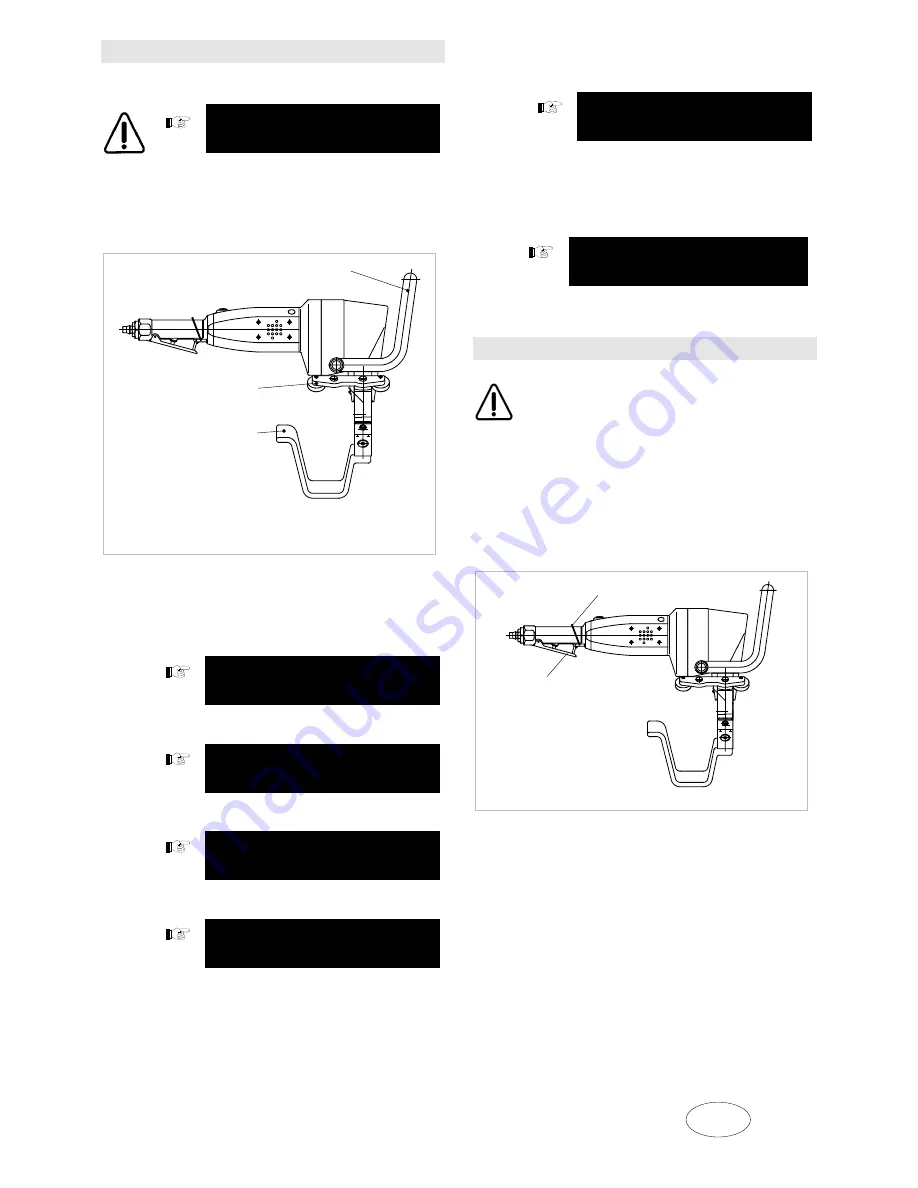
E254en1_02.doc
TKF 104 - 1
GB
3
Before initial use
1.
Read the chapter on safety.
Safety instructions
2.
Mount the handle and the roller guide, if
necessary (these parts are provided
separately when a new machine is
delivered).
Fig. 11423
3.
Check whether the installed cutting tool is
suitable for the material that is to be
machined. Use special cutting tools for high-
tensile sheets and aluminium!
Select cutting tool
4.
Sharpen or replace blunt tools.
Sharpen cutting tool
5.
Check the bevel angle.
Bevel angle
6.
Check the bevel angle (length of bevel set).
Set length of bevel angle
7.
Adjust the machine to the sheet thickness of
the workpiece.
Sheet thickness
8.
The flow pressure of the compressed air
must be 6 bar at the point of extraction.
9.
Oil lubrication must take place for the
compressed-air motor.
Maintenance
Operating instructions
Damage to property
Check the edge of the cutting tool every hour.
Check the oil lubrication of the compressed-
air motor every hour.
Never work with blunt tools!
(the compressed-air motor may stop).
Turning the unit on and off
Fig. 11424
Turning on the unit:
Push lever 1 forward (releases
compressed-air). Shift lever 2 (= motor ON). The
motor runs as long as the lever is pressed. Release
lever 1.
Turning off the unit:
Release lever 2 (the lever
springs back into initial position and the flow of
compressed air is interrupted).
58
53
38
38
Handle
53
Slide handle
58
Roller guide
1
2
1
Bracket
2
Lever
Summary of Contents for TKF 104 - 1
Page 1: ...Operator s manual english TKF 104 1...
Page 2: ......